Automatic generation of the shape of a complex traditional joint in which the apex moves along a sine curve.
Automatically creating 3D models using Grasshopper without producing conventional 2D drawings reduced the number of man-hours required and expanded the range of ideas.
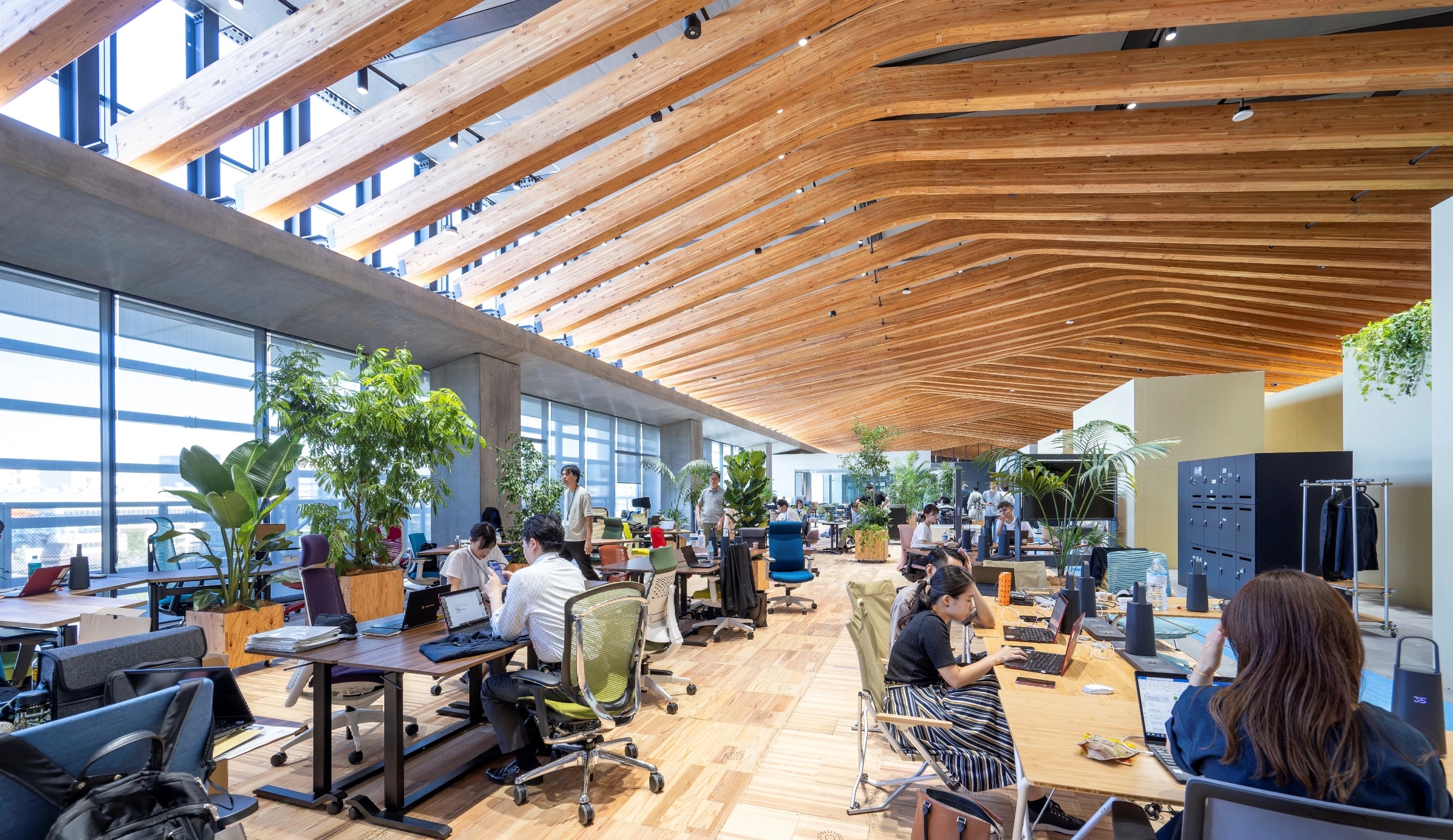
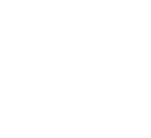
Smart Innovation Ecosystem Novare
(“New” Japanese Scarf Joint)
Novare: A new platform that creates next-generation innovation
Novare is an open innovation hub nestled in Shiomi, Koto-ku, Tokyo. Its name, derived from the Latin word for “to create” or “to renew,” embodies its purpose—to create a place for new invention by bringing together knowledge from Japan and overseas. Comprised by five facilities which work both independently and collaboratively, Novare mirrors the intricate ecosystems of nature, all converging at the heart of monozukuri (superb craftsmanship).
- Project site
- Shiomi, Koto-ku, Tokyo
- Site area
- 32,233.97 m²
- Stage
- Complete (2023)
A new space created to provide a feel of wood while expanding a traditional joinery technique
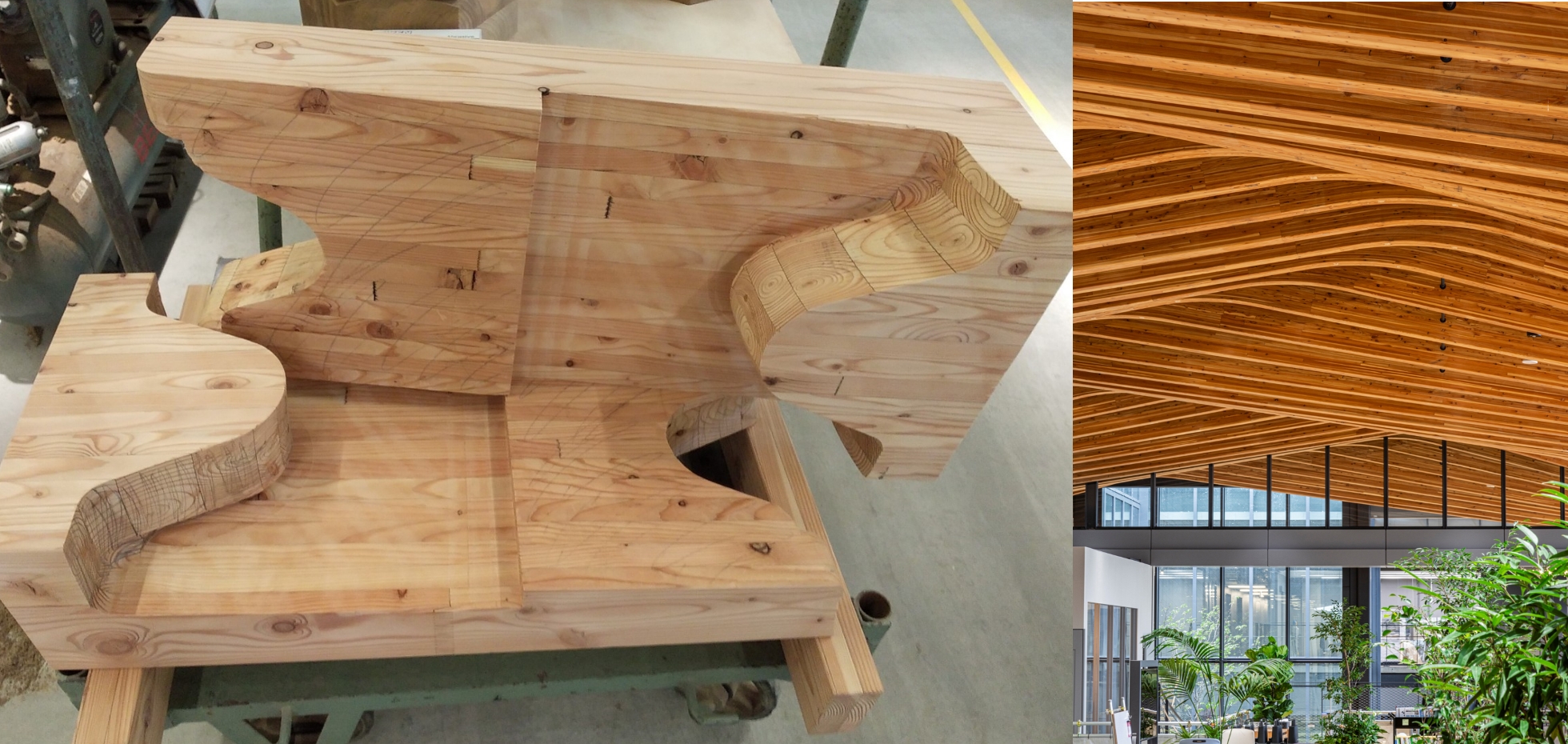
Shimizu celebrated its 220th anniversary in November 2023. Novare’s mission is to inherit the DNA of knowledge, technology, and human resources cultivated over the long history and tie it into innovations.
One of the five comprising facilities is the Novare Hub. Providing the core functions, it serves to connect all the facilities. It realizes a new creative space that promotes innovation by introducing systems, environmental plans, and new technology capable of responding flexibly to continually changing programs.
To bring greater warmth to the Novare Hub, where many people come and go or stay, a number of distinctive and bold wooden beams were installed in the third-floor hall and office. Here is a project that has developed and evolved traditional technologies into architectural construction that is only possible in the modern age.
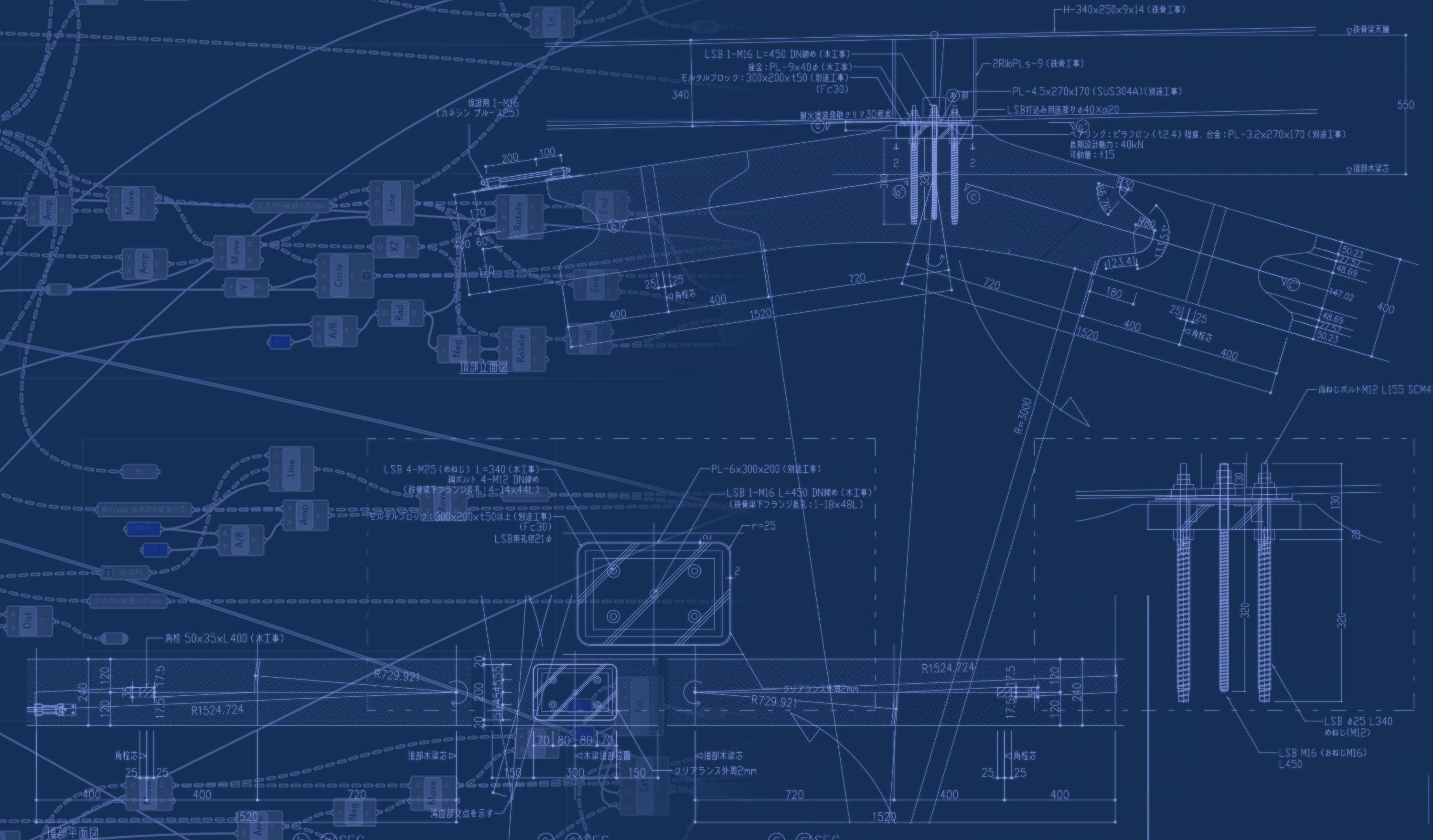
Birth of a new Japanese scarf joint that applies the principles of traditional technology
Using strong Japanese scarf joints in large-scale architectural construction
One traditional Japanese construction method considered for the ease of installing wooden beams was the Japanese scarf joint. In addition to being the most robust technique for fastening wooden pieces in place, also being used in the former Shibusawa Residence, the architectural work of Kisuke Shimizu II, standing in the center of Novare, contributed to the reason to employ the joinery technique.
There are two types of Japanese scarf joint. In this project, both awase-kanawa-tsugi (combined Japanese scarf joints) and kaiten-kanawa-tsugi (rotary Japanese scarf joints) are used in the design. The beams are made up of three components that are joined together, and these techniques are used to join the tops.
Computational design was employed for the joint to create a design that integrates a traditional joint. To use traditional Japanese scarf joints in large-scale architectural construction, the joints were reconstructed by modern technology to create a “new” Japanese scarf joint.
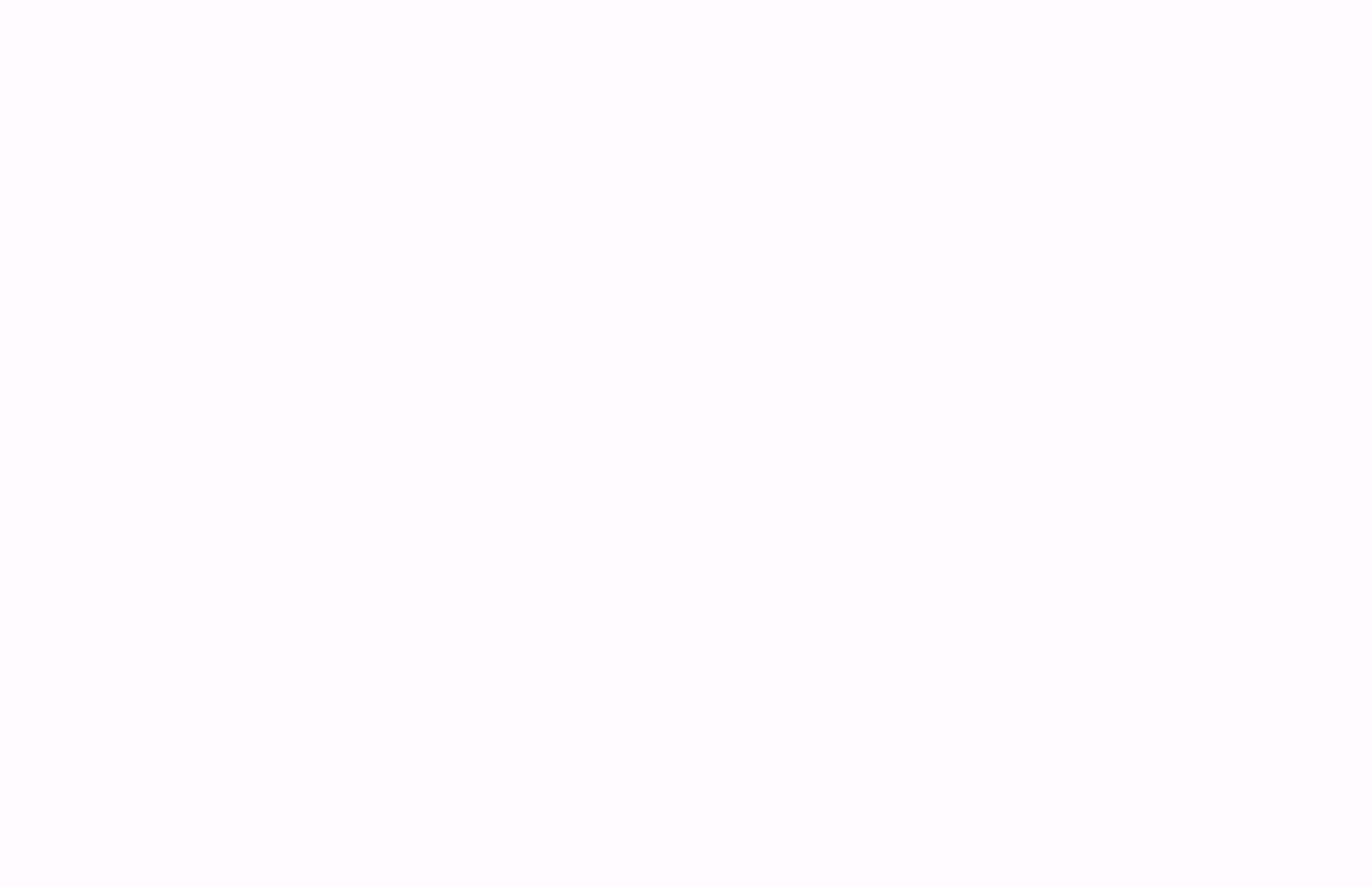
The blue pieces in the figure above are awase-kanawa-tsugi, the combined Japanese scarf joint, and the red piece is kaiten-kanawa-tsugi, the rotary one.
Pursuing structurally and aesthetically streamlined forms through computational design
Computational design was employed for the joint to create a design that integrates a traditional joint. The building spans 90 m, with a distance of 1 m between the wooden beams. The characteristic design where the top of the beams is curved is to hold up the entire roof evenly from below and prevent the roof's deformation. Because the joints at the top all have different angles, positions, and shapes, Grasshopper was used to generate and verify the model. This is from the perspective of both significantly reducing the time and effort required to create 2D drawings and conducting 3D-based reviews in a more streamlined manner.
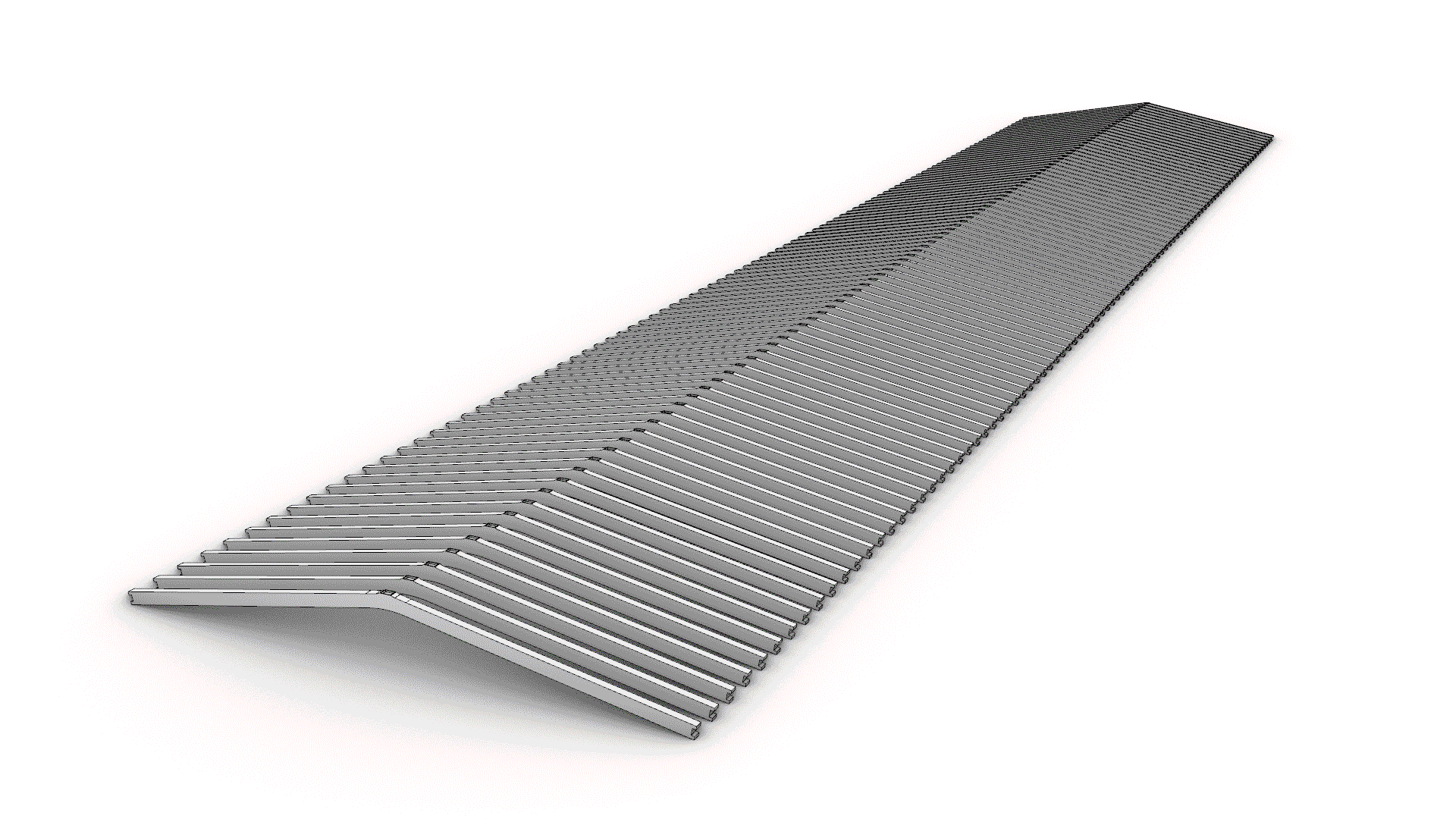
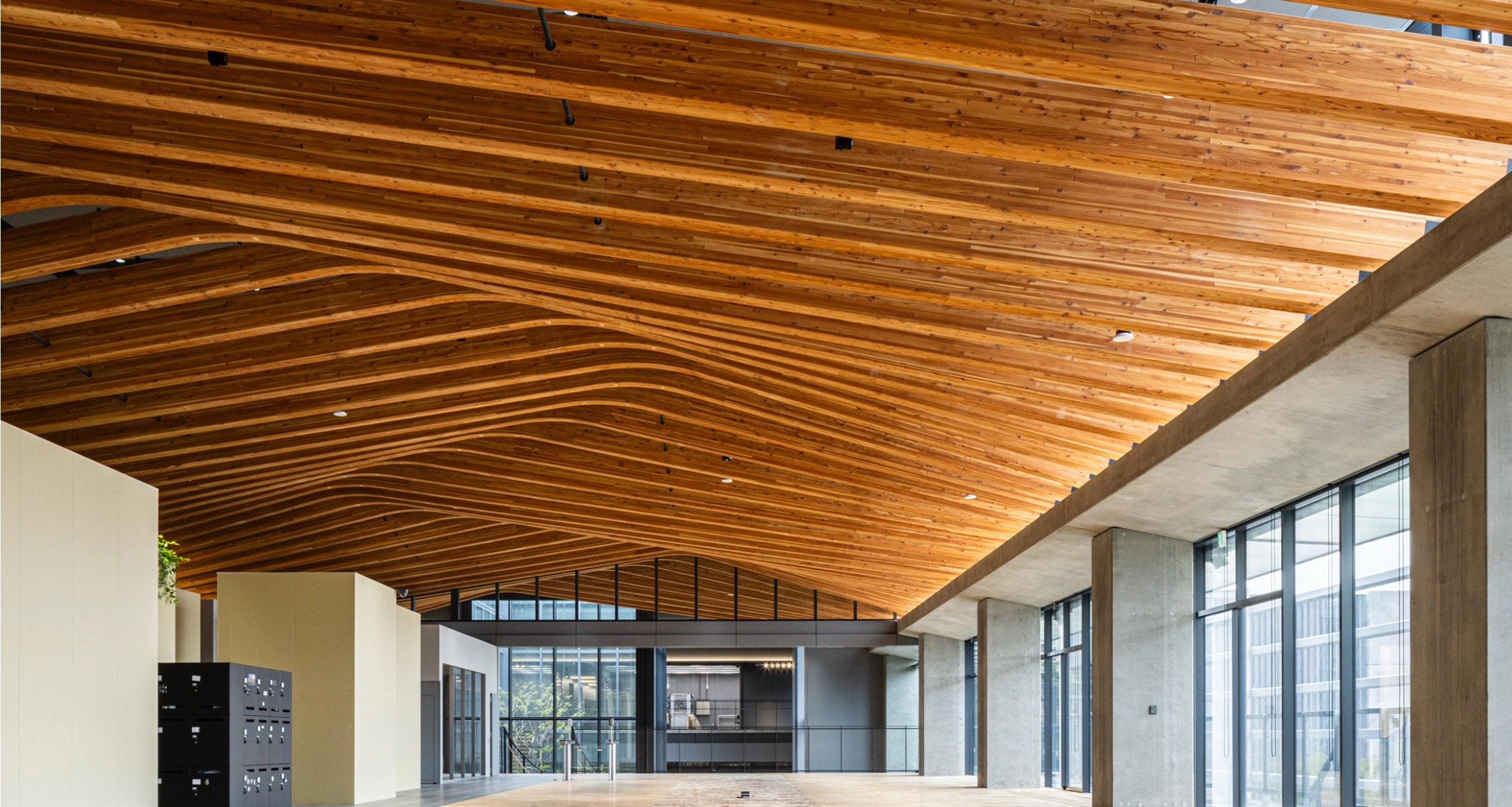
Wooden structures applicable to fire-resistant buildings in urban areas
Making use of wood in hybrid wooden framework
There has been demand for wooden frameworks as building structures in recent years. One of the challenges is how to use them within the constraints of fireproof buildings in urban areas. The hybrid wooden framework adopted for this project is an answer to that challenge. Wooden beams are assembled to support the steel-framed roof from below as part of a wooden structure that can also be used in fireproof buildings. Using wooden beams helps minimize the amount of steel used in the steel frame. Even if the roof deforms due to the loss of wood in a fire, the structure can support its own weight.
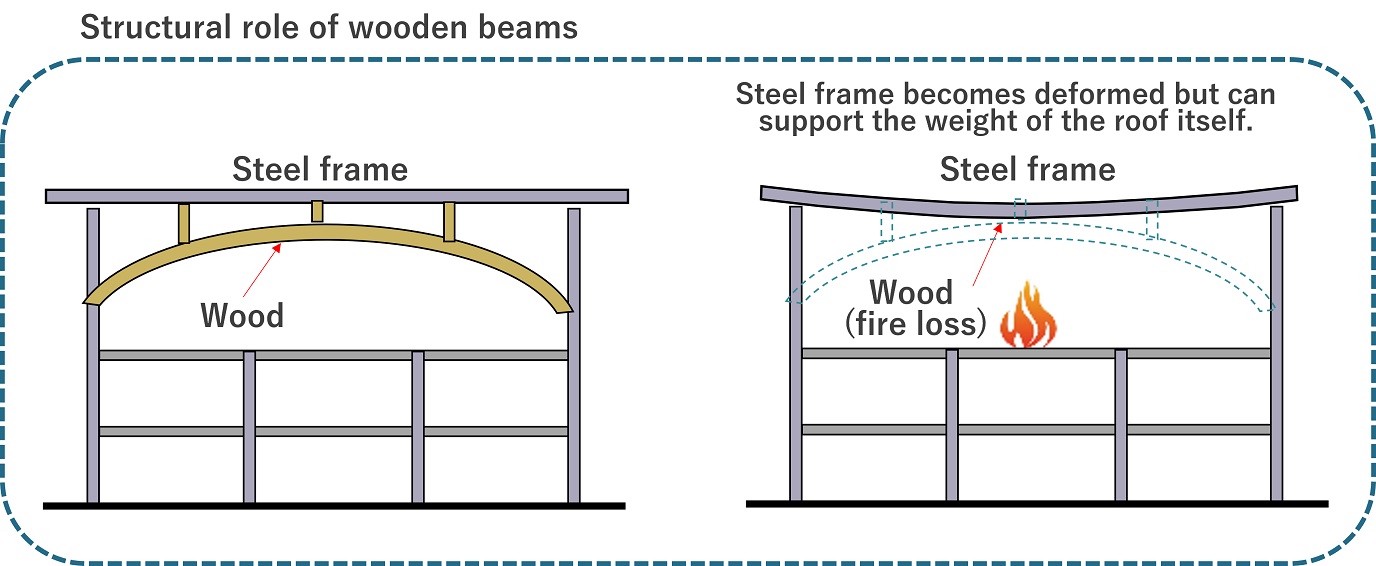
Structural verification making use of steel and wood
The Novare Hub has such a large column span that the cross-sectional size would have to be increased if the frame structure were made entirely of steel. Therefore, wooden beams were placed across the bottom of the steel beams, reducing the size of the steel beams at the top. Also, some ingenuity was employed in the arrangement of the wooden beams. When the vertices are arranged in a straight line, most of the deformation tends to occur in the center of the span. However, arranging the vertices in a wavy curved line can prevent this and reduce the amount of deformation. This is a streamlined structural plan that makes use of the characteristics of both steel and wood.
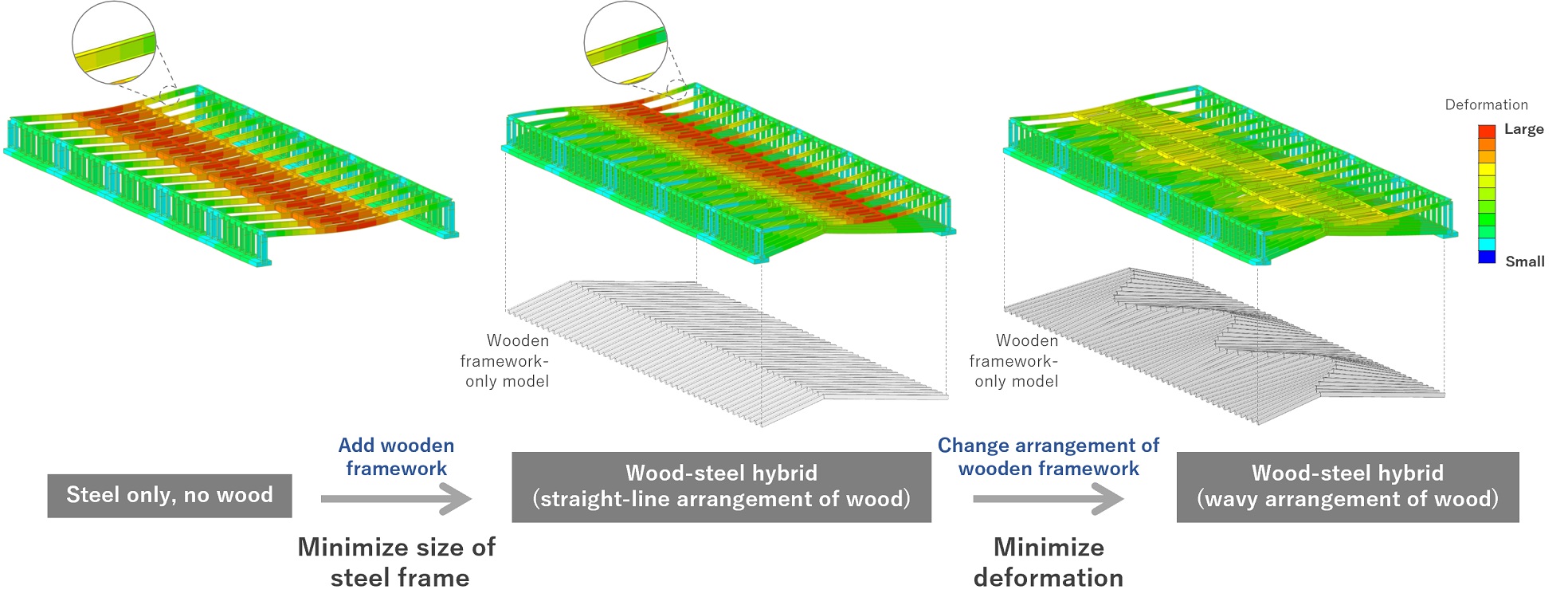
First, a straight arrangement of the wood was planned to reduce the size of the steel frame. Then, the wood was placed into a wavy arrangement to minimize deformation.
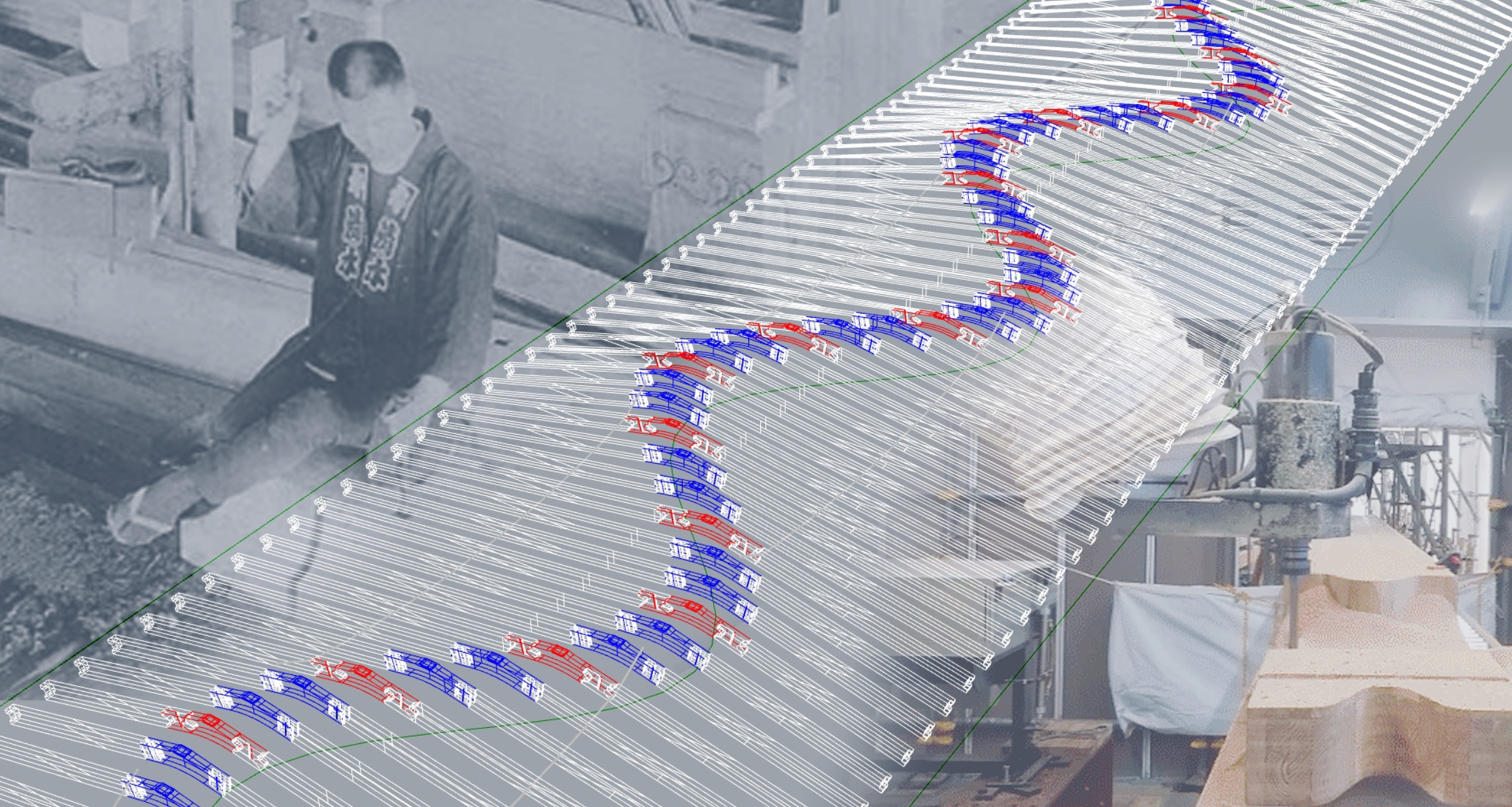
3D curved surface processing by multi-spindle machining robot
Digital fabrication using a multi-spindle machine for rotary Japanese scarf joints
To achieve the complex 3D curved surface of the Japanese scarf joint, an arm-type multi-spindle machining robot was used for wood processing. Unlike conventional robots that only operate on a single axis, this state-of-the-art robot can handle various 3D machining operations, allowing it to process large quantities of complex, multi-patterned shapes. This “new” Japanese scarf joint maximizes the advantages of the multi-spindle machining robot and was reproduced using 3D model data developed through extensive studies.
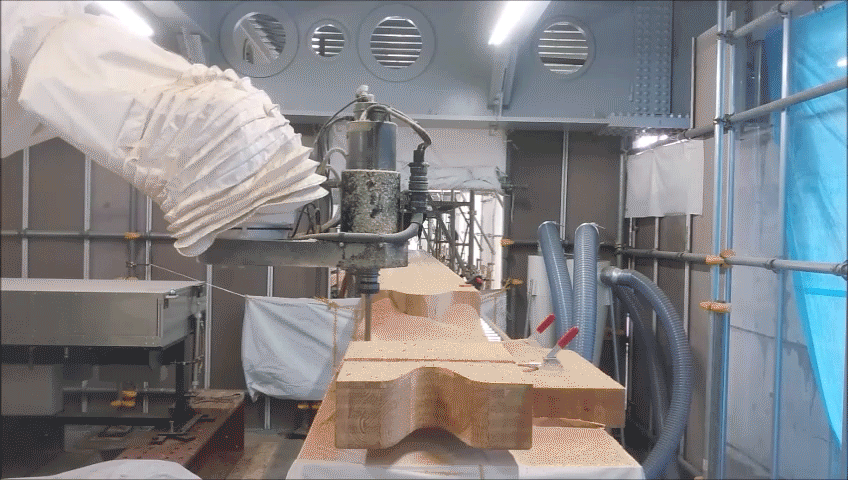
Wood Processing Robot No. 1. The maximum processing area is 600 mm high x 900 mm deep x 3,000 mm long.
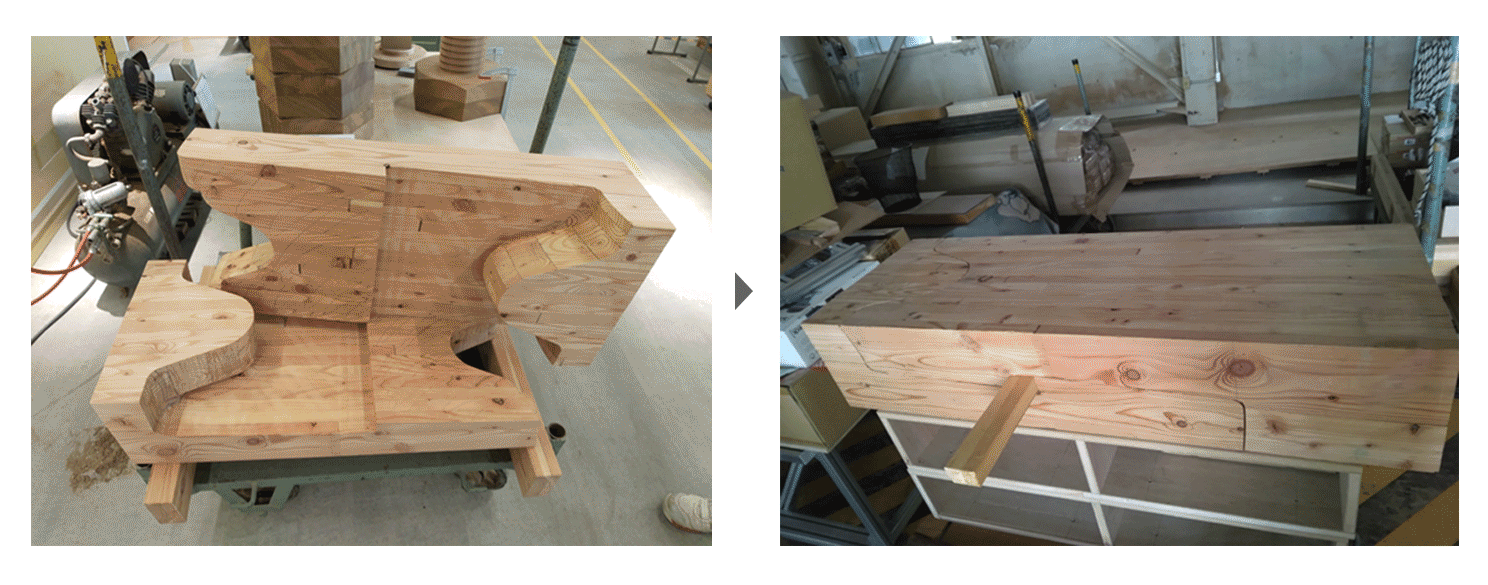
This rotary Japanese scarf joint was completed by robotic carving. The parts fit together perfectly, without the slightest deviation, as shown in the photograph on the right.
Digital fabrication, a technology that uses digital data to create objects, allows to make objects that are tailored to location and conditions rather than mass-produced. Because it is also highly compatible with generative AI, its use will likely spread.
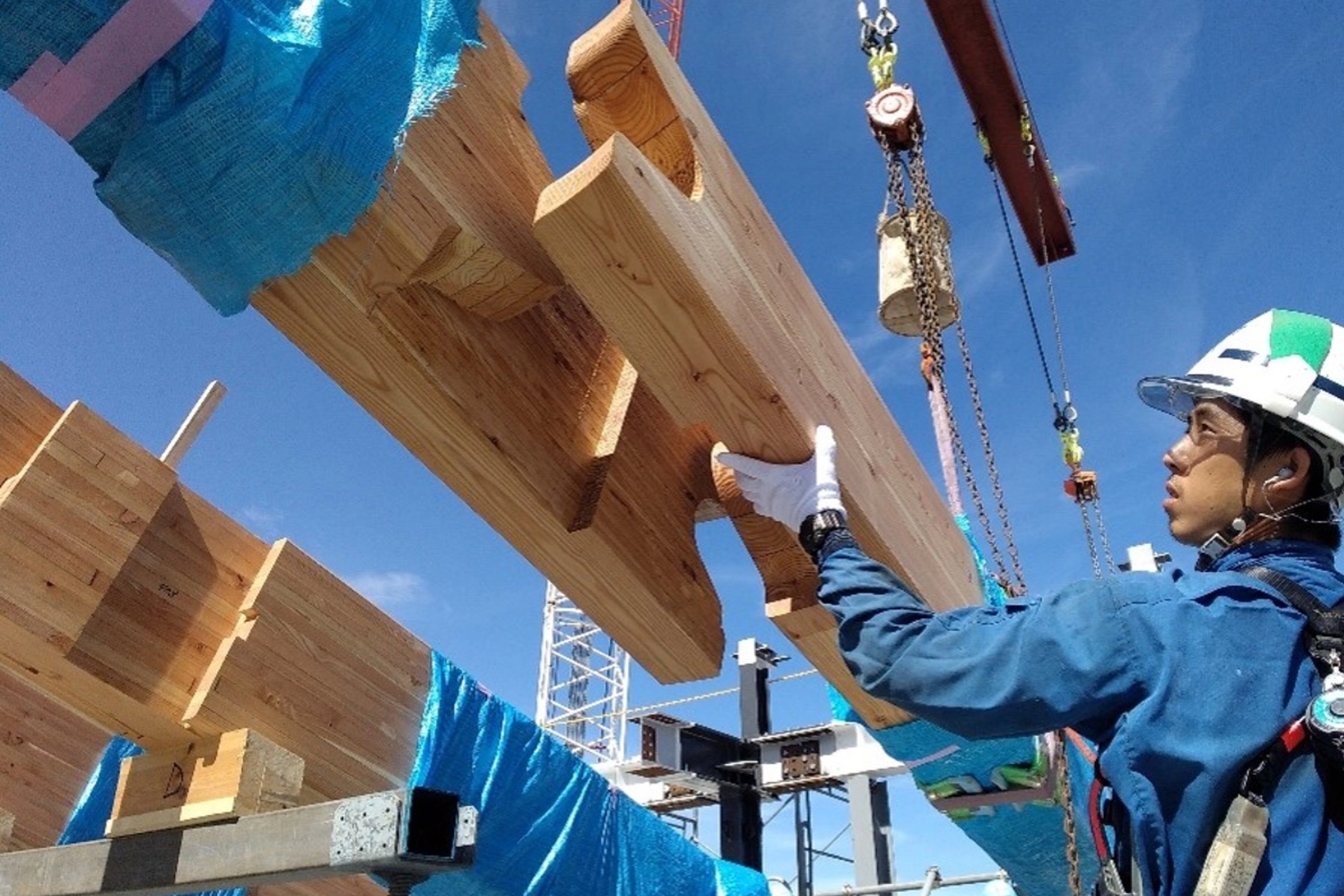
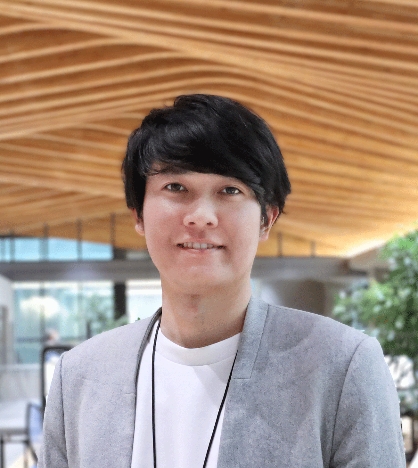
Architectural design
Hideyuki Inaba
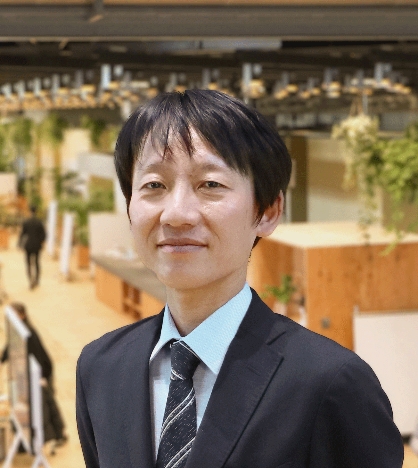
Structural design
Hatsutaro Tanaka
Streamlining the design of a new space that provides a feel of wood using traditional techniques.
To create a comfortable space, the Novare Hub actively incorporates wood, specifically adopting a hybrid wooden structure to utilize wood as a structural element.
Grasshopper was used for the Japanese scarf joints at the top because their vertices flow in a sine curve, forming irregular shapes. With the use of this technology, the design team gained a solid sense that it has become easier to achieve complex shapes and various designs. In addition, the wood used in this project was processed based on the 3D data created in the design stage, achieving a consistent digital fabrication process from design to production.
This project made the team realize the potential of digital fabrication to advance design without compromising it, even amidst labor shortages and workforce reductions.