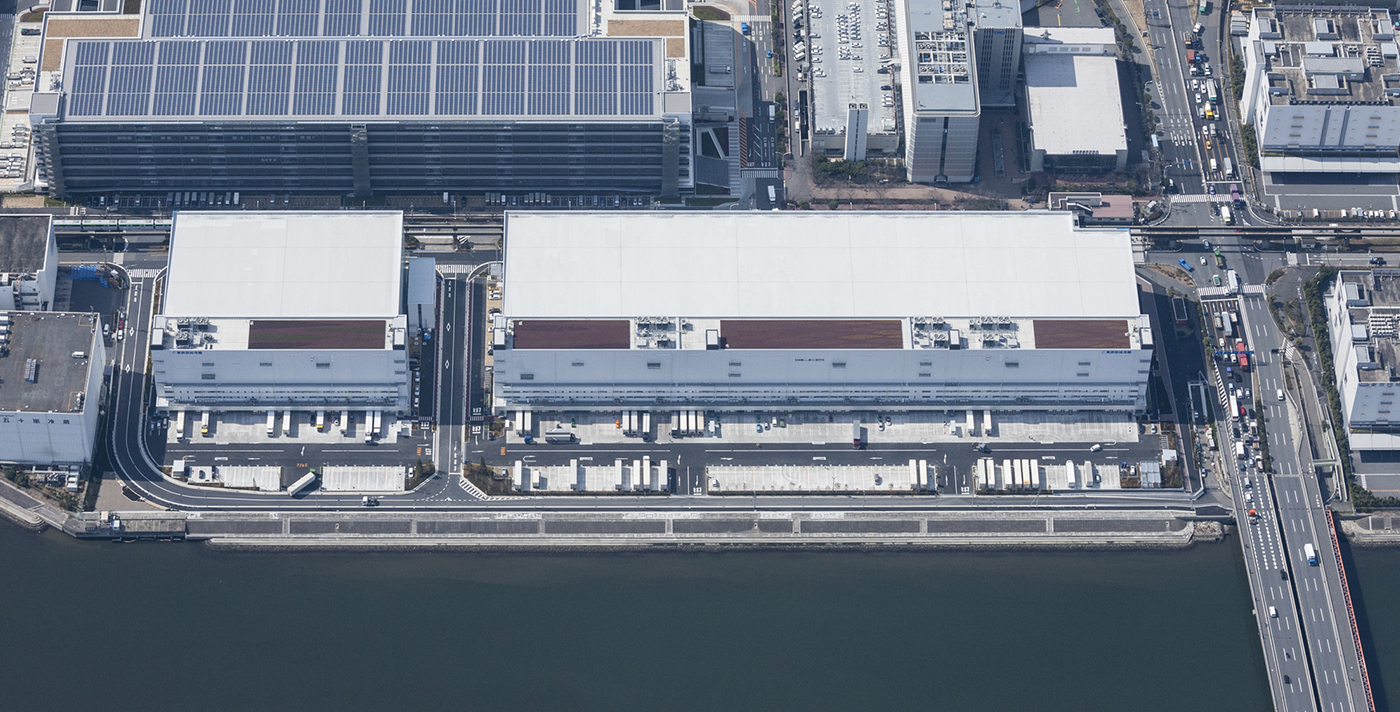
Production and Logistics Facilities of TodayShimizu Taking on the Challenge of Building the Largest Seismically Isolated Refrigerated Warehouse in JapanThe North, South and Administration Buildings of Tokyo Danchi Reizo Co.
Heiwajima in Ota-ku has superior access from the Oi Wharf and other main port facilities. Construction of Japan’s largest seismically isolated refrigerated warehouse was completed here in February 2018. The two North and South buildings have a combined total floor space of around 135,000 m2 and storage capacity of 178,000 tons. It is the first time Shimizu has taken on the challenge of building a seismically isolated refrigerated warehouse of this magnitude.
Shimizu used its expertise in construction of massive warehouses and the engineering technology it has developed thus far to achieve this.
Building a Large Refrigerated Warehouse as Quickly as Possible
Tokyo Danchi Reizo Co. ordered the construction. The company’s refrigerated warehouse, which it operated in Heiwajima since around 1965, houses around 300,000 tons a year of products imported from overseas, consisting mainly of meat and other products, and roughly 30% of meat unloaded at Tokyo Port. It is not an exaggeration to say that it helps to feed the Greater Tokyo Area. The warehouse has deteriorated with the passage of many years, however. The company wanted to consolidate the multiple existing refrigerated warehouses to improve the efficiency of logistics, including the construction of a new peripheral road and also construct a seismically isolated building from the perspective of business continuity planning (BCP) to ensure a stable supply of food to the Greater Tokyo Area even in the event of a disaster.
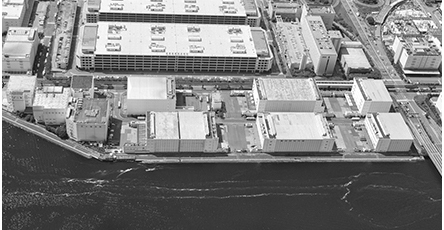
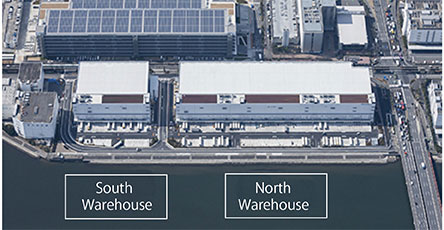
Nine warehouses consolidated into two, the North and South Warehouses
Because another temporary storage location had to be prepared for tenant companies while the warehouses were being rebuilt, this meant that the longer the construction period, the higher the cost incurred.
The company therefore requested that Japan’s largest seismically isolated refrigerated warehouse be built as quickly as possible.
We met that need with the Shimizu New RCSS construction method, named for our company.
Taking on the Challenge of Using a Proprietary Construction Method and Counterintuitive Thinking
The Shimizu New RCSS construction method combines high-strength reinforced concrete columns that use high-strength concrete and are resistant to contraction with Shimizu’s own joining technology for connecting the columns to steel beams to make long spans possible. This technology achieves both high strength and high earthquake resistance, and the use of fewer columns makes a higher storage capacity possible. Industrializing many aspects of construction such as precasting the reinforced concrete columns and the foundation for the seismic isolation system also made it possible to shorten the construction period and meet the needs of the customer.
Construction Plan PointsComparing Construction Methods for the Upper Structure
Shimizu RCSS Construction Method
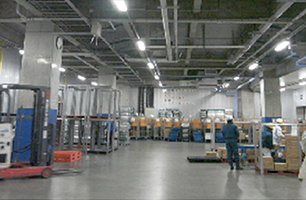
A construction method that uses columns made of reinforced concrete and beams for the steel frame. A dry-panel construction method is used to build exterior walls and room partitions
Used in this project
- Makes large spans possible
- Industrialization shortens the construction period
- Steel beams used to make steel frame lighter
- Enables application of Construction EXP.J
Precast Concrete Pca Method

A construction method that uses columns and beams made of precast concrete, that are connected by cables
Used in recent refrigerated warehouse construction
- Makes large spans possible
- Industrialization shortens the construction period
- Frame is heavy
- Application of Construction EXP.J difficult
Flat Slab Construction Method
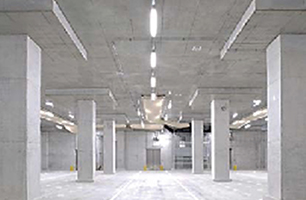
A construction method that uses prestressed concrete and steel materials driven into the slab. These are stretched to control the stress, eliminating the need for beams
Conventional refrigerated warehouse construction method
- Makes large spans difficult
- Difficult to industrialize
- Frame is heavy
- Application of Construction EXP.J difficult
Reducing the number of columns enables storage of more pallets. The columns were precast (factory built) to shorten the construction period.
The challenge was contraction of the framework (concrete, steel frame) that occurs due to cooling the interior of the refrigerated warehouse. Because concrete and steel have the property of expanding and contracting according to the temperature, the entire structure of the North Warehouse, which is the largest in Japan, contracts about 12 cm when cooled from room temperature to −25ºC.
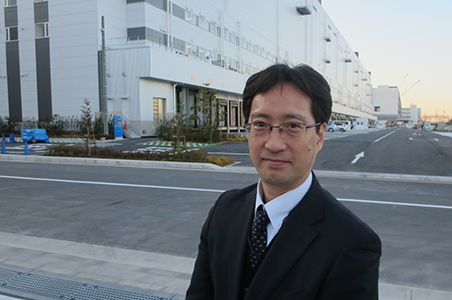
Eiji Matsumoto, who was in charge of the project in the Design Division, had this to say about the problem: “We tackled the challenge by reversing the concept and asking, ‘If the frame will shrink when cooled, would it work to cool the frame while it is in sections and connect the sections after it has shrunk sufficiently?’”
To resolve this problem, we divided construction of the top 253 m of the frame into three separate blocks. After this was completed, we put the connecting components of the separate blocks in a slidable state, cooled the frame, and distributed the frame contraction across each of the blocks. After the frame had shrunk sufficiently, we bound each block to create a single structure. This enabled us to complete the building without any warping due to contraction. We utilized the steel beam feature of the Shimizu New RCSS construction method and incorporated a sliding mechanism in the connecting components.
Shimizu subsequently obtained a patent for this refrigerated warehouse construction method (Nickname: Construction EXP.J).
Devising a Construction Method that Solved the Problem of Warping due to Cooling
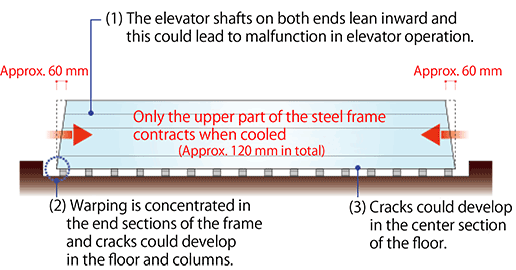
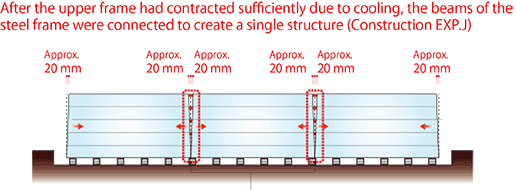
We divided the building into three blocks and employed a method of joining them after cooling to solve the problem of thermal contraction of the steel frame, which has presented the biggest challenge
*Already patented: Patent No. 6414673 for the Refrigerated Warehouse Construction Method
BIM Engineering and Technical Capabilities that Support Ideas
It is simulations and space management using BIM* and functional experiments by the Shimizu Institute of Technology that support the realization of such bold, original ideas.
We carefully verified each location through a process of repeated trial and error in temperature simulation using a BIM model to predict frame malfunction due to thermal contraction and cooling and to control the condensation and mold that occurs depending on the outside temperature difference. We also used BIM to check and make sure that there was no mutual pipe and cable interference between the mutual building construction work, and refrigerated equipment and electrical equipment installation work. This substantially reduced reworking during construction.
We also performed functional experiments to test the steel beams in a low temperature of −25ºC, the actual environment they would be used in.
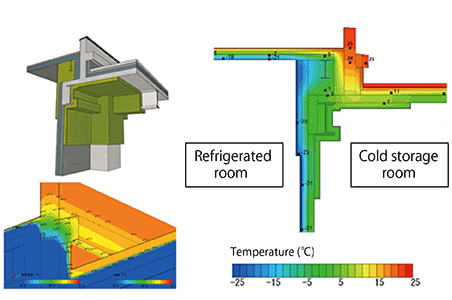
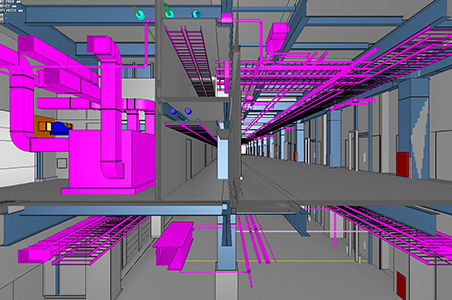
*BIM: An abbreviation of Building Information Modeling. Data on attributes such as cost, finishing, and management can be added to a 3D digital model of a building produced on the computer. This enables use of shared information on all stages, from design and construction to maintenance and management.
Shimizu’s ideas and engineering, and on site members who performed excellent to implement them. The incorporation of all of these enabled us to build Japan’s largest seismically isolated refrigerated warehouse in a short amount of time, taking just one year for demolition work and one year and eleven months for new construction.
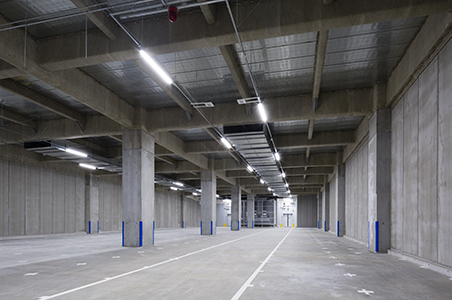
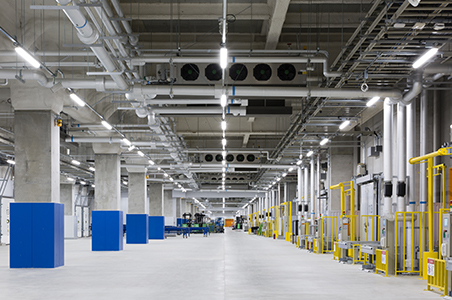
In Line with the Pace of Change
Many of the refrigerated warehouses in Japan are reaching the age of obsolescence and rebuilding them is a matter of urgency. Furthermore, there is no doubt that the need for warehouses will grow even more in today’s environment where Internet shopping is the normal practice.
Aligning ourselves with the changing times and being able to build the optimal structures with the optimal construction methods is Shimizu’s strength. The logistics industry is confronting great changes. Shimizu will continue to take on the challenge of providing a tailwind for the industry as it evolves.

The information posted here is the current information on December 25, 2018.
Please be aware that this information may have changed by the time you view it.