Interior and alcove post of former Shibusawa Residence where Eiichi Shibusawa lived from 1840 to 1931
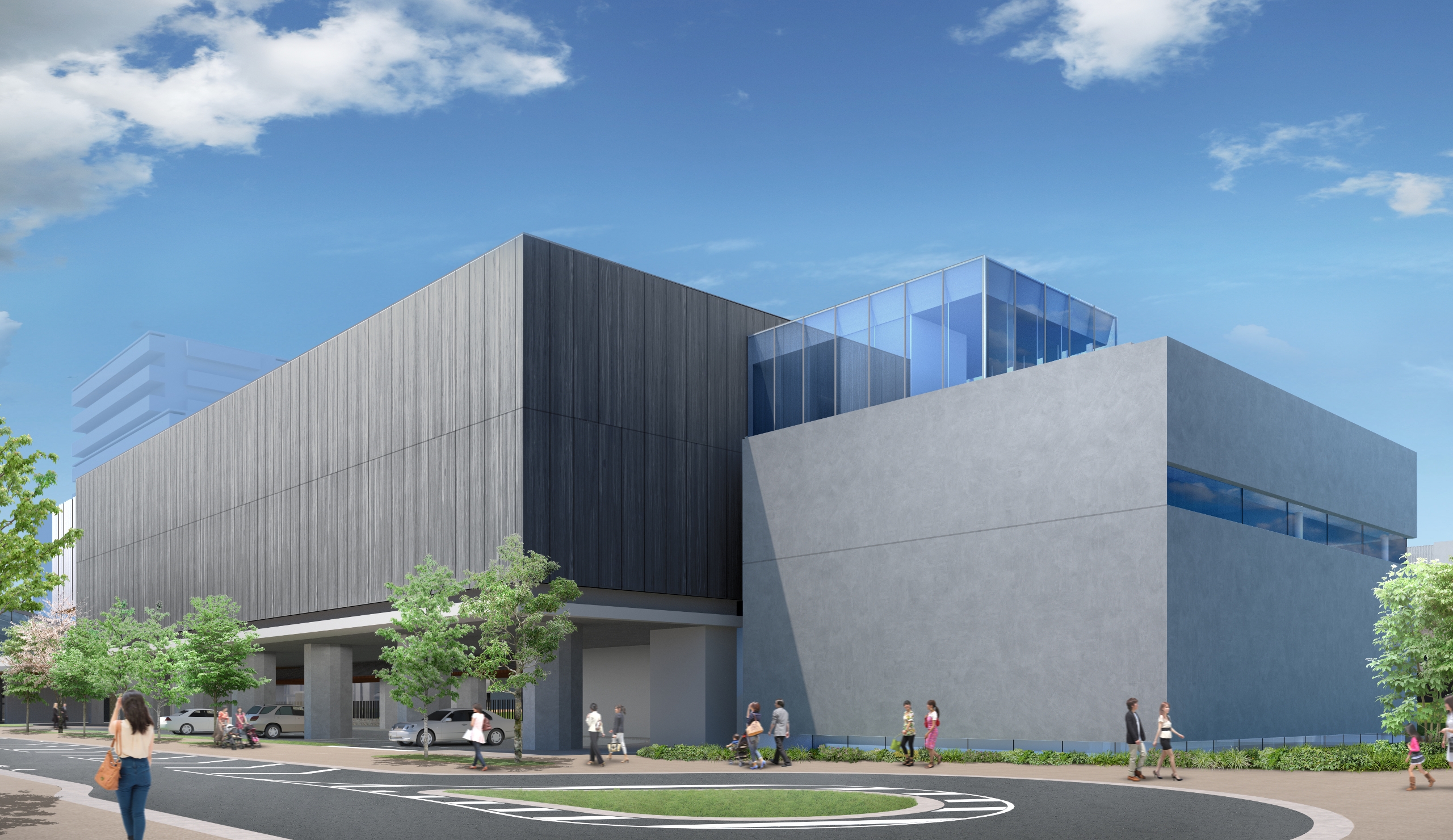
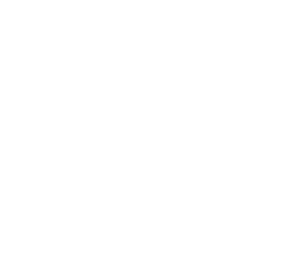
Smart Innovation Ecosystem Novare
(Delving into the Mind of Kisuke Shimizu II with AI)
Novare: A new platform that creates next generation of innovation
Novare is an open innovation hub nestled in Shiomi, Koto-ku, Tokyo. Its name, derived from the Latin word for “to create” or “to renew,” embodies its purpose—to create a place for new invention by bringing together knowledge from Japan and overseas. Comprised by five facilities which work both independently and collaboratively, Novare mirrors the intricate ecosystems of nature, all converging at the heart of monozukuri (superb craftsmanship).
- Project site
- Shiomi, Koto-ku, Tokyo
- Site area
- 32,233.97 m²
- Stage
- Complete (2023)
Reviving the Craftsmanship of Kisuke Shimizu II with AI to Design Exterior Panels
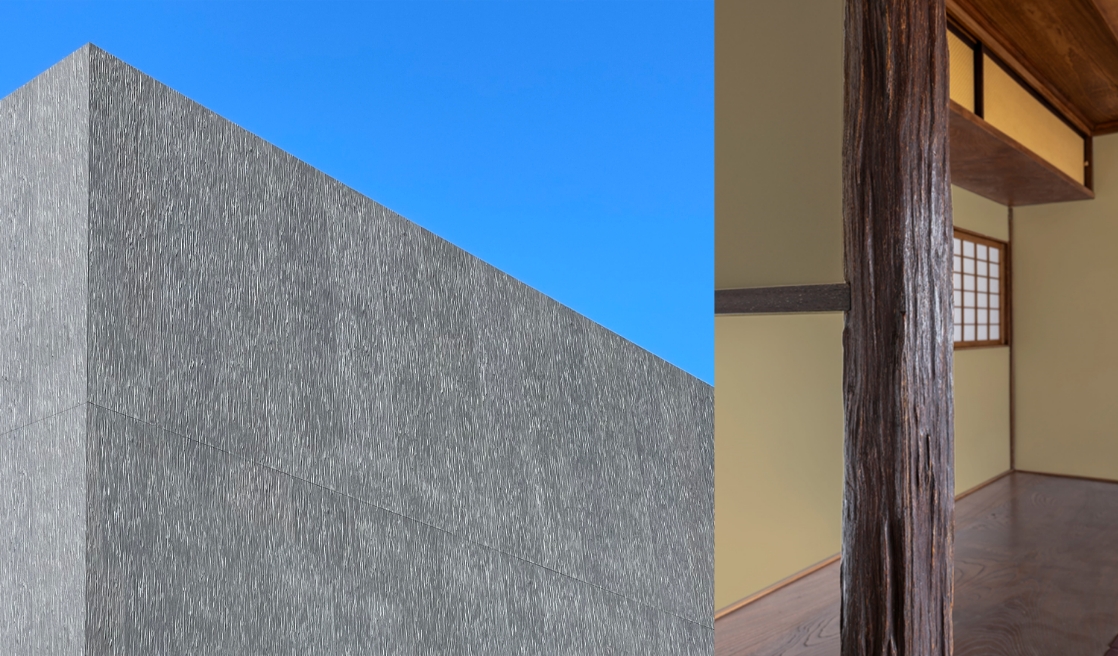
Shimizu celebrated its 220th anniversary in November 2023. Novare’s mission is to inherit the DNA of knowledge, technology, and human resources cultivated over the long history and tie it into innovations.
One of the five facilities comprising the hub is the Novare Archives (Shimizu Corporation Historical Archives). Technological and academic materials, items of high cultural value in its collection and other innovation created by predecessors are stored in the facility, which means this facility exhibits Shimizu’s path of challenge. Visitors are offered an overview of past and present works that illustrate the history of the Japanese construction industry. The message is also found in the distinctive exterior walls of the building.
At the center of Novare is the former Shibusawa Residence built by Kisuke Shimizu II. Using proprietary AI technology, a clone-like 3D pattern of this alcove post technique was generated and engraved onto the exterior walls of the building as a reminder of Shimizu’s origins. Let’s look at the project where the latest AI technology was used to delve into Kisuke Shimizu II’s craftsmanship.
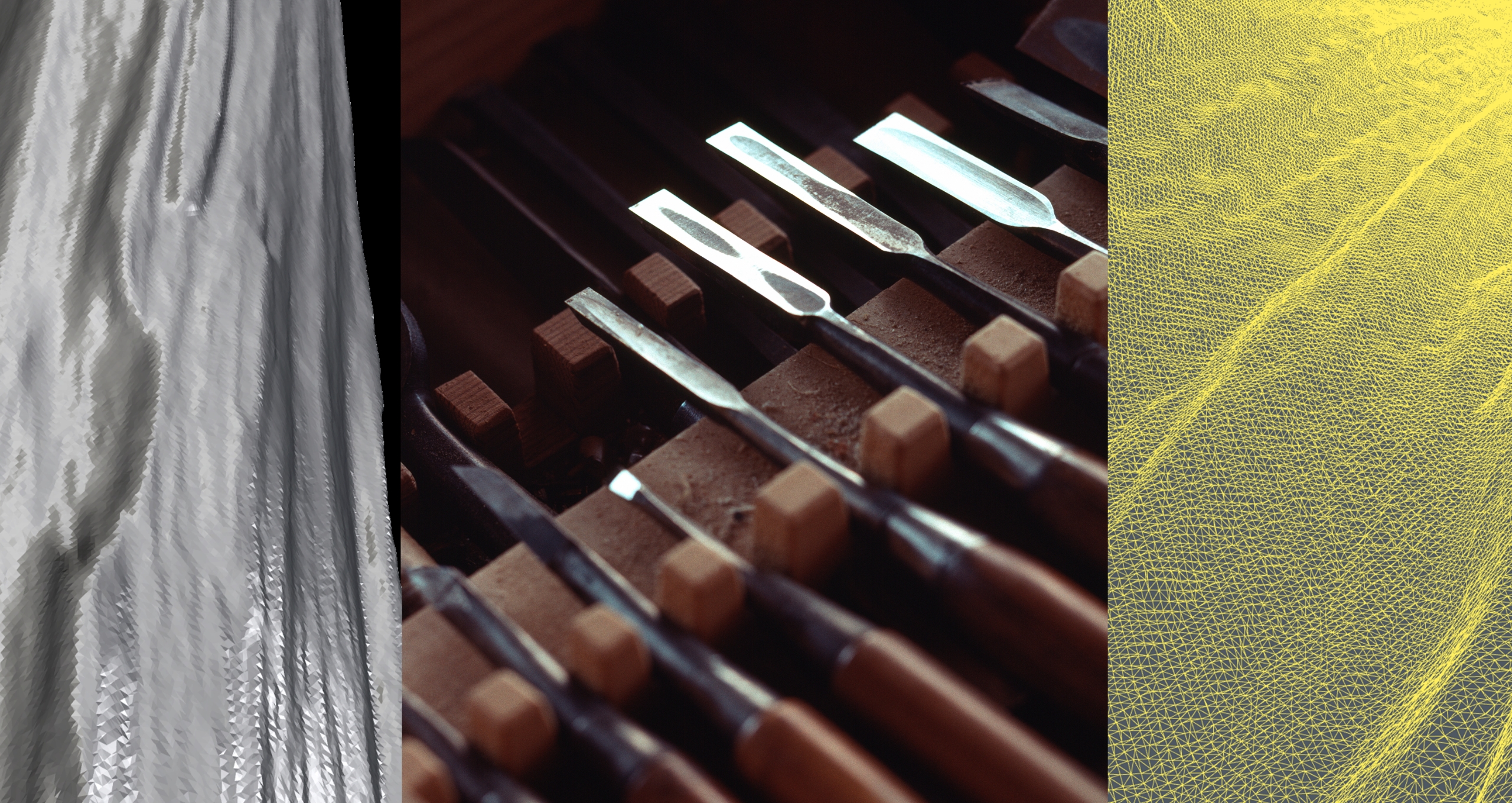
Using digital technology to analyze the thoughts and techniques of our predecessors through Chisel marks left by Kisuke Shimizu II
The only architectural work of Kisuke Shimizu II remaining to this day
Kisuke Shimizu was the second-generation owner of the Company, working from the late Edo period to the Meiji period. He is known as a pioneer of modern architecture in Japan, having created a quasi-Western style based on traditional Japanese architectural techniques. This includes the Tsukiji Hotel Building, the Daiichi Kokuritsu Ginko (former Mitsuigumi House), and the Kawase Bank Mitsuigumi.
The only remaining building that Kisuke Shimizu II worked on is the former Shibusawa Residence located in the center of Novare. Eiichi Shibusawa, often called the “father of modern Japanese capitalism,” his children, grandchildren, and great-grandchildren lived in the house for four generations. It was originally built in Fukagawa-Fukuzumi-cho (now Eitai, Koto-ku). and relocated for the third time after previously being moved to Mita-Tsunamachi (now Mita, Minato-ku), and to Rokunohe-machi, Aomori. It is preserved at Novare as the DNA of Shimizu Corporation and a cultural heritage that should be passed on to future generations.
The alcove posts in the house are said to have been hand-carved by Kisuke Shimizu II, resembling naturally formed grooves and grains found in meiboku or precious wood. It is said that Kisuke Shimizu II came up with a way to make materials look high-end, realized by Eiichi Shibusawa’s statement that “you don’t need anything extravagant.”
Inspired by this episode, we believed it tied into our corporate credo, “The Analects and the Abacus (Ethics and Economics),” and started this project with our eagerness to pass it on to future generations.
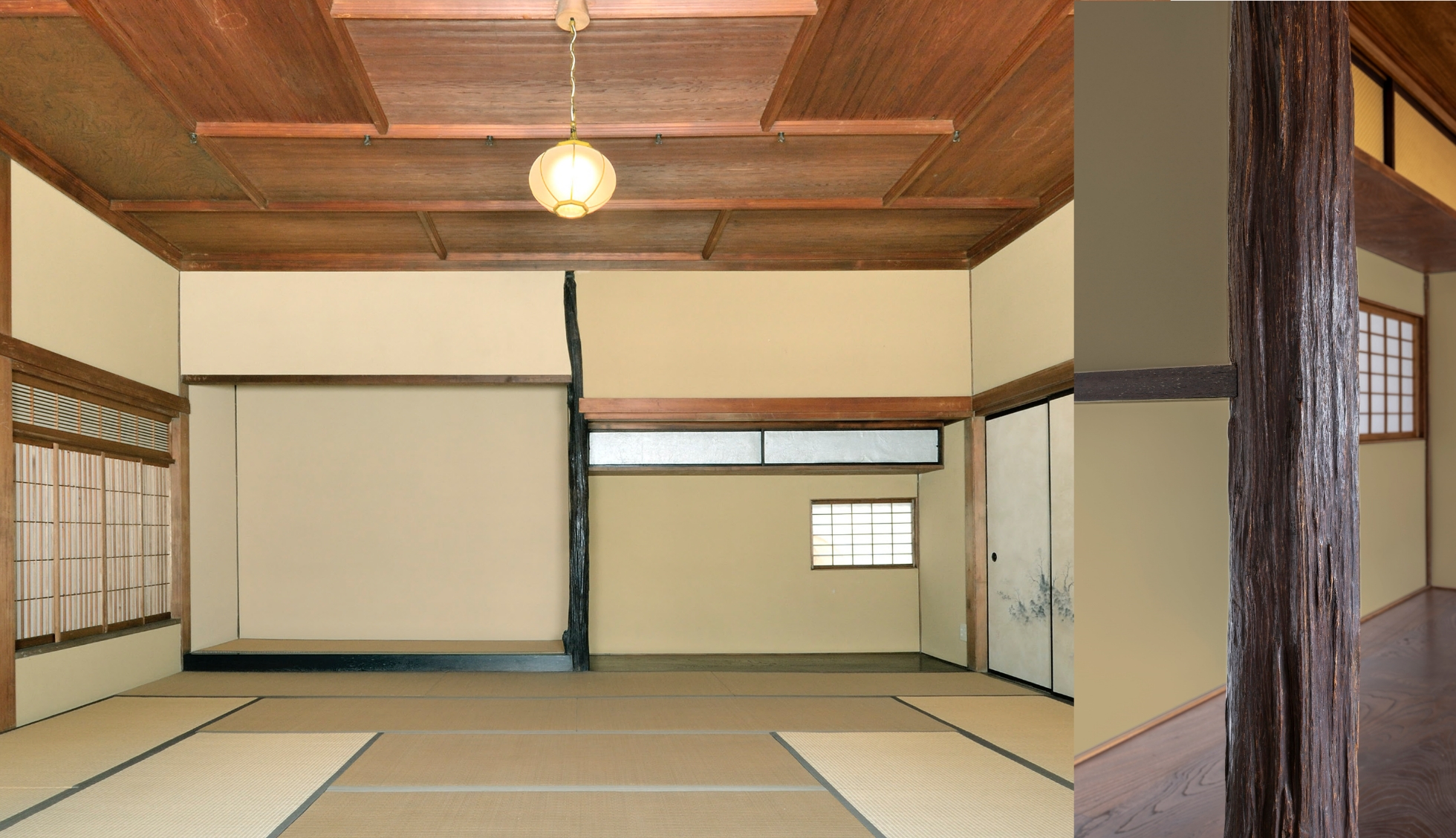
Scanning a real object and using algorithms to develop it into panels
We decided to utilize an alcove post pattern for the exterior walls but encountered several issues. First, we tried to transfer the pattern as-is, but it did not match to the scale of the exterior wall that was much larger in area, resulting in a low-resolution mosaic. Then, when copying the pattern repeatedly, it looked as though it were just pasted side by side, creating a design that was not appropriate for a building. For that reason, digital technology was used to analyze the thoughts and techniques of our predecessors.
The alcove posts had been disassembled for relocation, so the timing was perfect for obtaining an actual object to scan. After scanning one and incorporating it into a 3D model, we created an algorithm to make it into panels as if thinly slicing it into long strips while preserving its appearance.
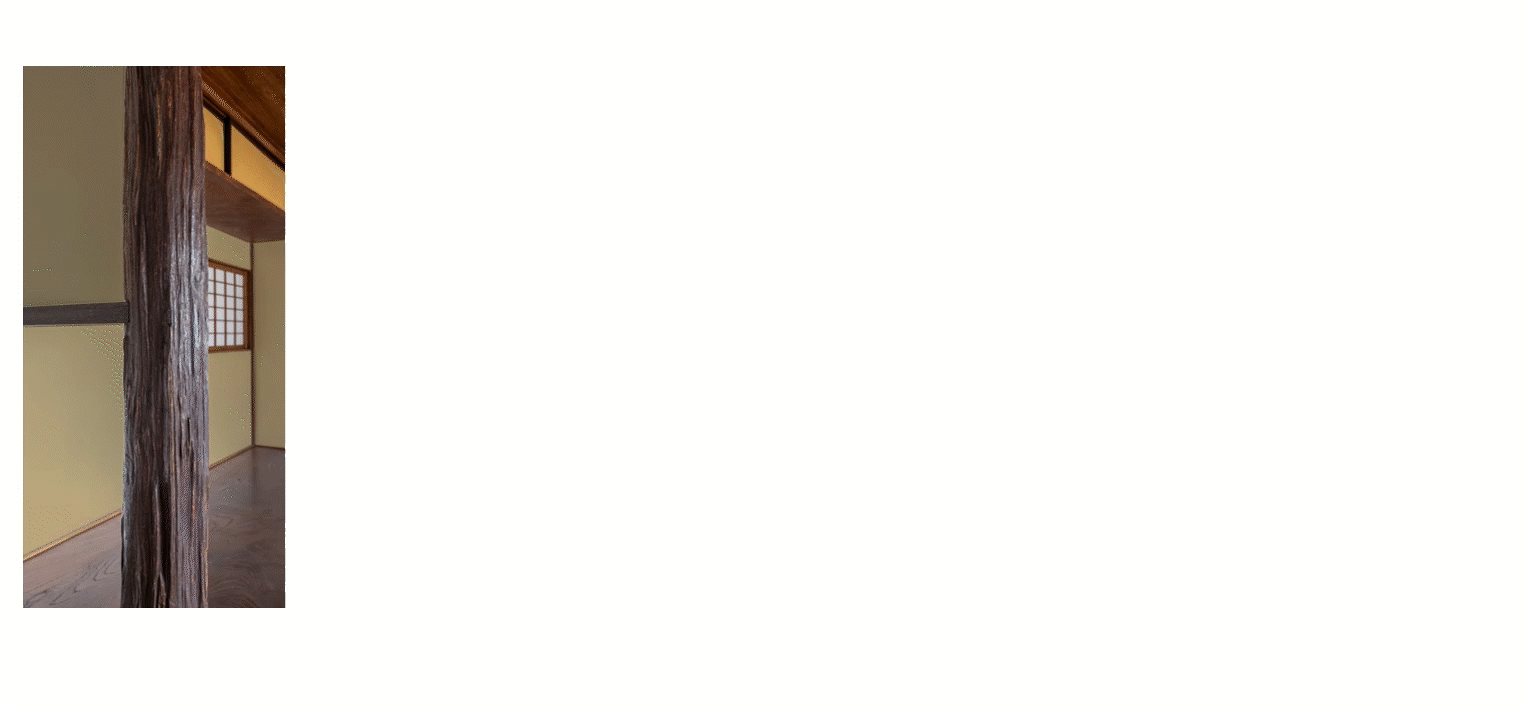
Developing an original algorithm to turn 3D scanned data into flat panels
Expanding the distinctive design using generative AI to incorporate it into a vast canvas
After the base design has been extracted, it was incorporated into the vast canvas. The pattern was extended while capturing the expressive characteristics of the image. We devised the idea of utilizing generative adversarial network (GAN) technology, which learns characteristics from data to produce/transform non-existent data. After comparing and considering various AIs, we adopted a generative AI called SinGAN, which captures the characteristics of a single image and generates similar ones.
The first step was to expand the original image (300 mm x 1,375 mm) to an area 16 times larger (1,200 mm x 5,500 mm) by quadrupling the long and short sides. Then, 50 images were generated based on the characteristics of the pattern. After that, the designs were carefully selected, narrowing them down to four images to actually make models of.
When selecting the four images, since it wasn’t possible to make the decision just by looking at them on a flat surface, we converted them into 3D digital mock-ups and examined them from various angles in VR. As AI sometimes produces unnatural parts that are not in the real thing, the final selection had to be made by the human eye.
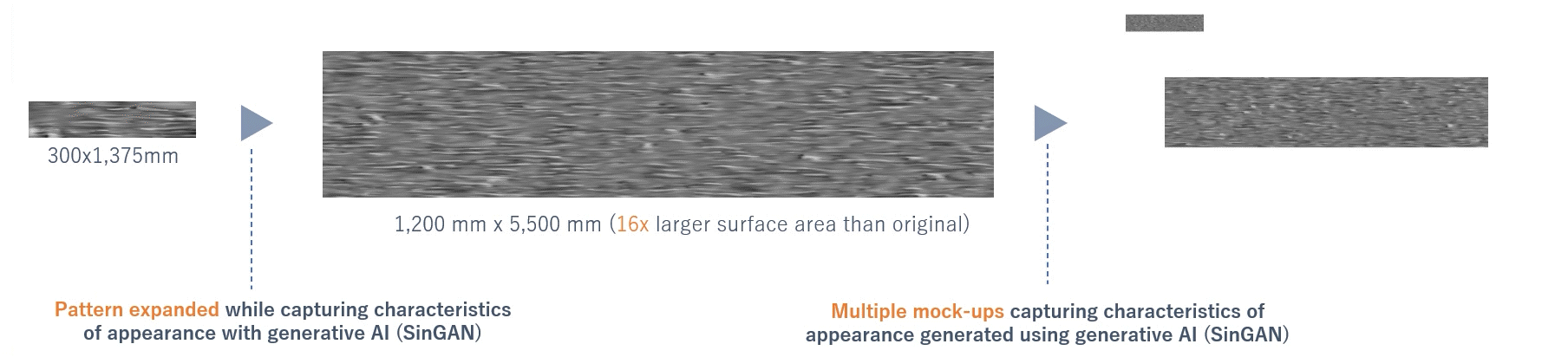
Creating multiple designs using generative AI to expand patterns while capturing characteristics
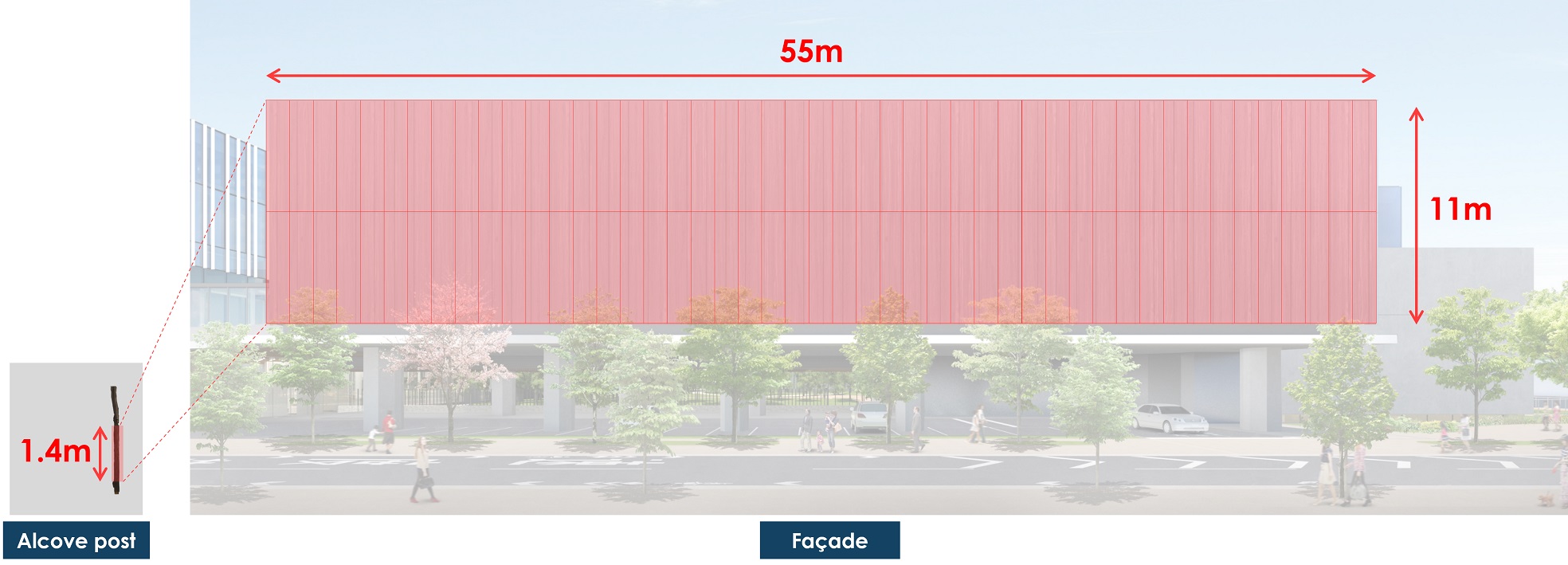
Massive exterior wall of Novare Archives, where panels are installed, measures 55 meters wide by 11 meters tall.
Replicating subtle irregularities (chisel marks) undetectable by 3D scanning
In addition, when creating patterns, the 3D scans simply could not detect subtle undulation such as chisel marks.
Therefore, we conducted a parametric study (analysis with varying parameters) and restored them with a 3D model.
The image on the right is the photograph of the actual object and the model reproduced based on it.
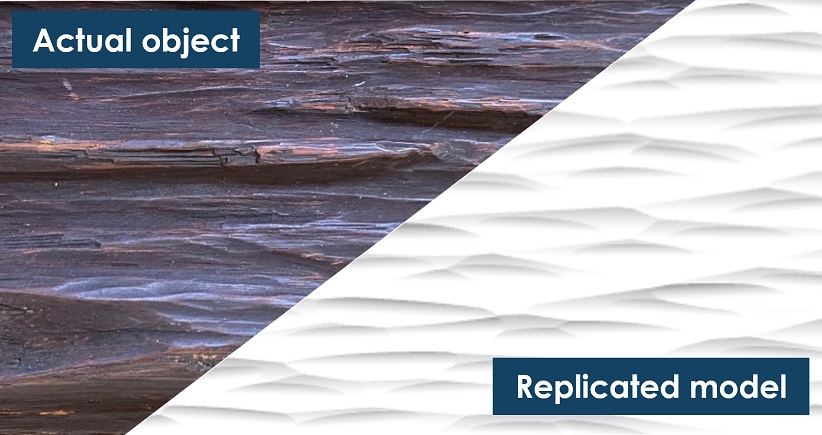
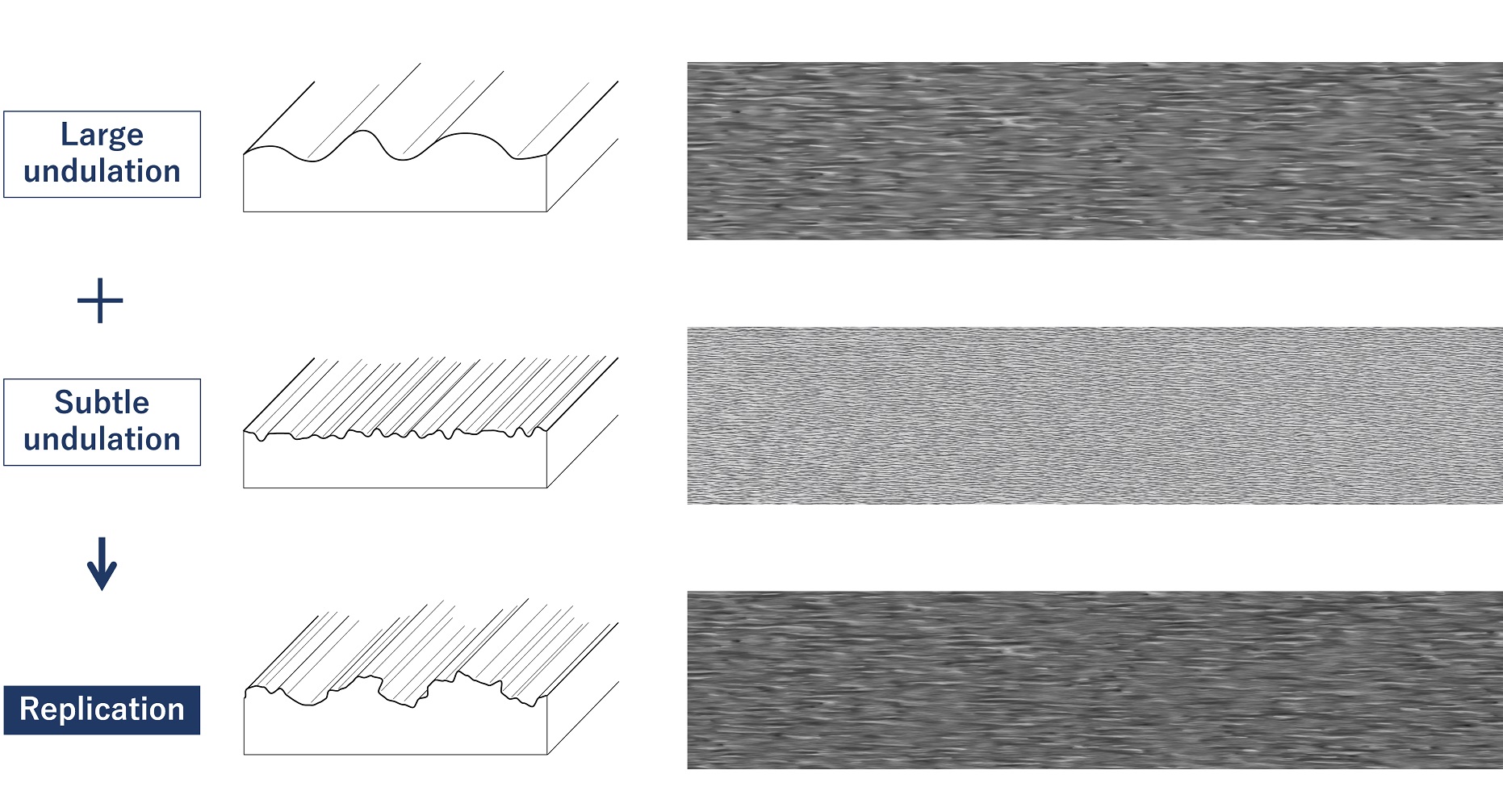
The graininess is replicated by scanning harsh and subtle undulation and then combining them.

Before (left) and after (right) replication of subtle undulation
One of the reasons we used generative AI for the patterns of the alcove post was that it could generate the patterns in a few seconds, which would be impossible for humans. We realized the unique ability of generative AI to connect patterns seamlessly and naturally without compromising authenticity.
There was also a custom-made aspect. We believe that incorporating the thoughts and DNA in an object and developing them into architecture, as we did with the alcove post, will create an affection for the building, thereby enhancing its value. The use of AI in architecture is expected to evolve. We took the first step by using generative AI in this project.
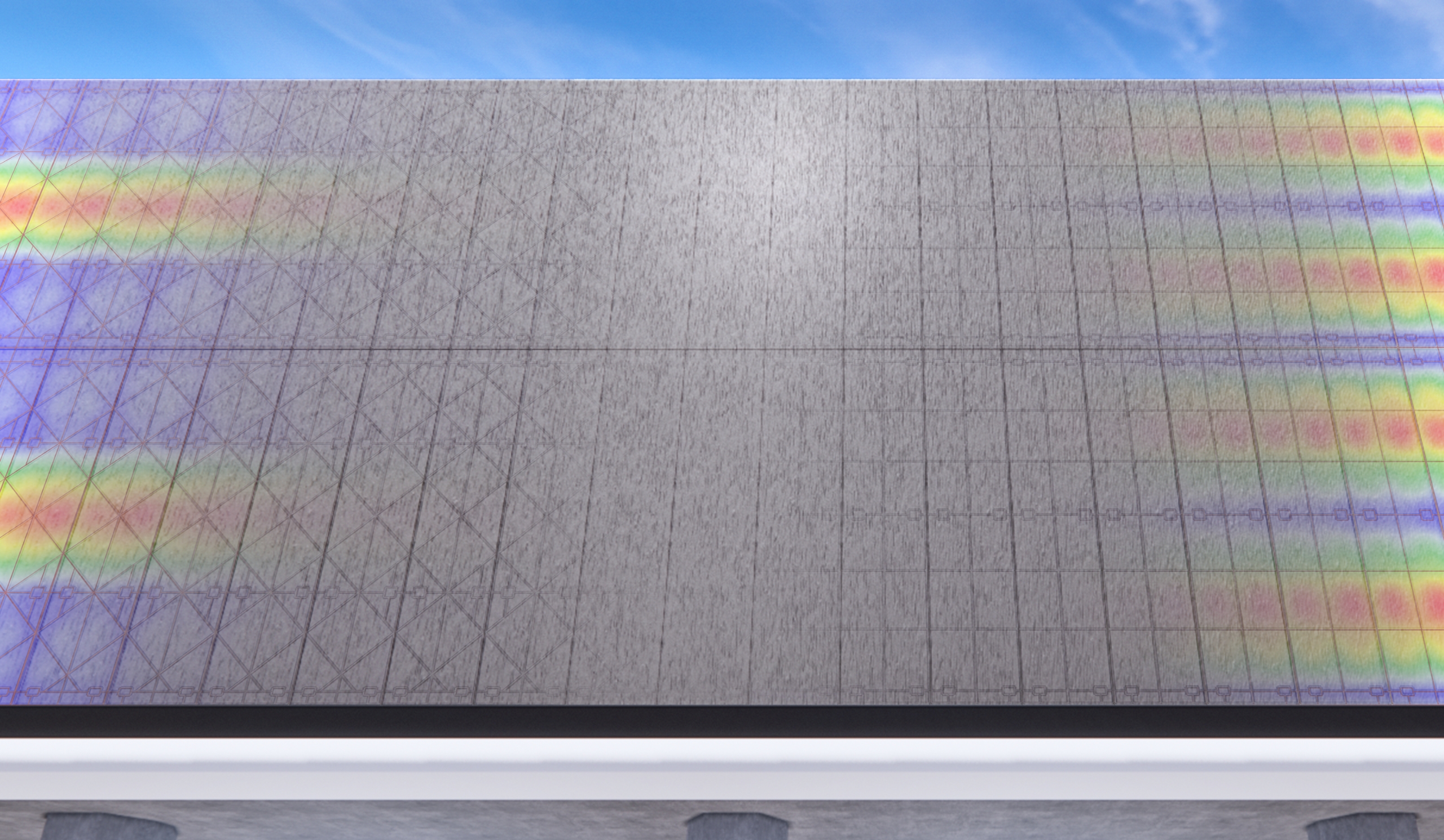
Implementing a structural simulation for wind load
First in-house application of Grasshopper’s Karamba plug-in to an aluminum structure
In addition to the design, a new attempt was made on the exterior wall structure. We used Grasshopper’s structural analysis plug-in, Karamba, to simulate the wind load on the structure. This was the first in-house example of applying Karamba to an aluminum structure.
When aluminum panels are used as exterior walls, a base steel frame is usually placed on the inside to bear the load of external forces from outside, such as wind load. In this project, we considered designing the backside of the panels with the necessary shape to withstand external forces and omitting the base steel frame because of the degree of freedom available in terms of shape due to making the panels from a mold.
For that reason, we used Grasshopper not only to create the ribs for the panel attachment and waterstops but also to instantly generate various panel shapes with different arrangements of the structurally required ribs. We then used Karamba for stress analysis. The panel thickness was calculated with each panel element to satisfy the required strength, and the necessary thickness was verified using contour diagrams.
After reviewing the simulation results and considering the ease of fabrication and installation, we decided to proceed based on a cross-shaped rib configuration. Basing on the results obtained, we used Midas iGen to perform a detailed study and determined the final specifications.
Karamba is rarely applied to aluminum structures at building scale, even overseas. Utilizing computational design in the initial study proved beneficial also in terms of design and cost in the field of structural engineering.
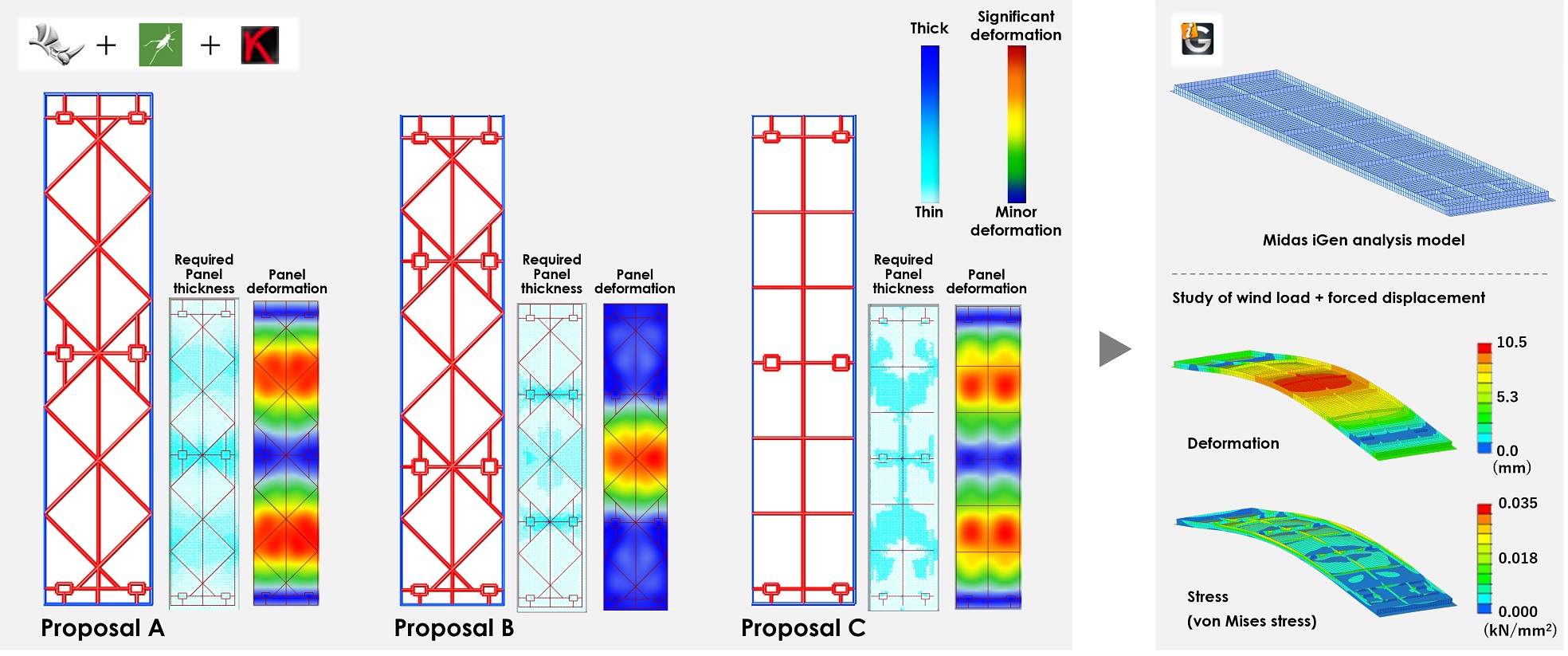
Left: Proposals A, B, and C with different rib shapes. Karamba provides the required thickness to satisfy the design criteria (the ratio between the maximum load a structure can support and the maximum load it is expected to encounter) and the amount of deformation when the required thickness is accommodated.
Right: Final detailed study performed using Midas iGen
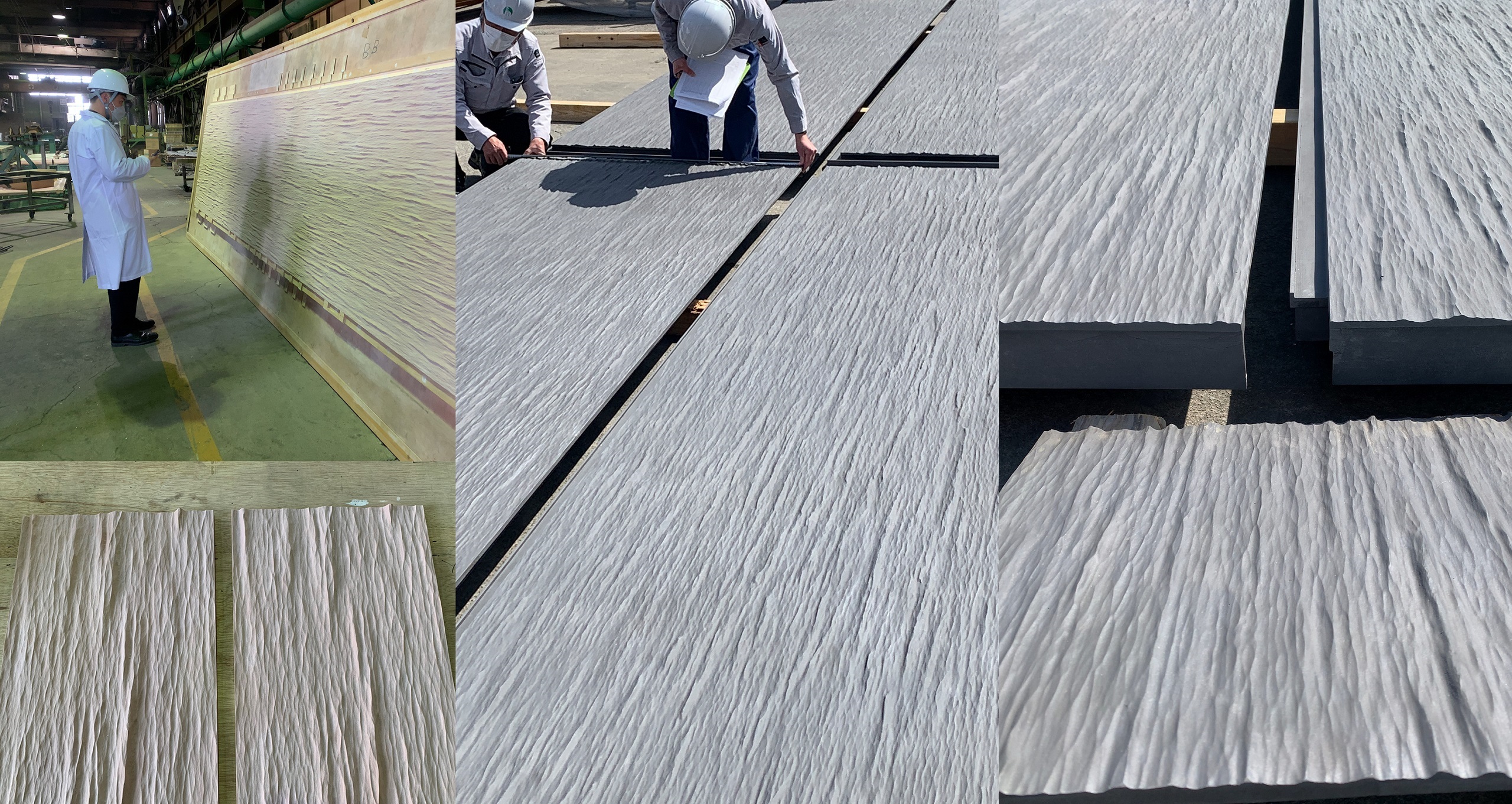
Checking design with digital technology 3D data linking to construction
Checking using real-time rendering and VR
Using an in-house plaster 3D printer to create 11 mock-ups
For this project, digital technology was also used to check the design. First, we used our in-house plaster 3D printer to create mock-ups based on the 3D model. Since the shape is replicated as-is, we checked the roughness by holding it in our hands and shining the light on it. We repeated this process 11 times as part of trial and error.
At the same time, we created about 20 digital mock-ups using the 3D modeling software Rhinoceros and the rendering software Enscape. We then used VR to check how the exterior walls would look depending on the environment by changing the time/date, the way the sunlight hits, and the angle.
These exterior wall panels are designed for the pattern to continue seamlessly at panel joints. Normally, we would have to have more mold types, but we used digital design so that only the relevant parts have a seamless pattern. This allowed us to create a seamless pattern while keeping the number of molds low. The joints between the panels were also made as thin as possible to create a continuous pattern, providing the appearance of one large piece.
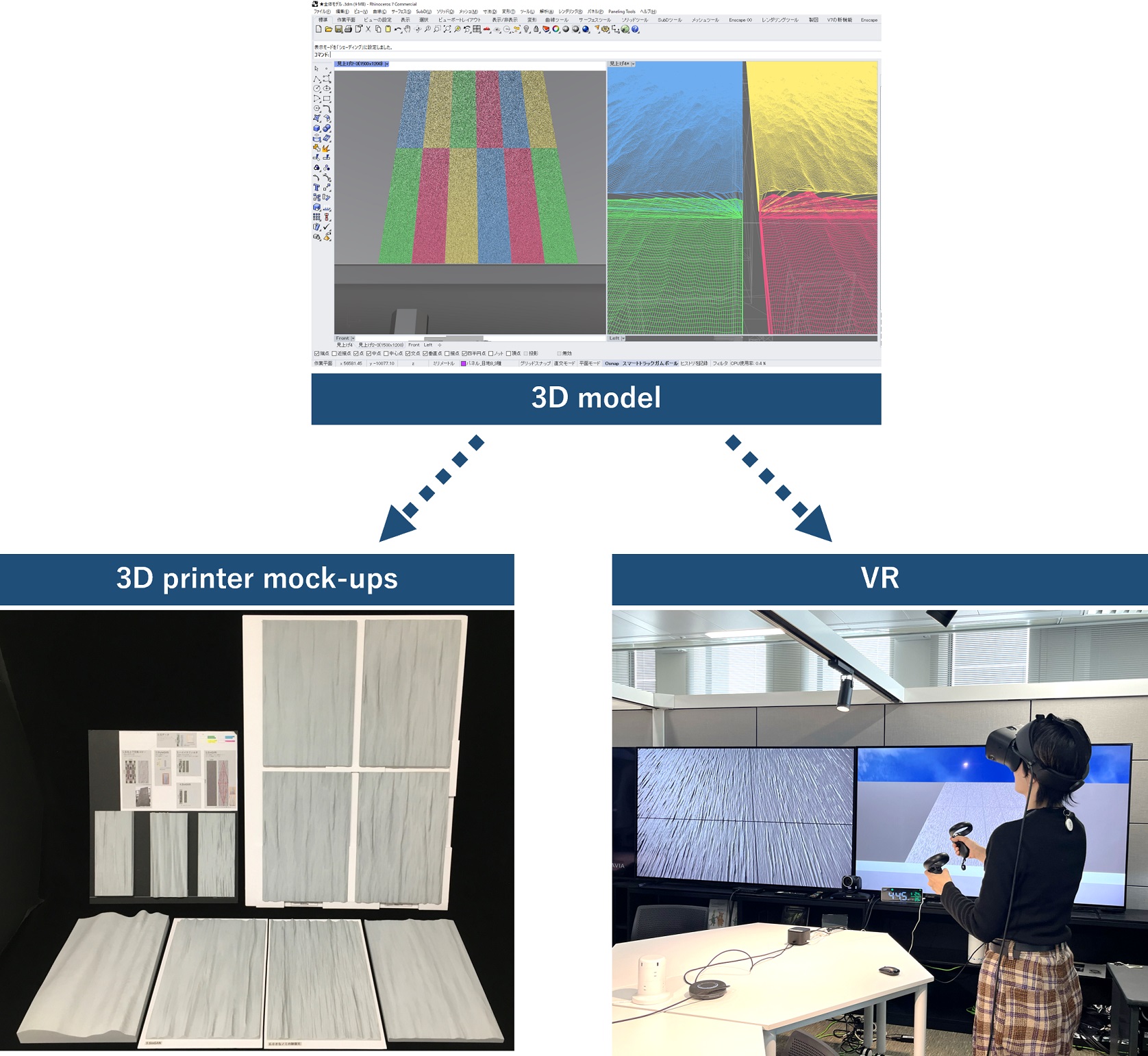
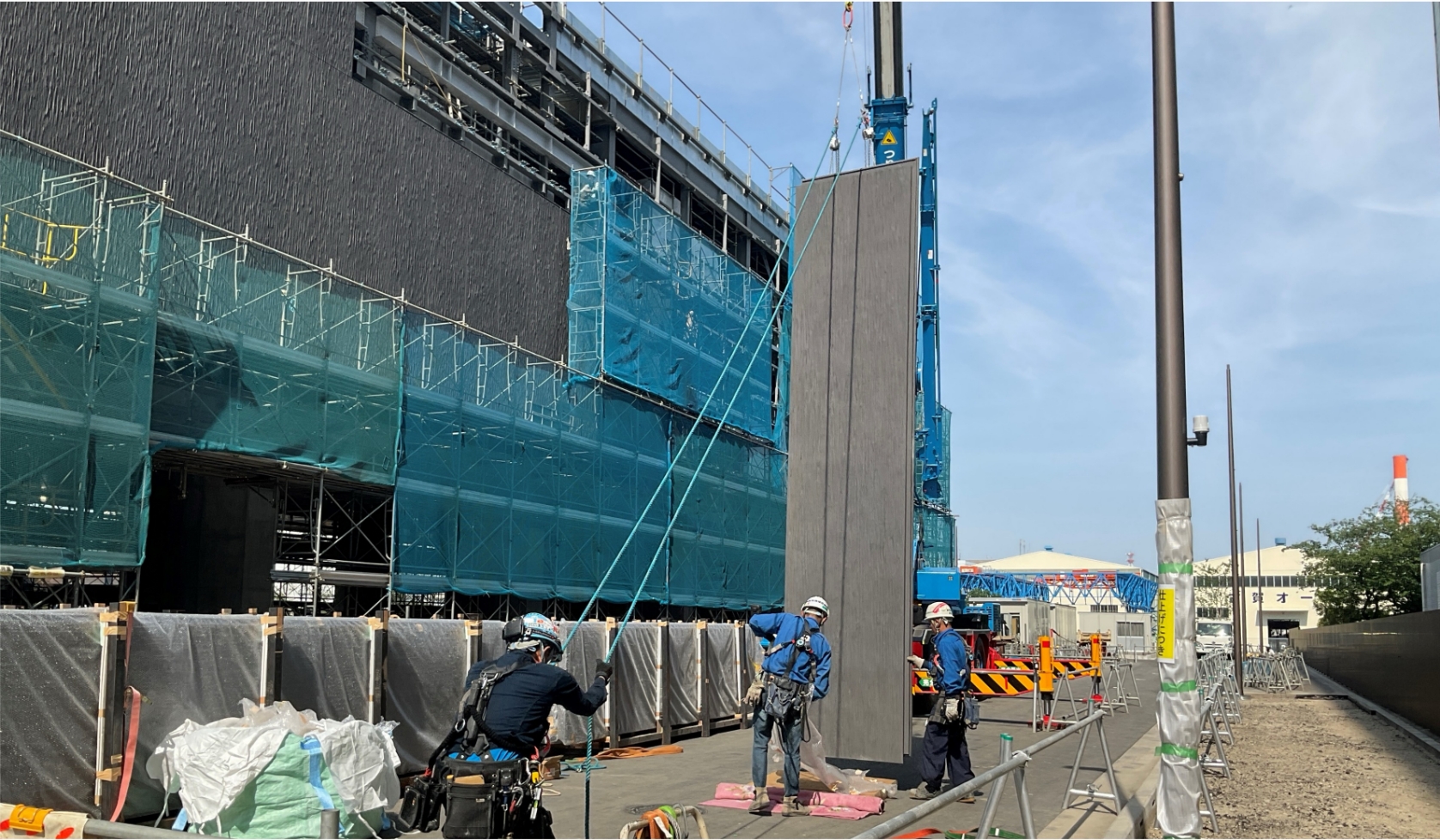
Panel construction work. Each panel is 1.2 meters wide and 5.5 meters tall.
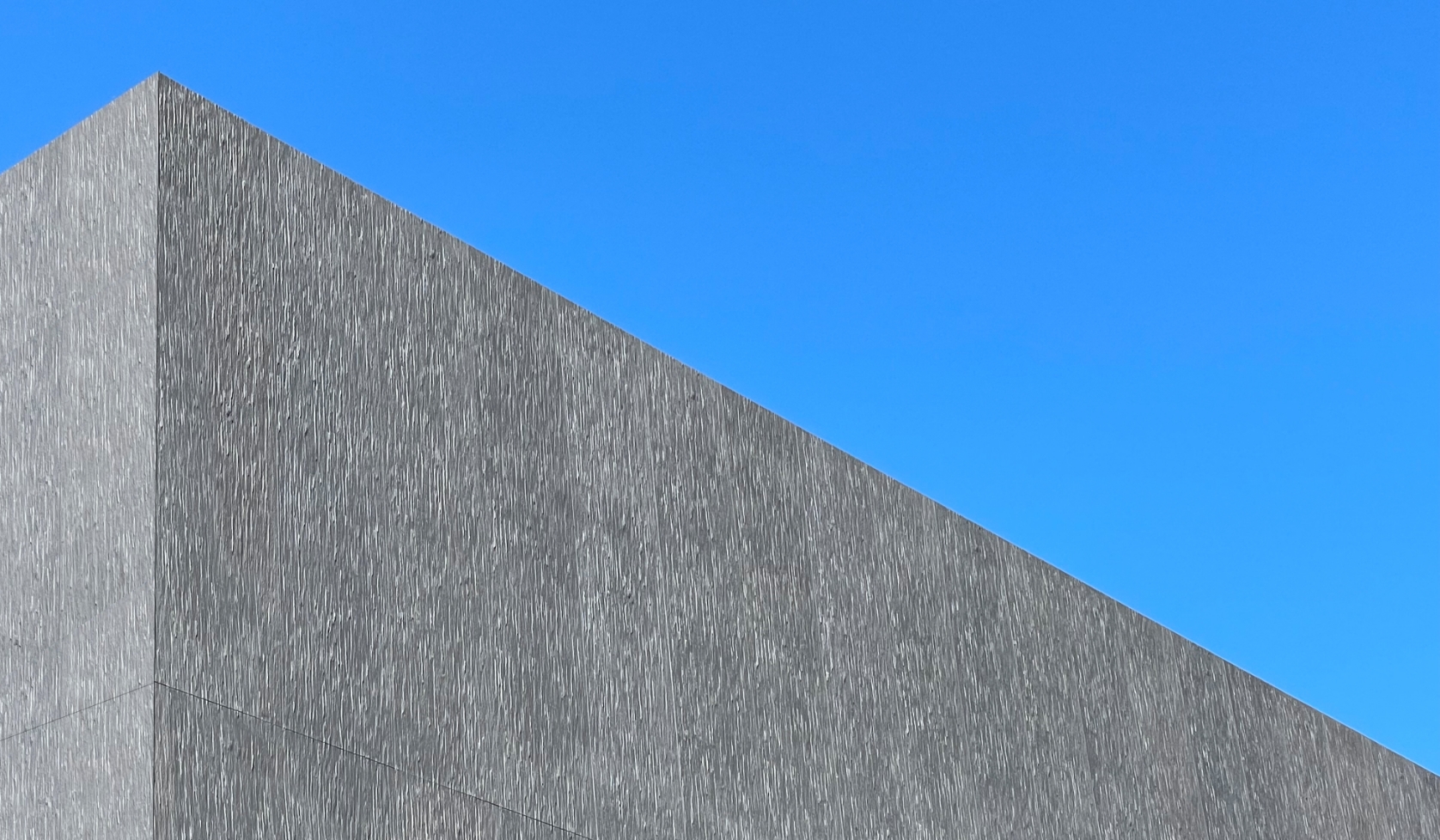
The panels look different depending on the angle of the sun, and the seams are invisible on the actual panels, just as they were in VR.
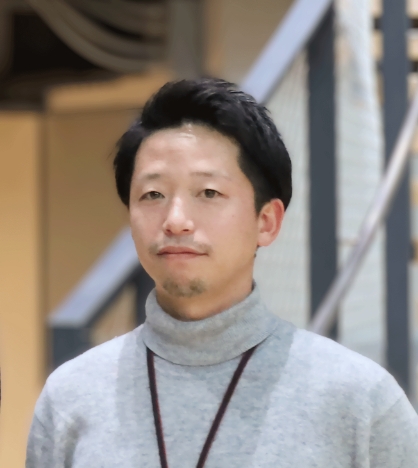
Architectural design
Takashi Kimba
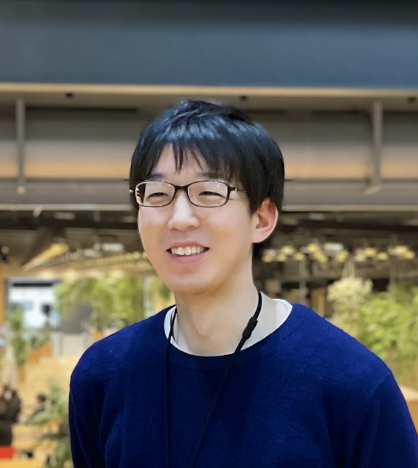
Structural design
Ryuta Hasegawa
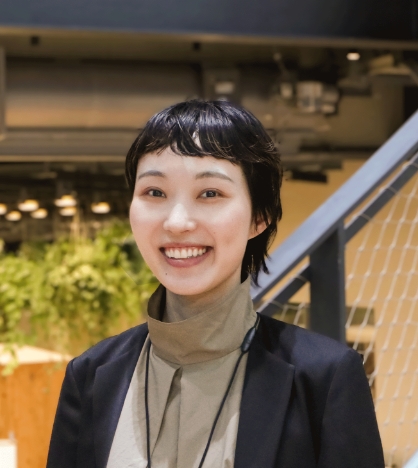
Computational design
Moe Takeuchi
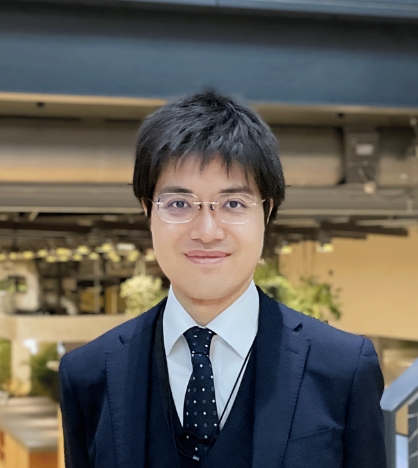
Computational design
Satoshi Oe
We took the thoughts of Kisuke Shimizu II that he put into the alcove posts and preserved them in a new design.
Combining the casting techniques of a craftsman and generative AI, we also replicated the thoughts behind the workmanship rather than making a simple copy. We feel that we’ve shown how the latest technologies, such as generative AI and digital fabrication, can be harnessed to create a new value in the field of architecture instead of using them only to improve efficiency.
For this project, we set out to craft a design that honors the essence of our company’s DNA. In the future, we hope to elevate this concept further by tailoring custom designs that reflect the unique origin stories cherished by each client, thereby creating architecture that resonates deeply with them.