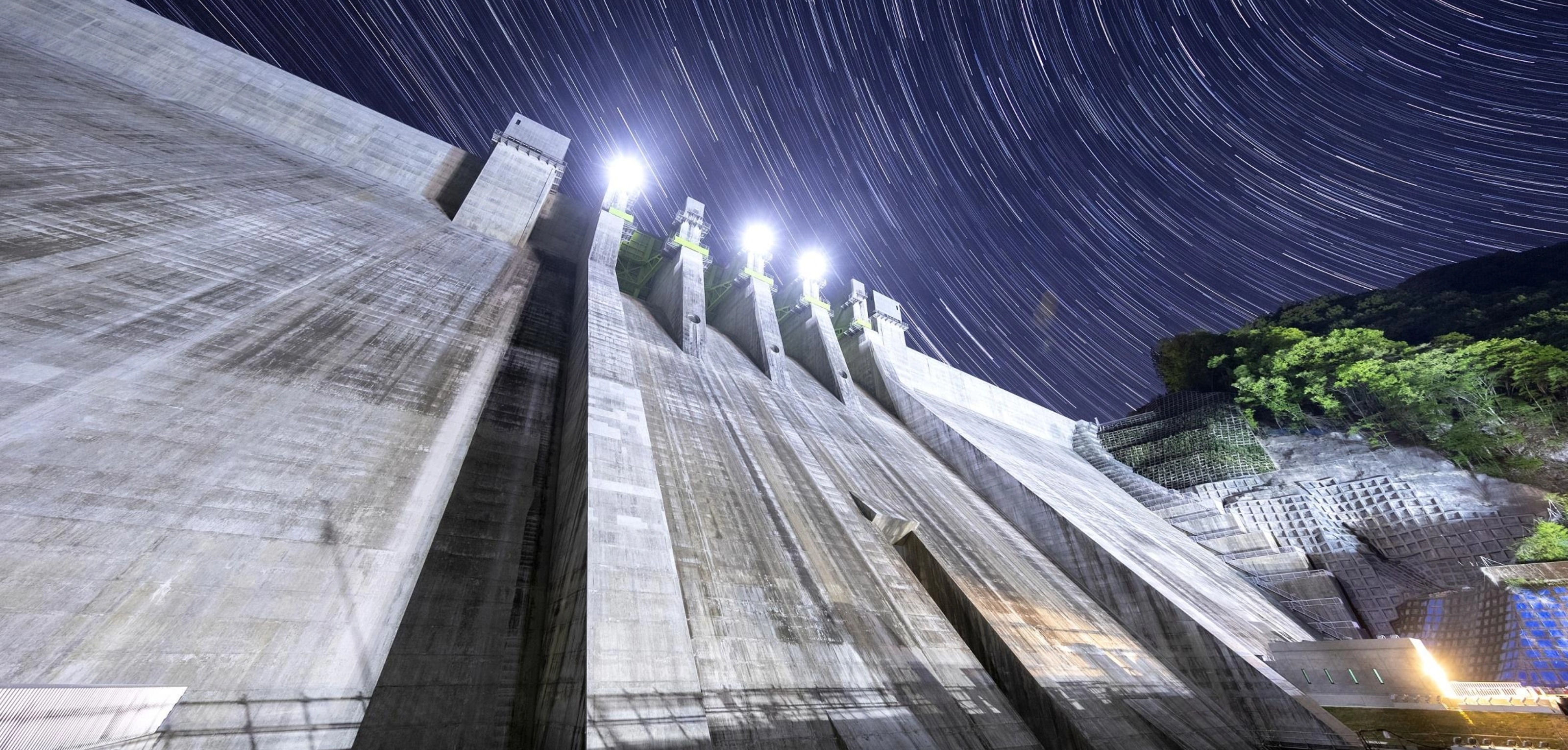
The Frontlines of Dam Construction The Era of Comprehensive Dam Construction(New Construction and Redevelopment)
During the three years from 2020 to 2023, we completed three new dam construction projects, including the Yamba Dam, and two redevelopment projects of existing dams. We currently have two new constructions (Asuwagawa Dam and Toga Dam) and three redevelopments (Ainono Dam, Sengosawa Dam, and Nomura Dam) underway. Actively working on both new dam construction and redevelopment of existing dams, we are a leading player in the dam construction field.
Asuwagawa Dam, Japan’s largest flow-through dam
The Asuwagawa Dam is a new flow-through dam under construction on the Heko River,
a tributary of the Asuwa River in the Kuzuryu River system, a first-class river in Fukui Prefecture. Under normal
conditions, water flows downstream without being stored. Only during heavy rainfall is the gate at the riverbed
closed to store water in the dam reservoir. Subsequently, water is released downstream in controlled quantities,
with the gate regulating the flow rate to mitigate downstream impacts.
It is a large dam with a height of 90
meters and volume of 700,000 cubic meters, so it is being constructed using the cruising RCD construction
method*, which was used in the Yamba Dam project.
For this project, SC premium conveyor which is a
piece of belt concrete transport equipment and two 18-ton cable cranes were installed for high-speed construction.
An automatic dam concrete placement system was also installed to completely automate the entire process from
material supply to manufacturing, transportation, and placing of concrete.
*RCD stands for Roller Compacted Dam Concrete. This is a rationalized construction method for concrete gravity dams. Ultra-hard-mix concrete with less cement is spread by a bulldozer and compacted by a vibratory roller.
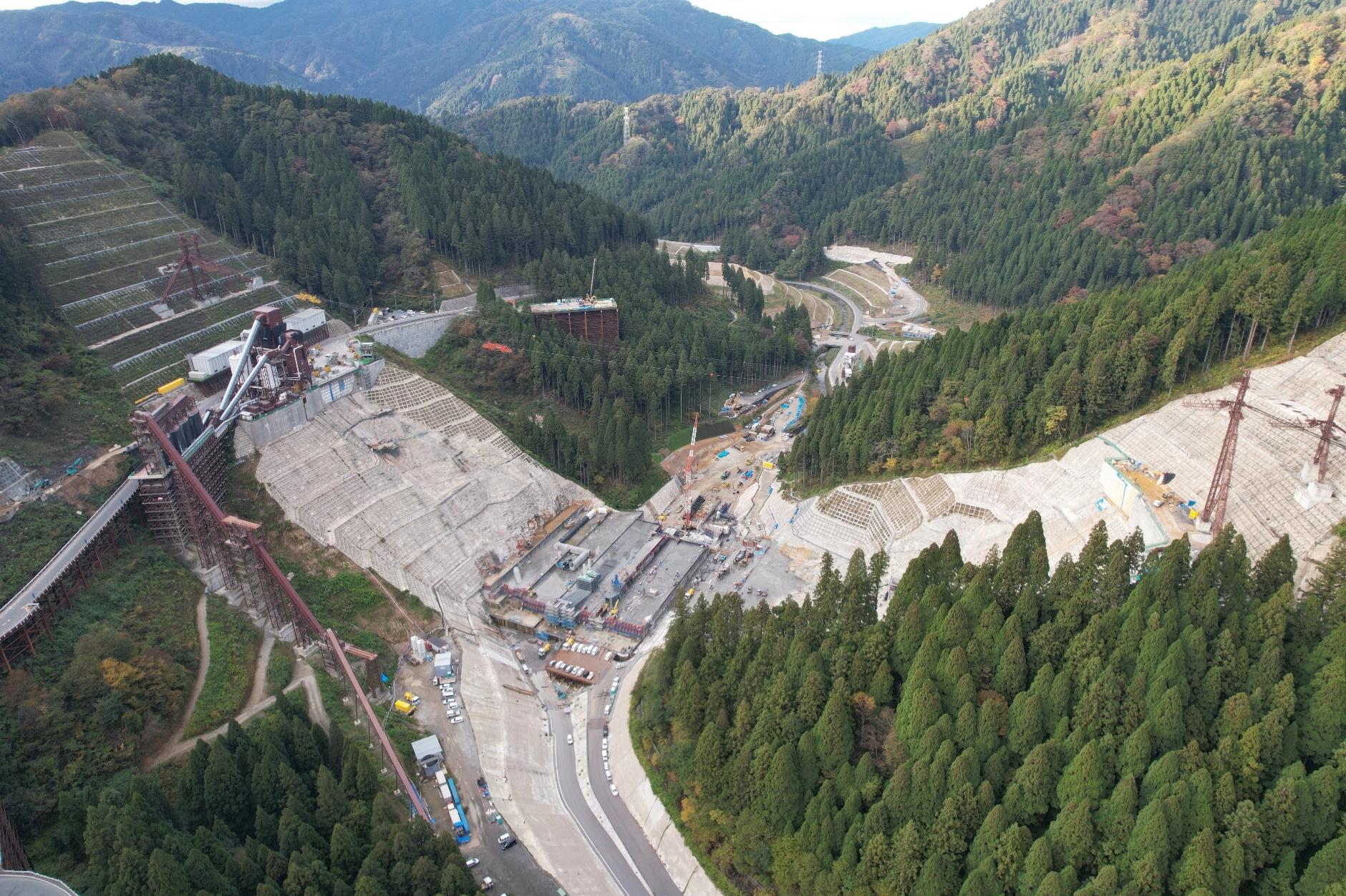
Asuwagawa Dam
- Location
- Obatake, Ikeda-cho, Imadate-gun, Fukui
- Client
- Kinki Regional Development Bureau, Ministry of Land, Infrastructure and Transport
- Construction period
- August 2020 - March 2028
- Structure and scale
-
Concrete gravity dam
96m height, 351m length,
670,000m3 dam volume
Taking on the challenge of diverse redevelopment projects
In Japan, dam construction has traditionally been tailored to suit the
characteristics of their respective drainage basins, aiming to address flood control and water utilization issues.
In recent years, changes in weather conditions have resulted in localized torrential rains (sudden heavy rains),
frequent typhoons, and frequent abnormal droughts, creating a need to strengthen flood control and water
utilization functions.
Moreover, recognizing that well-maintained dam bodies can endure for an extended period,
there has been a growing focus on enhancing the functionality of existing dams rather than constructing new ones.
The aim is to reduce flood and drought damage and improve flood control and water utilization functions.
Our
involvement in dam redevelopment initiatives includes raising the body of the Shin-Nakano Dam, constructing a
tunnel spillway outside the body of the Kanogawa Dam, and modifying the spillway of the Sengosawa Dam. The most
notable project currently underway is the expansion of the spillway within the body of the Nomura Dam.
Introducing the second floating upstream temporary bulkhead in Japan at Nomura Dam
Nomura Dam, located at the uppermost reaches of the Hiji River, a first-class
river in Ehime Prefecture, was completed in 1981 as a multipurpose dam to regulate floods, provide agricultural
water, and maintain the normal flow of water. During the 2018 West Japan floods, there was flooding in the lower
reaches of the Hiji River. For that reason, an improvement plan was established to add one more spillway to the
existing dam to increase its flood control capacity. We were entrusted with the Nomura Dam Facility Improvement
Project, secured through the Early Contractor Involvement (ECI) approach. From the initial construction planning
phase onwards, we provided technical support.
This project involved introducing the second upstream temporary
floating bulkhead in Japan. In redevelopment projects carried out while operating an existing dam, a temporary
bulkhead, created by stacking steel components in what is called a gate leaf, is required to temporarily block the
river water in order to ensure the construction of the foundation structure to be built in the water. In the past,
the pedestal concrete or bracket methods, which require a great deal of diving work, were used for construction.
In this project, however, a floating bulkhead was introduced to improve work efficiency and reduce manpower by
significantly reducing diving work.
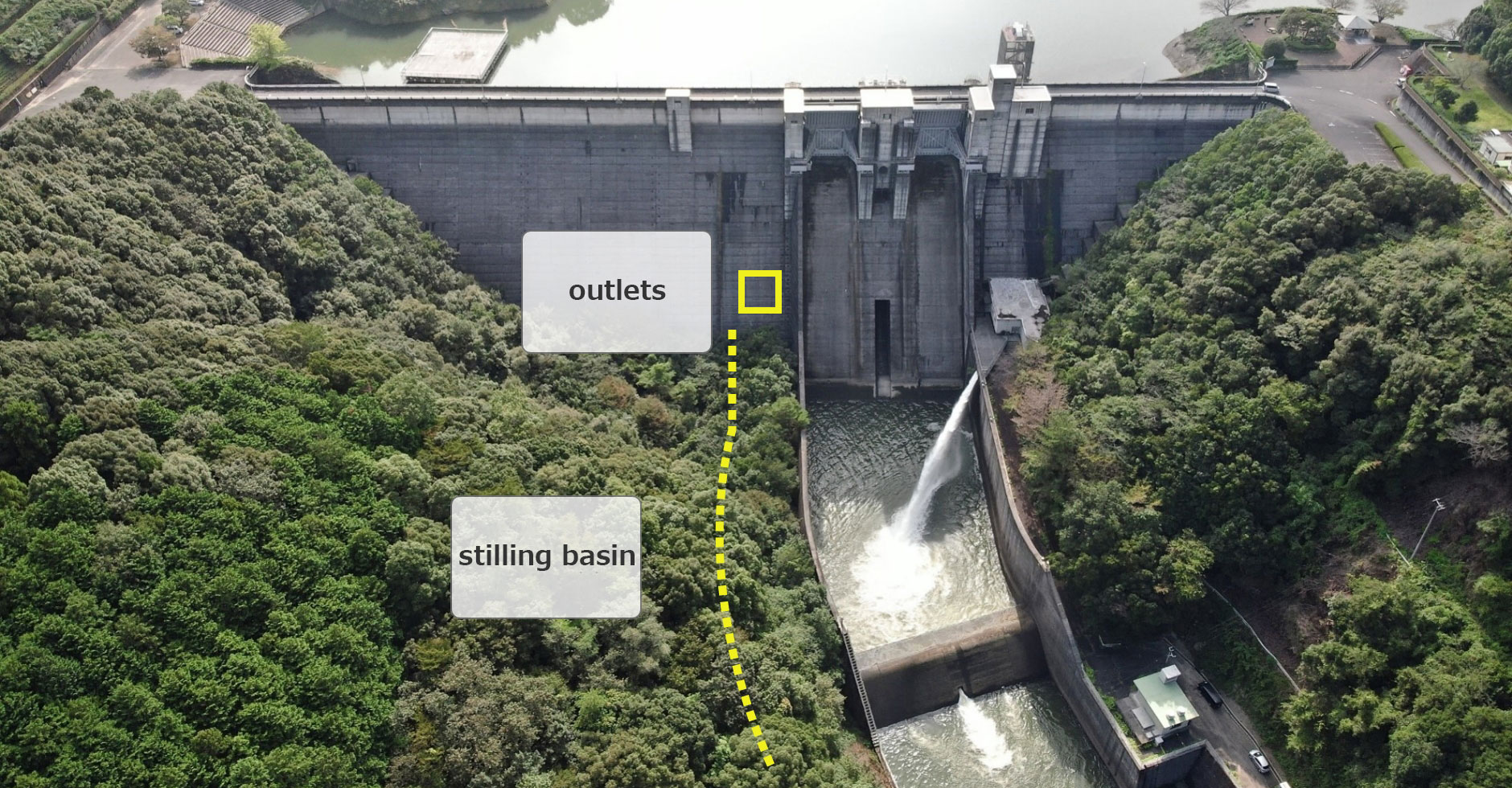
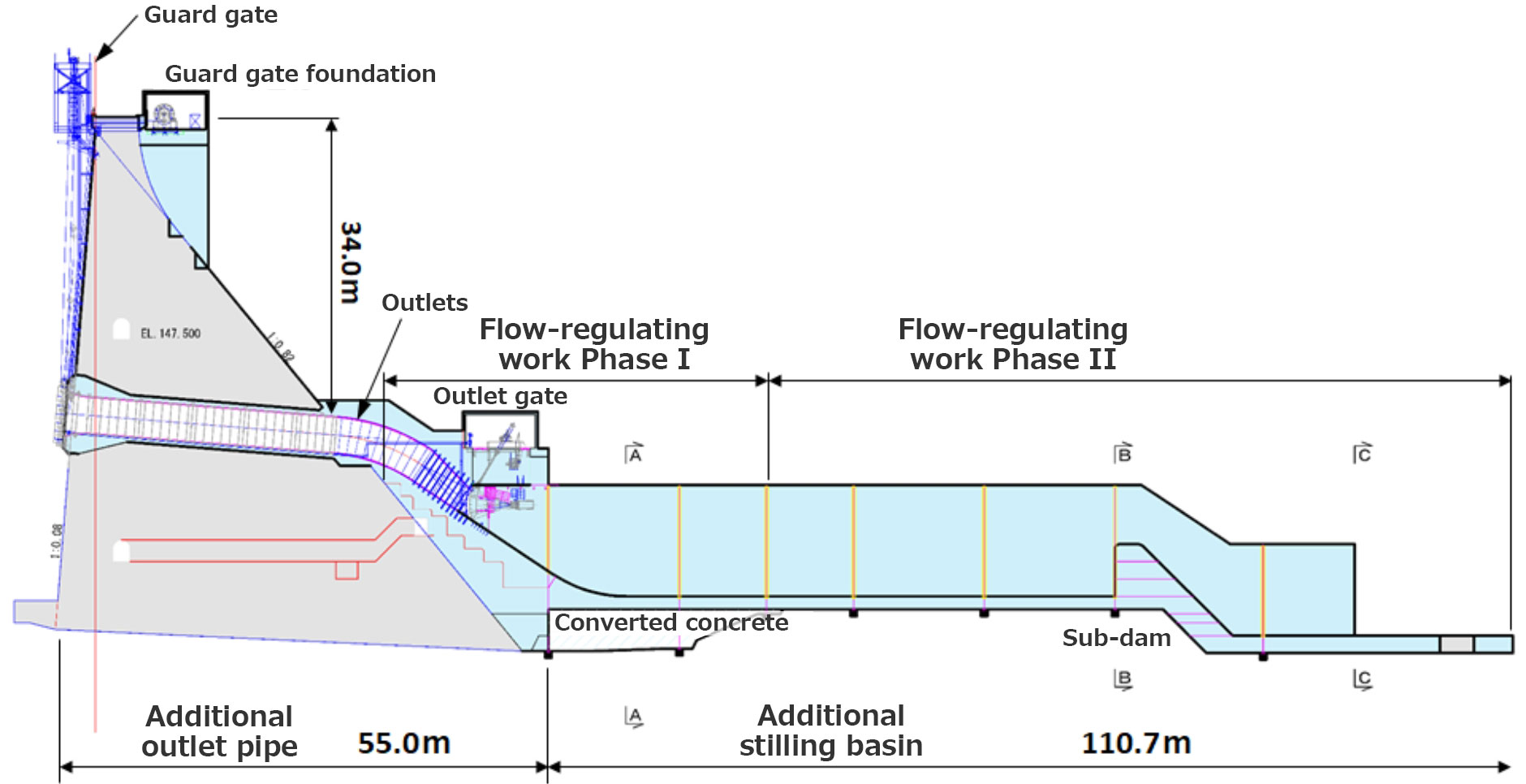
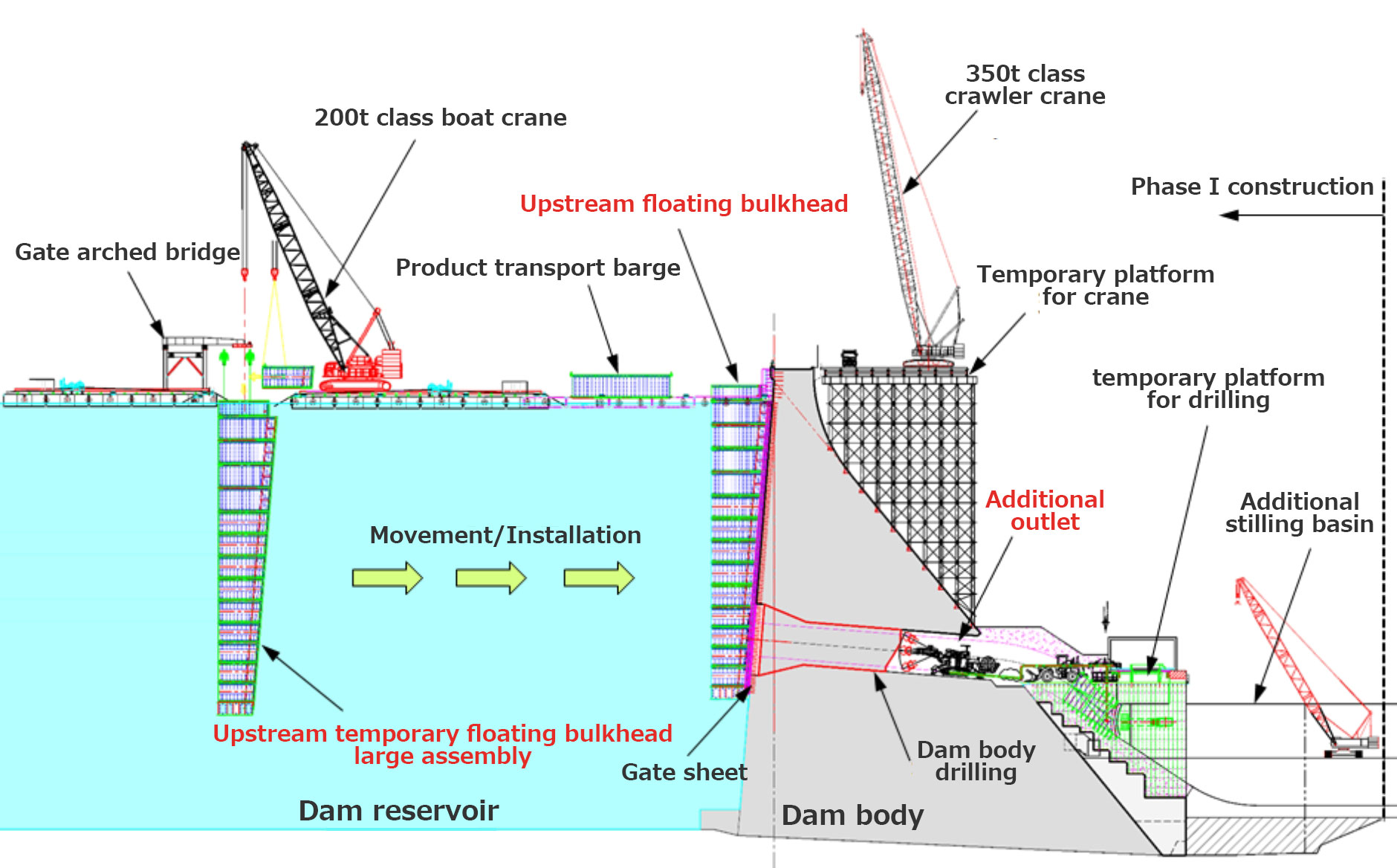
Nomura Dam
- Location
- Nomura, Nomura-cho, Seiyo City, Ehime
- Client
- Shikoku Regional Development Bureau, Ministry of Land, Infrastructure and Transport
- Construction period
- May 2023 - December 2025(Phase I)
- Structure and scale
-
Concrete gravity dam, additional outlet and decelerating work
60m height, 300m length,
254,000m3 dam volume
Labyrinth-type spillway at the inflow section of Sengosawa Dam
The Sengosawa Dam, situated on the Kitasu River within the Abukuma River system,
a first-class river in Fukushima Prefecture, was completed in 1975 to supply irrigation water. However, recent
shifts in agricultural dynamics have led to declining water usage for farming purposes, resulting in surplus water
storage capacity within the dam. The reconstruction work was planned to utilize this available capacity for flood
control to reduce flood damage. We reconstructed the inflow spillway (labyrinth structure), constructed a new
gravity dam, installed a new water level lowering facility, and upgraded the administration building and
administrative facilities.
The Sengosawa Dam redevelopment project required construction of the spillway from
November to February to avoid the busy farming season, as it was essential to maintain the dam’s functionality
during construction. Concrete work during winter months, when temperatures drop, necessitated covering placing
areas with sheets and using jet heaters or other heat-supplying equipment for curing. After placing the concrete,
we provided thermal insulation to ensure the quality of the concrete despite the harsh winter conditions.
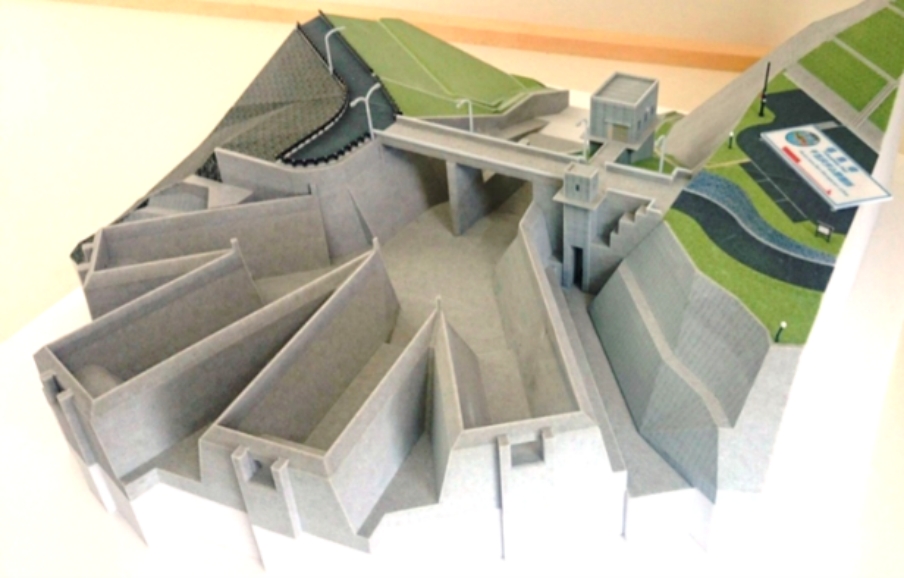
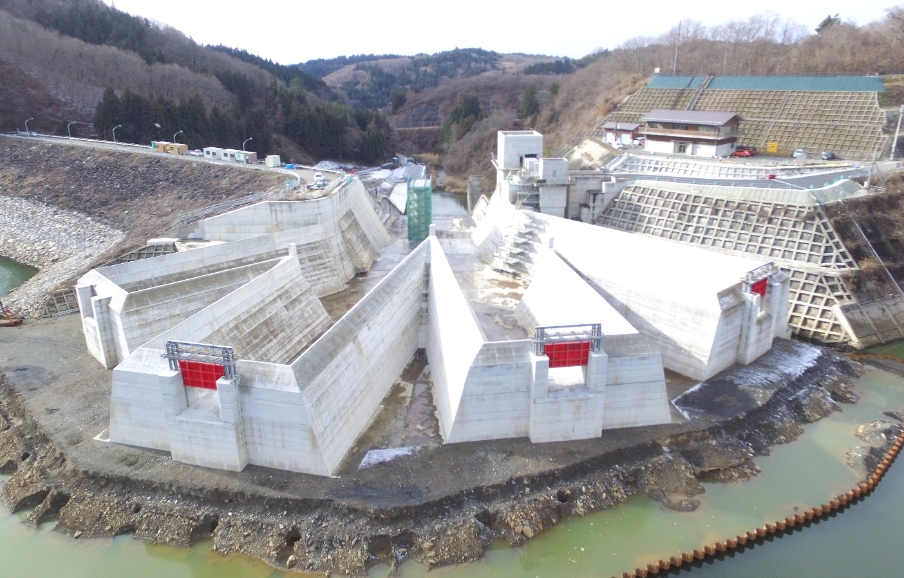

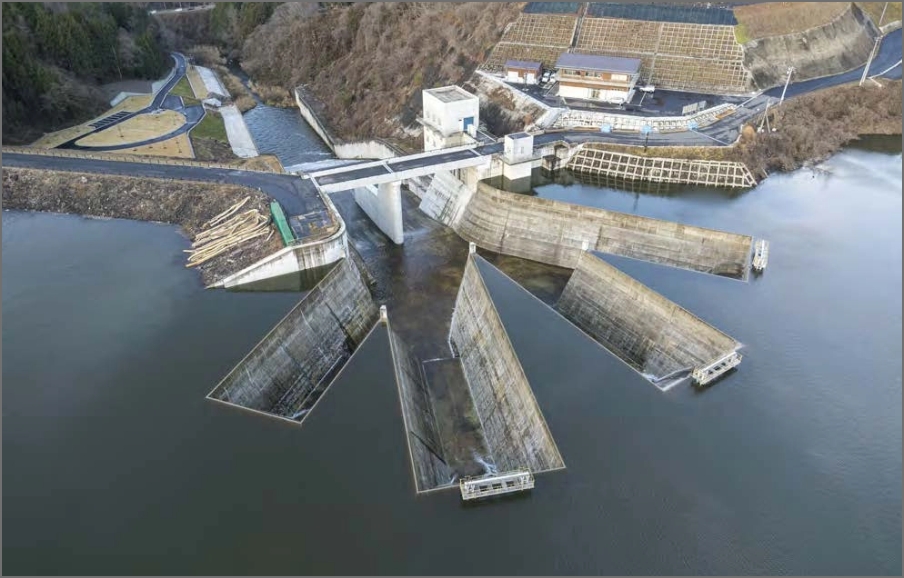
Sengosawa Dam
- Location
- Yugoto, Ishikawa-machi, Ishikawa-gun, Fukushima
- Client
- Fukushima Prefecture
- Construction period
- October 2014 - March 2024
- Structure and scale
-
Earth-fill dam
Labyrinth-type spillway reconstruction,
new gravity dam construction,
new water level lowering facility construction,
and administration building and administrative facility upgrades43.0m height, 176.5m length,
347,000m3 dam volume
Streamlining dam construction and saving manpower
The construction industry faces challenges such as a shortage of human resources, skill transfer, work at dangerous job sites, and normalized long working hours. Introducing the latest DX technology and tools is expected to help solve these challenges. In dam construction, in particular, it is difficult to gather human resources due to the danger inherent in construction in mountainous areas. There are also concerns about long working hours due to the two-shift construction system. For that reason, this is considered an area where DX can be highly effective in streamlining construction and saving manpower.
SC premium belt conveyor for conveying concrete
Concrete placing accounts for more than half of the total construction work in
concrete dam construction. As such, improving the efficiency of concrete placing is key to improving overall
construction productivity. Shimizu has set its sights on the importance of improving the transport capacity of
concrete in particular to increase placing efficiency. We have developed SC premium belt conveyor, a piece of
concrete conveying equipment that uses a bag-shaped belt conveyor that can be placed in a straight line even on
steep slopes to maximize conveying efficiency. We installed a demonstration test machine in Iwaki City, Fukushima
Prefecture to move toward actual operation.
We will introduce the equipment at the Asuwagawa Dam in the fall of
2024 to improve the productivity of concrete work there.
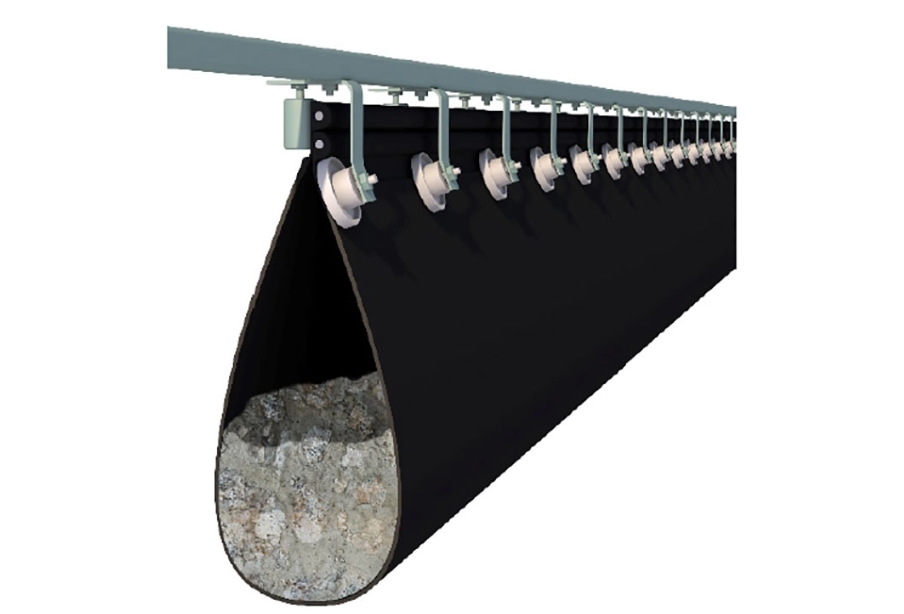
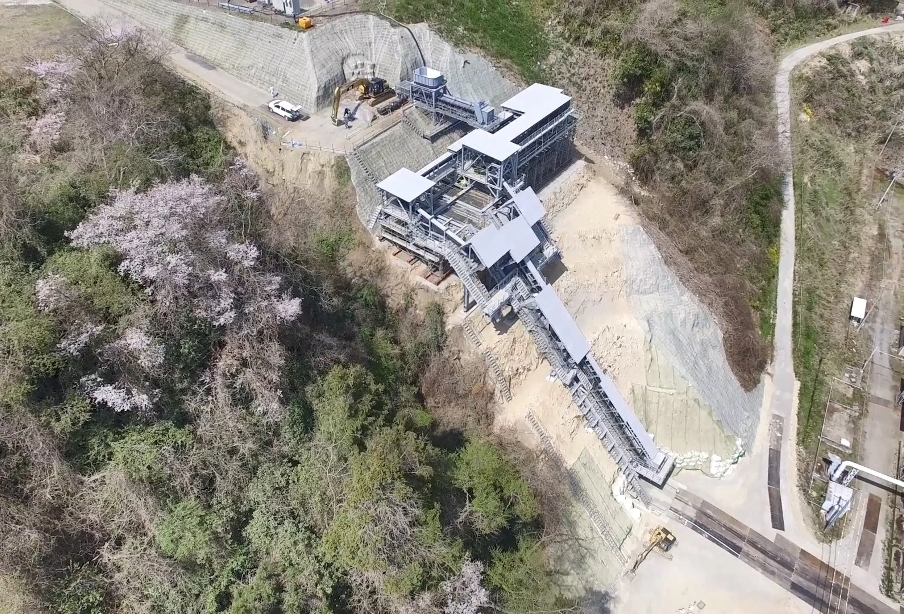
Automatic dam concrete placement system
Dam concrete is mixed at on-site concrete plant, then transported and placed
using cable cranes and other equipment. This series of work is repeated tens of thousands of times, so improving
the efficiency of this work will significantly contribute to improving the productivity of dam construction. As
such, we developed an automatic dam concrete placement system that automates all processes from supplying concrete
materials (aggregate, cement, and water) to making, transporting, and placing the concrete.
This system enables
a series of tasks to be performed entirely automatically by creating a placing plan and entering it into the
system. It has allowed us to reduce the number of personnel involved in concrete placing to two-thirds,
contributing to higher productivity and manpower savings. In addition, since the system can be operated without
skilled operators, the technology also addresses the expected turnover of skilled technicians. We implemented the
system at the Yanagawa Dam in Iwate in 2019. Since then, we have added improvements, and it is currently in use at
the Asuwagawa Dam.
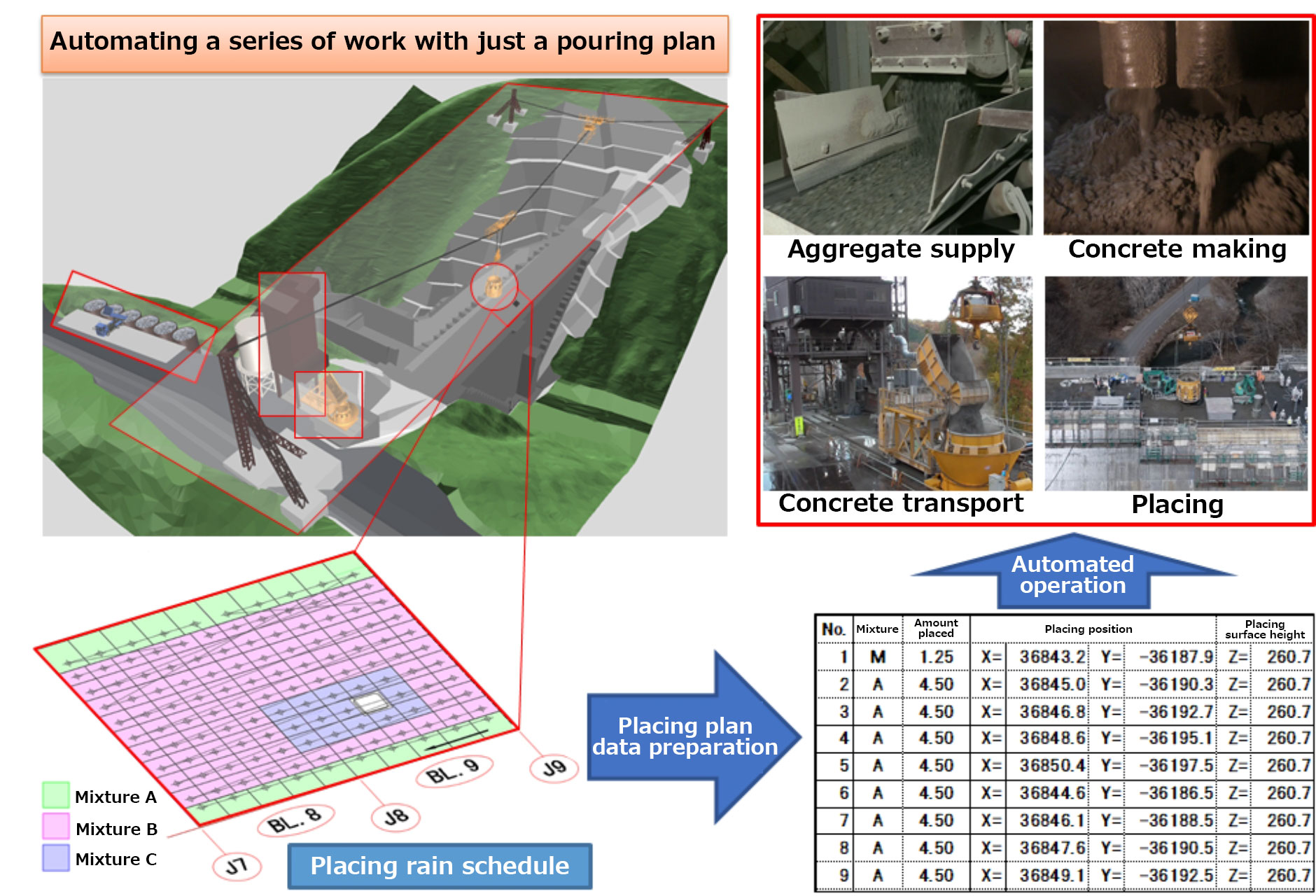
SC premium vibrating backhoe, a backhoe with vibrator, equipped with our Dam Concrete Compaction Management System
To build a concrete dam, a backhoe with vibrator compacts the concrete during placing to homogenize the aggregate and cement. When compaction is finished is determined based on the experience of on-site technicians. However, to ensure appropriate and stable quality, we have developed a compaction management system that quantitatively determines the completion of work based on objective data measured by ICT. The index of compaction is the flatness (unevenness) of the surface measured by a 3D scanner. The compaction position is determined in 3D coordinates using GNSS and various sensors. We have begun utilizing SC premium vibrating backhoe, a backhoe with vibrator, equipped with this system.
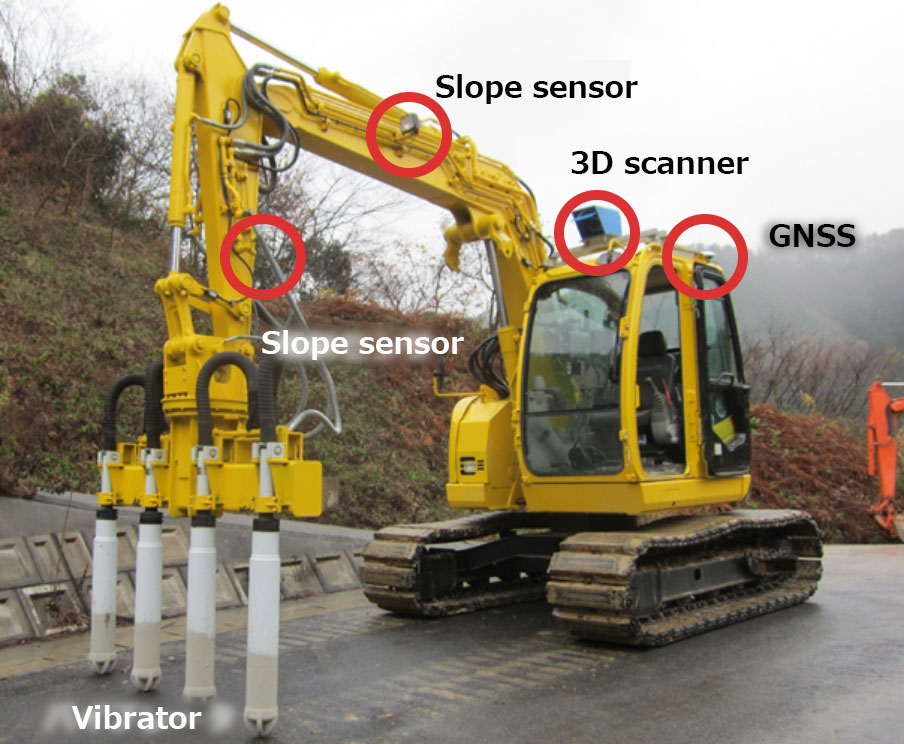
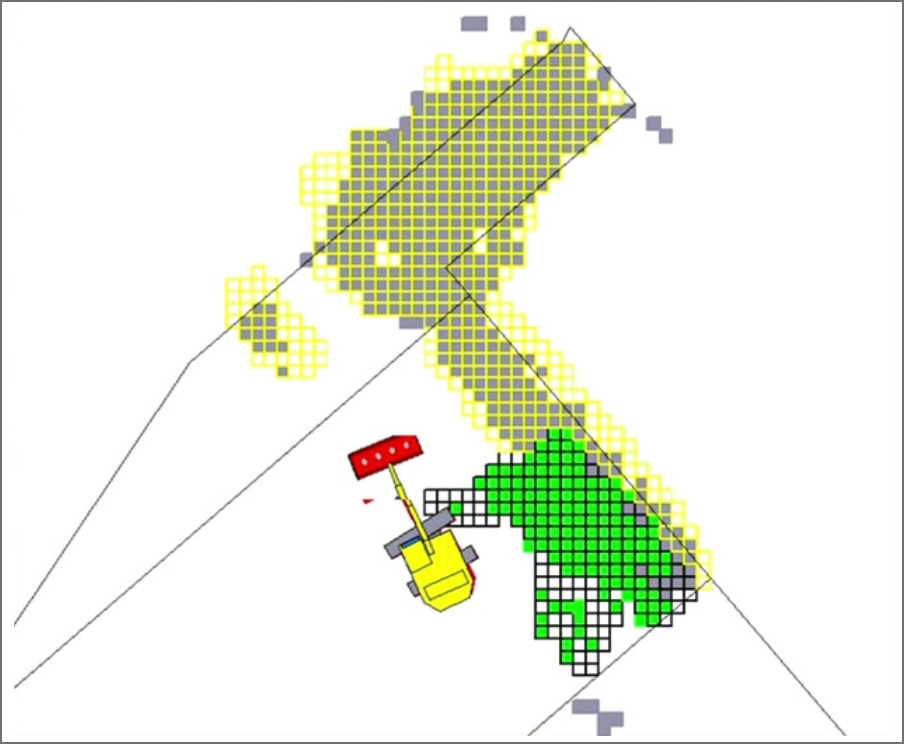
Particle size distribution detection system
Aggregate for dam concrete production is obtained by crushing and cutting rocks extracted from the on-site quarry and then classifying the materials by particle size through a process called a sieve test. Traditionally, sieve tests have been performed manually, and dam concrete placing takes a long time (two to four years), requiring a significant amount of manpower and time. To address this, we installed a laser scanner on a belt conveyor and developed a system to capture point cloud data of the transported aggregate and detect the particle size distribution via AI data analysis. This has helped improve productivity and save manpower.
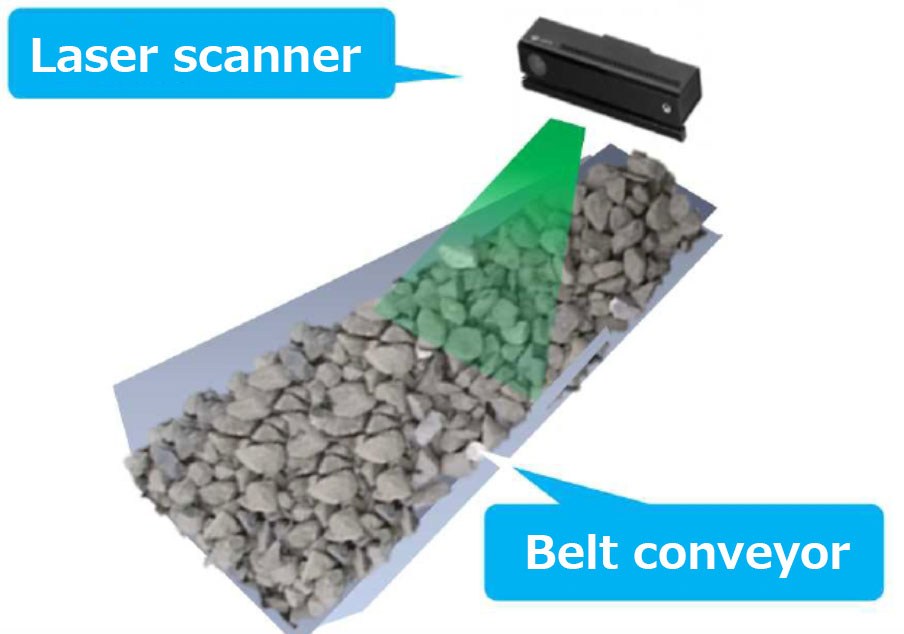
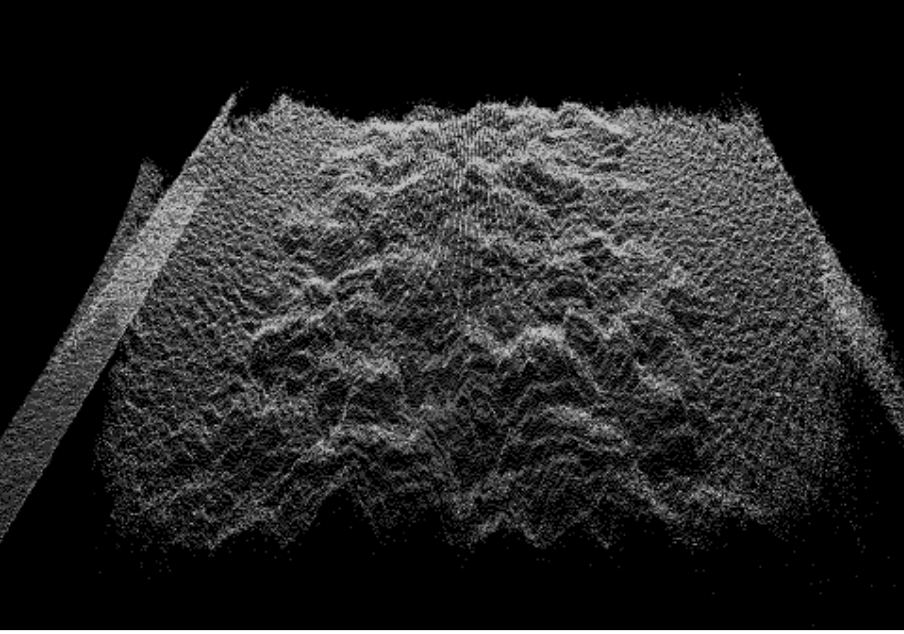
Outlook for dam construction
A cap on overtime will be applied effective April 1, 2024. That means we must improve productivity, save labor, and reduce working hours. We will continue to develop technologies to help improve productivity and save manpower in dam construction work and work toward their practical application and widespread use. This is an era in which dam construction work is diversifying into new construction and redevelopment. We will tackle both and contribute to the development of social infrastructure.
The information posted here is the current information on March 15, 2024.
Please be aware that
this information may have changed by the time you view it.