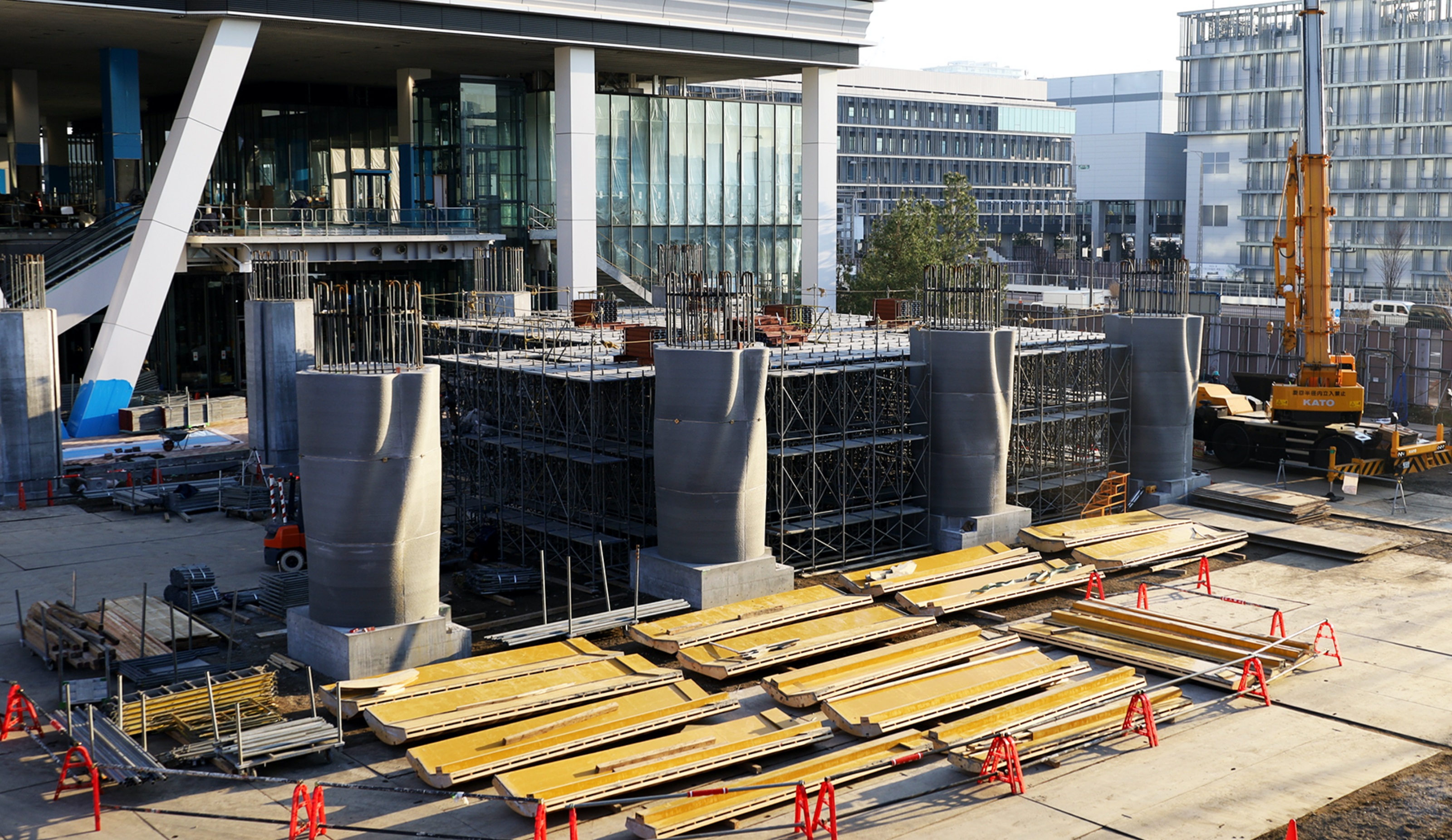
技術研究所から
3Dプリンティングで自由曲面形状の巨大柱を実現
繊維補強モルタル「ラクツム」の可能性
ラクツムを適用した曲面形状の柱
コンクリートをノズルから紐状に押し出しながら積層していく「建設3Dプリンティング」。注目されているこの分野で、シミズは独自技術の開発に成功しました。その鍵を握るのが、3Dプリンティングに最適化されたセメント系材料「ラクツム」です。
この技術を自社開発物件である「(仮称)豊洲六丁目4-2・3街区プロジェクト」に適用し、自由曲面形状を有する高さ4.2mの柱部材を構築しました。
大幅な省人化を実現する強くてしなやかなモルタル
「ラクツムは、強度と靭性(しなやかさ)を兼ね備えた3Dプリンター用の繊維補強モルタルです。主に、柱や壁の埋設型枠をプリントすることを目的に開発しました」と、担当者である技術研究所の小倉大季は語ります。
埋設型枠とは、コンクリートを打設した後に取り外すことなく、構造体の一部として使用するものを指します。
欧州、米国、中国などの海外では3Dプリンティングで構造体そのものを造る開発も進んでいますが、地震の多い日本では、鉄筋を入れて補強することが可能な埋設型枠が、現段階では現実的な適用法の一つになっています。
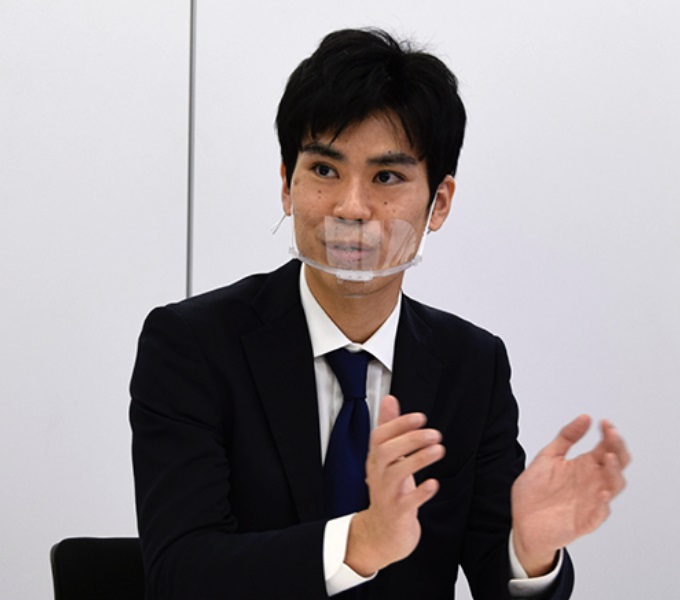
主任研究員 小倉大季
シミズが建設3Dプリンティングの開発に乗り出したのは、2つの目的がありました。一つは、建設業界の慢性的な人手不足に対応するため、もう一つは従来工法では実現が難しい形状・デザインの構造物を施工するためでした。なかでも前者の人手不足は10年後に深刻化することが予想されており、鉄筋コンクリート造の施工における省力化、省人化は喫緊の課題です。
これまでは、工場で事前に製作したプレキャスト部材の活用が有効とされてきたものの、工場から現場への運搬コストがかさむ、現場でプレキャスト部材を接合する手間がかかるといった問題がありました。これに対し、小倉は「施工場所のオンサイトで3Dプリンターによる機械化施工が可能になれば、運搬コストが削減でき、運搬に伴う部材サイズの制限もなくなり、大幅な省人化が実現します」と語ります。
別の開発で却下した配合に再び脚光を
しかし、ラクツムの開発は一筋縄ではいきませんでした。型枠のような薄い構造物を通常のモルタルを使用して3Dプリンターで造形すると、10cmほど積層した段階で形状が崩れてしまうからです。また、モルタルが固まるのに時間がかかり、思うように作業効率が上がらないという悩みもありました。
そこで、清水建設技術研究所内に専用の実験施設「コンクリートDXラボ」を新設。大型3Dプリンターを開発するとともに、実験と数値シミュレーションで、最適な材料の配合や圧送方法、プリント速度について検討しました。
「材料開発で難しかったのは、プリンターのノズルから押し出すときは流動性が高く、押し出し後はしっかりと形状を保持するという、相反する性質を両立させることでした」と小倉は振り返ります。
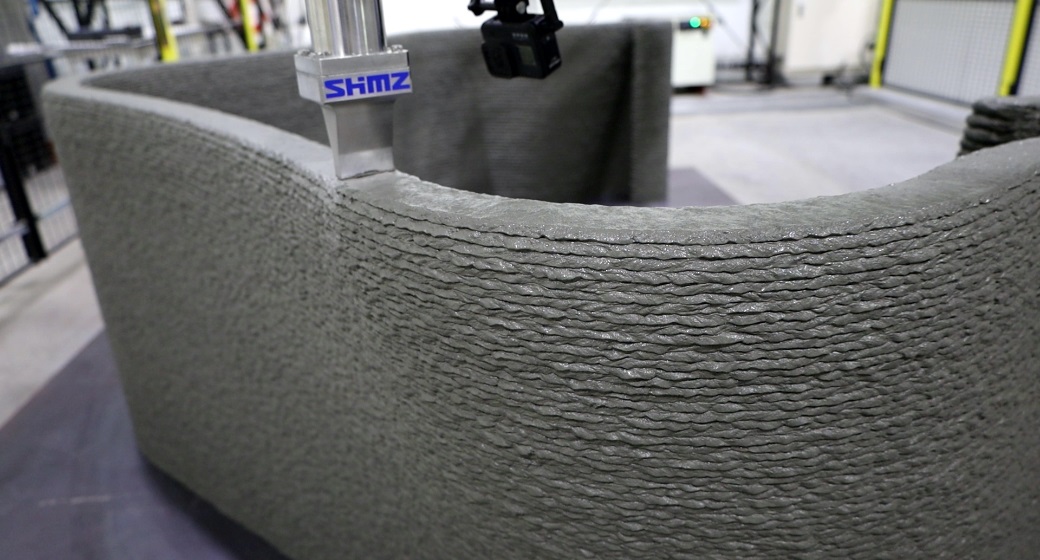
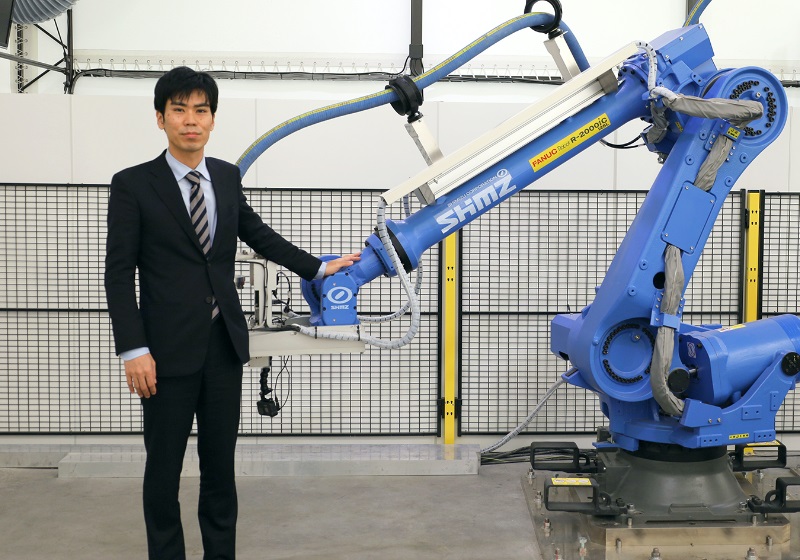
試行錯誤を繰り返す中で思いついたのが、以前に高靭性コンクリートの開発に取り組んでいた時、型枠にうまく充てんすることができずに候補から外した配合でした。「逆に3Dプリンティングにはフィットするのではないかと思いつき,実験と数値解析により検証したところ、これが積層に適した材料であることがわかりました」。この配合を足掛りに、構成材料を最適化していき、ラクツムを完成させました。
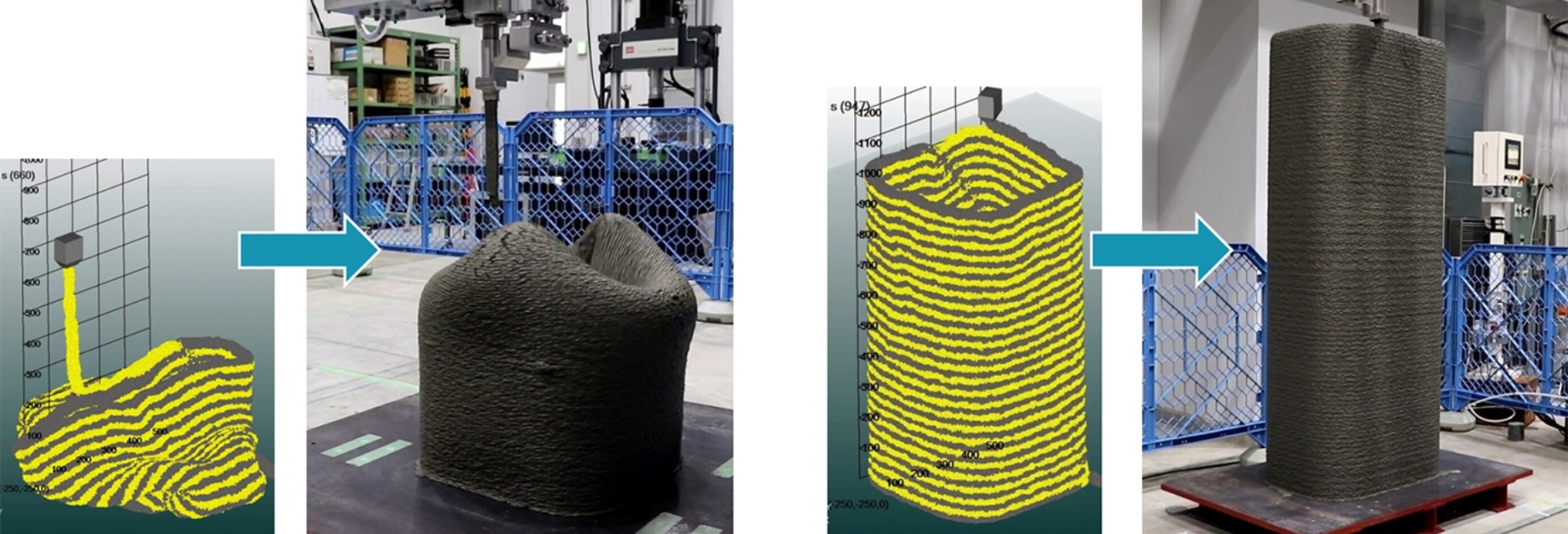
省人化、デザインの自由度向上、高い耐久性
ラクツムによる埋設型枠には、三つのメリットがあります。
一つ目は「省人化・省資源化」。実験では高さ2.1mの柱の埋設型枠を約2時間で造形でき、省力化に大きな効果が得られることが分かりました。型枠の組み立てと解体が不要になるため、省人化にも寄与します。使い捨てではないことから、産業廃棄物の削減やCO2排出量の低減に貢献するメリットもあります。
二つ目は「デザインの自由度向上」。板状の型枠と違って複雑な3次元曲面の造形が可能なため、部材のデザインの自由度が飛躍的に高まります。3Dモデルさえあれば、即座に造形物を印刷できるため、多品種小ロット生産でもコストを抑えられます。
三つ目は「高い構造性能と耐久性」です。この埋設型枠にコンクリートを充てんして造った柱の構造耐力や靭性は、既存のコンクリート柱と同等以上であることが実験で証明できました。また、プリンティングで積み上げた層の継ぎ目が密着することから、鉄筋を腐食させる水や空気が柱などの内部に侵入せず、高い耐久性を維持します。
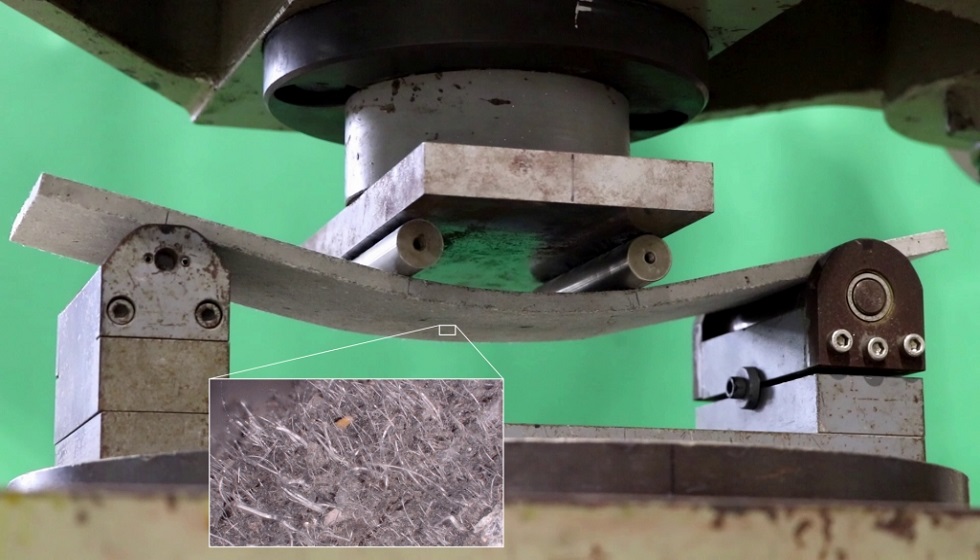

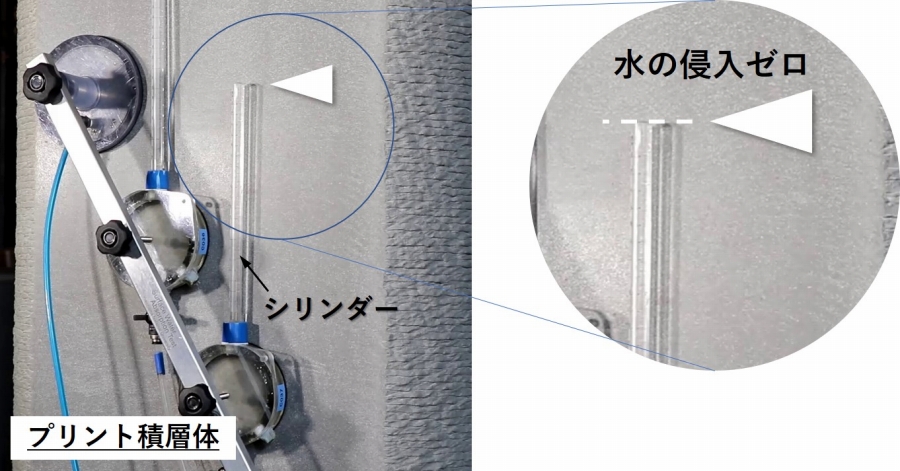
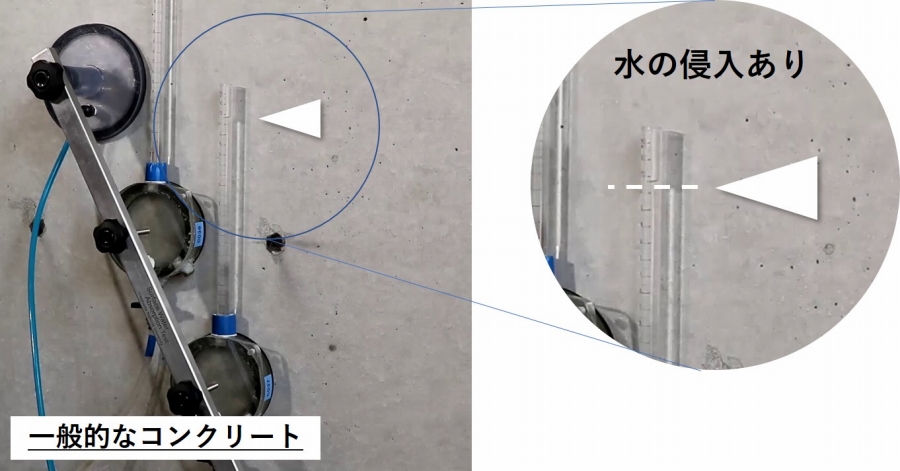
ガラスシリンダー内の水量の変化でコンクリート表面からの吸水速度を調べる試験の様子
花のように開く特殊形状の柱型枠を現場に初適用
先ごろシミズは、この技術を自社開発事業である「(仮称)豊洲六丁目4-2・3街区プロジェクト」に適用。大規模デッキを支えるコンクリート柱に特殊なデザインを採用していることから、この柱の埋設型枠を3Dプリンターで“印刷”しました。
柱は、円形の基部から花びら状の頂部へとねじれながら形が変わっていく複雑な形状。当初は直線的な柱形状で計画されていたものを、ラクツムの採用が決まってから、あえて曲面を活かしたこれまでにないデザインに変更しました。投資開発、設計、施工と全社を挙げてのチャレンジです。
施工にはまず、高さ4.2mの柱1本分の埋設型枠を水平方向に3分割、垂直方向に2分割してコンクリートDXラボで3Dプリンティング。これを現場で組み立てた後、コンクリートを打設して4本の柱を完成させました。「全部で24ピースを印刷して、不良率ゼロを達成しました」と小倉は語ります。
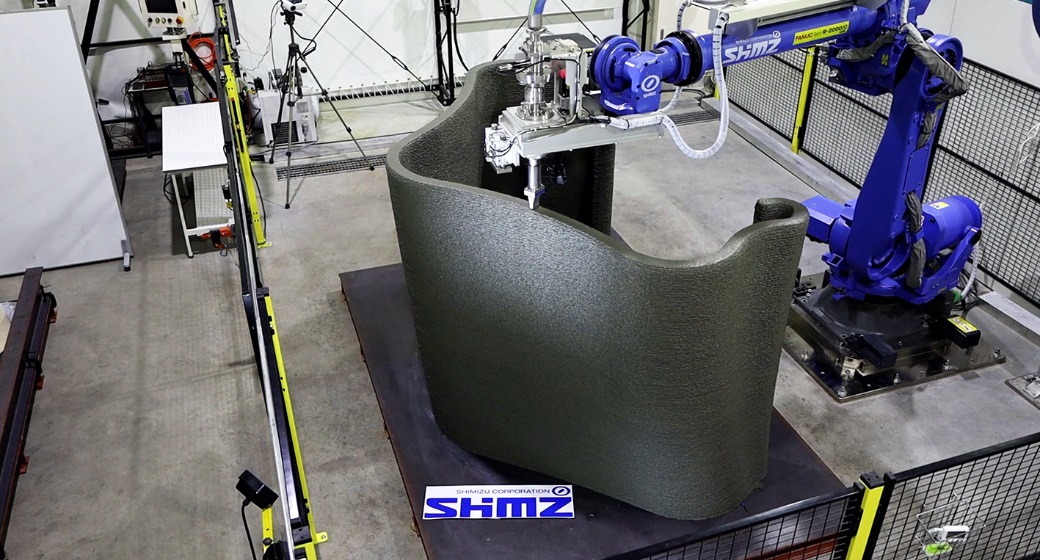
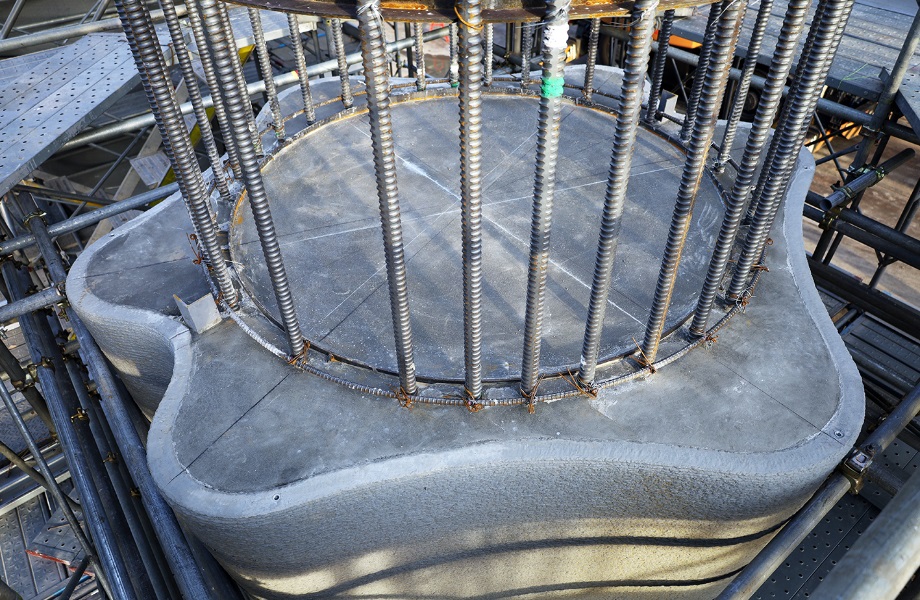
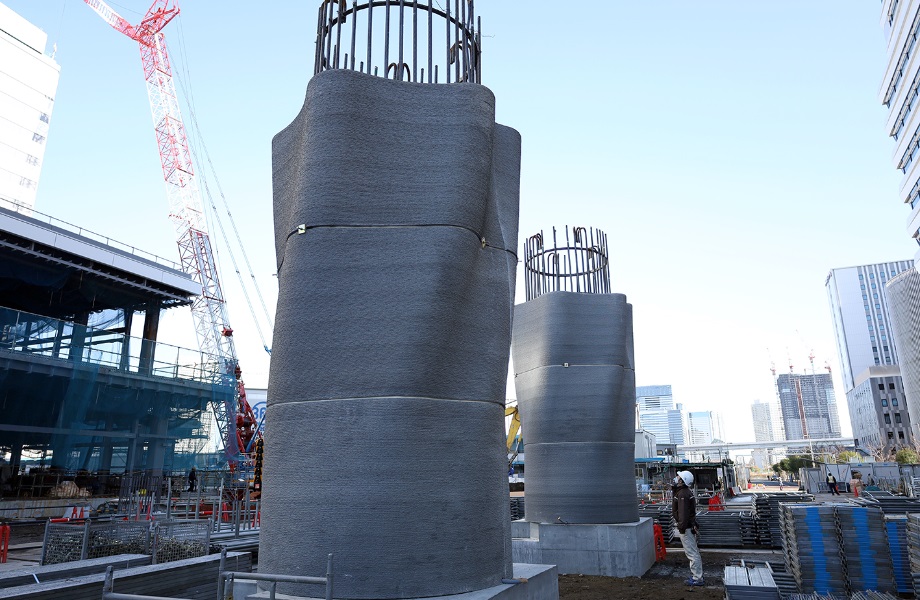
柱基部の断面は円形で、上部へ行くにしたがってねじれながら花びら型に変形していく。こうした複雑な造形ができるのも、ラクツムによる3Dプリンティングならでは
(仮称)豊洲六丁目4-2・3街区プロジェクトは、オフィス棟とホテル棟、そして高速バスなどが発着する交通広場を整備するもので、当社単独の開発事業としては過去最大の規模となります(2021年8月竣工予定)。特殊デザインの柱は、この交通広場に設置。大勢の人々が行き交う場所に、従来の型枠によるコンクリート施工法では出せない美しい曲面の柱を採用することで、まちの賑わいづくりの目玉とする狙いです。
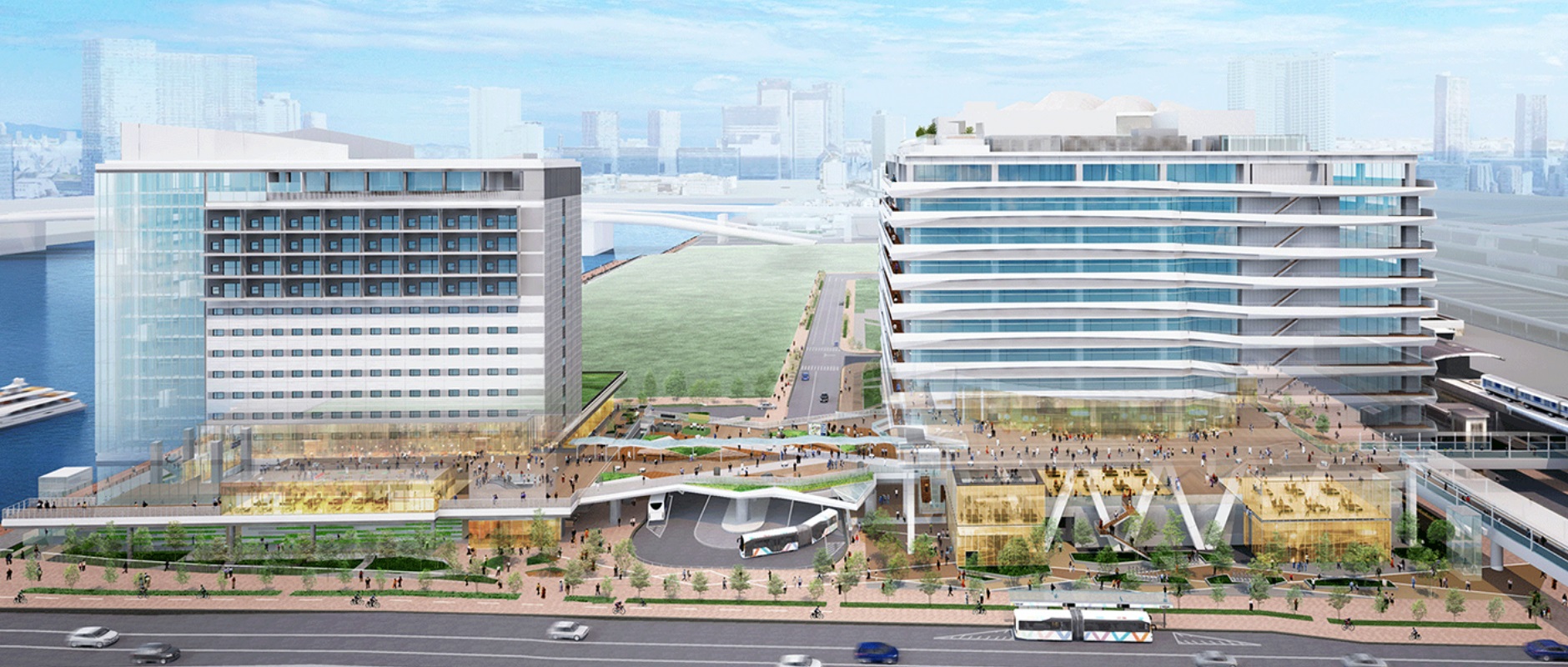
シミズは今後、ラクツムによる埋設型枠の現場適用を推進していくとともに、施工現場で型枠を直接プリントする3Dプリンティングを実現するための研究開発を進めていきます。「柱や壁だけでなく、建築物のファサードや橋梁などの土木構造物にも応用できるはず。将来的には、型枠ではなく構造部材そのものにも使えるようにしていきたい」。今回の現場への実装でラクツムの可能性を実感した小倉は、早くも次の目標へ向かっています。
記載している情報は、2021年5月10日現在のものです。
ご覧になった時点で内容が変更になっている可能性がございますので、あらかじめご了承ください。