July 12, 2017
Shimizu Corporation (President: Kazuyuki Inoue) has developed Shimizu Smart Site, a next-generation production system for performing construction work through human collaboration with autonomous robots that are equipped with the latest technology. This was achieved through the use of information-oriented construction, with BIM (Building Information Modeling) as the core of the system. This system was developed to improve productivity, reduce hard and repetitive work, and increase the efficiency of inspections and management tasks at construction sites. The construction sites where the individual robots and construction machinery that are part of Shimizu Smart Site will be used have already been decided. Shimizu will begin construction on a high-rise building that will use the complete system in the Kansai area early next year. The goal is to achieve a 70% or greater reduction in labor in construction tasks performed by the robots through completion.
Hiring new workers and improving productivity is an urgent issue due to concerns over the large number of skilled workers retiring. Because improving productivity is key to improving wages, expanding the number of days off, and other improvements in work conditions, the Ministry of Land, Infrastructure, Transport, and Tourism designated 2016 as the initial year of a revolution in productivity, beginning the introduction of i-Construction based on the premise of automating construction through the use of information science. Shimizu recognized this trend and the needs to be a leader in the construction industry on the information-oriented construction, developed Shimizu Smart Site system, and worked to develop and manufacture the autonomous robots that make up the system.
The autonomous robots and construction machinery that make up the Shimizu Smart Site system include: the Exter, a horizontal telescopic crane that has an expandable and retractable boom to adjust to the working radius; Robo-Welder, a column-welding robot that operates a welding torch; Robo-Buddy, a multipurpose robot that handles construction work for ceilings and floors with its two arms; and four main types of horizontal and vertical conveyor robots with Robo-Carrier as the main robot. Each type of robot employs AI or IoT to move around the job site while maintaining an awareness of its own positioning, recognize the work to be performed and perform it independently based on task instructions sent from the integrated control system operated via a tablet device. The operational status and task results of each robot are logged and collected in the integrated control system in real time, and can be confirmed via the tablet screen at any time.
After the construction work on the foundation is completed at a site employing Shimizu Smart Site, an all-weather cover is installed to provide a lightweight shelter for the building against all kinds of weather. Exter, which is located beneath the cover, then lowers the columns and beams of the steel frame into position sequentially and Robo-Welder welds the columns to complete the framework. Robo-Buddy executes the final stage of finishing the floors and ceilings from the lower floors upward. After Robo-Carrier and other horizontal and vertical conveyor robots transport the materials that have been delivered to the job site to their temporary staging areas at night, they then transport them to the location where Robo-Buddy will perform the work.
When Shimizu Smart Site is used to build a 30 story building with a standard floor area of 3,000 m2, the following labor savings (reduction) are estimated at a 75% reduction in lifting and transport work, 2,500 workers; a 75% reduction in interior finish work, 2,100 workers; and a 70% reduction in column welding, 1,150 workers, for a total labor reduction of nearly 6,000 workers. The labor-savings enable full depreciation of the individual robots and construction machinery to be paid for after use at two to three job sites.
Shimizu will strive to improve productivity in the future by using the entire Shimizu Smart Site system and by using individual elements of the system, with the goal of preparing for future labor shortages and creating more attractive job sites.
<<For Reference>>
1. Conceptual Diagram of the Shimizu Smart Site System
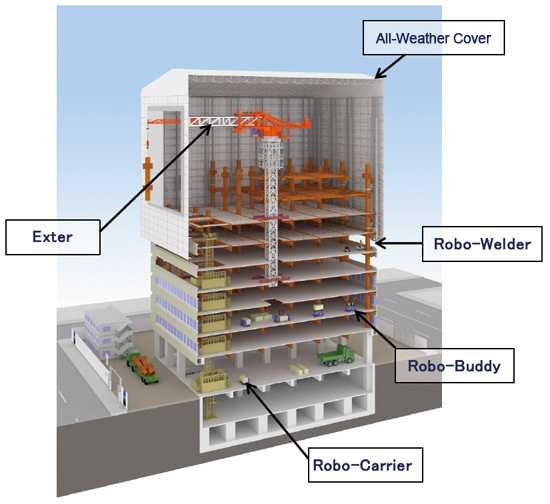
2. Components of the Shimizu Smart Site System
Exter
Unlike existing tower cranes that have a knuckle-type bendable boom, the Exter incorporates a function that enables the boom to extend and retract horizontally. The crane has a load capacity of 12 tons, an operational radius that extends from a minimum of 3 meters to a maximum of 25 meters, and it can be used even in ultra-high-rise buildings of the 200-meter class. Moreover, because Exter can be used in combination with an all-weather cover for demolition work, we anticipate its use in a rapidly growing number of projects. IHI Transport Machinery Co., Ltd., the subcontractor manufacturing the crane, will complete two cranes at the end of June. These will be first used at a high-rise office building site in Kansai.
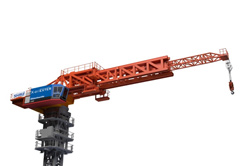
Robo-Welder
Shimizu worked on joint development with Professor Satoru Asai, who runs a lab in the Division of Materials and Manufacturing Science, Graduate School of Engineering Osaka University. Once the robot has been placed on a special conveyor and is guided to the designated position, it automatically performs all welding without worker intervention. The robot recognizes the channel shape (groove) of the spot to be welded by laser measurement. A robotic arm equipped with a welding torch moves freely along six axes and determines the conditions in real-time for accurately welding the groove with welding material. The welding work uses two robots. We also plan to introduce a non-contact system that can inspect the quality of welded components in real time. The manufacturing of this has been subcontracted to Aichi Sangyo Co., Ltd. and the decision to use it has already been made at three job sites.
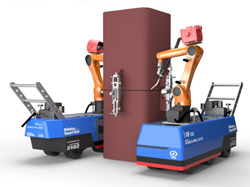
Robo-Buddy
Robo-Buddy recognizes its own position via laser sensors and referencing BIM information (SLAM function), and automatically moves to the specified work location. It is also equipped with a special feature that enables it to climb over level differences of 20 cm. The two robot arms that perform the work move freely along six axes and can pick up materials weighing up to 30 kg. It operates on an elevating pedestal on top of an automatic guided vehicle. After it recognizes the location to perform the work via imaging sensors and laser sensors, it uses its two robotic arms to insert ceiling suspension bolts, assemble the base materials, and install the ceiling board, screw it into place, and install the OA floor pedestal and paneling. This robot can be used to perform multiple functions by switching the end effectors at the tip of the robotic arms. The manufacturing subcontractor is Toyo Iron Co., Ltd., and aT Robotics Inc. is collaborating on development. It will be first used at a high-rise building site in the Kansai area.
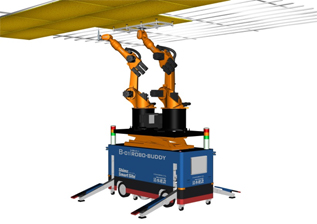
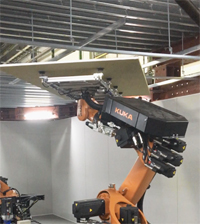
Robo-Carrier, the Core Component of the Automatic Conveyor System
Robo-Carrier is the automatic conveyor system that transports the materials delivered to the job site to the location where Robo-Buddy will perform its work. This system consists of four types of robot, with Robo-Carrier as the core of the system for horizontal transport. It operates by receiving instructions from the integrated control system. It will begin operating at a job site in Tokyo from November. Robo-Carrier recognizes its own position via laser sensors and referencing BIM information, and automatically transports materials to the designated work site. When it encounters an obstacle, it performs a repeat search and corrects course.
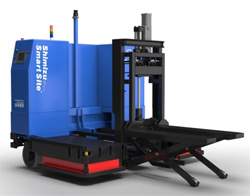
The Robo-Carrier is deployed on ground level and loads palletized materials on an Autonomous ELV that works in concert with it. When the ELV arrives at the delivery destination, another Robo-Carrier unloads each pallet from the ELV and transports it to the temporary staging area. The Robo-Fork loads the materials in the temporary staging area onto the Robo-Assist which works alongside the Robo-Buddy and carries them to the Robo-Buddy base.
All-Weather Cover
The all-weather cover consists of outer material made of temporary scaffolding and roofing materials composed of lightweight steel trusses. The roof is covered with a waterproof sheet and the external area is covered with a mesh sheet that has superior transparency. The simple structure and light weight does not require reinforcement of the building framework. The first site it will be used at is a high-rise building in the Kansai area.
The information contained in this news release is the current information on the date of publication. Please be aware that this information may have changed by the time you view it. Please contact the company to inquire for further details.