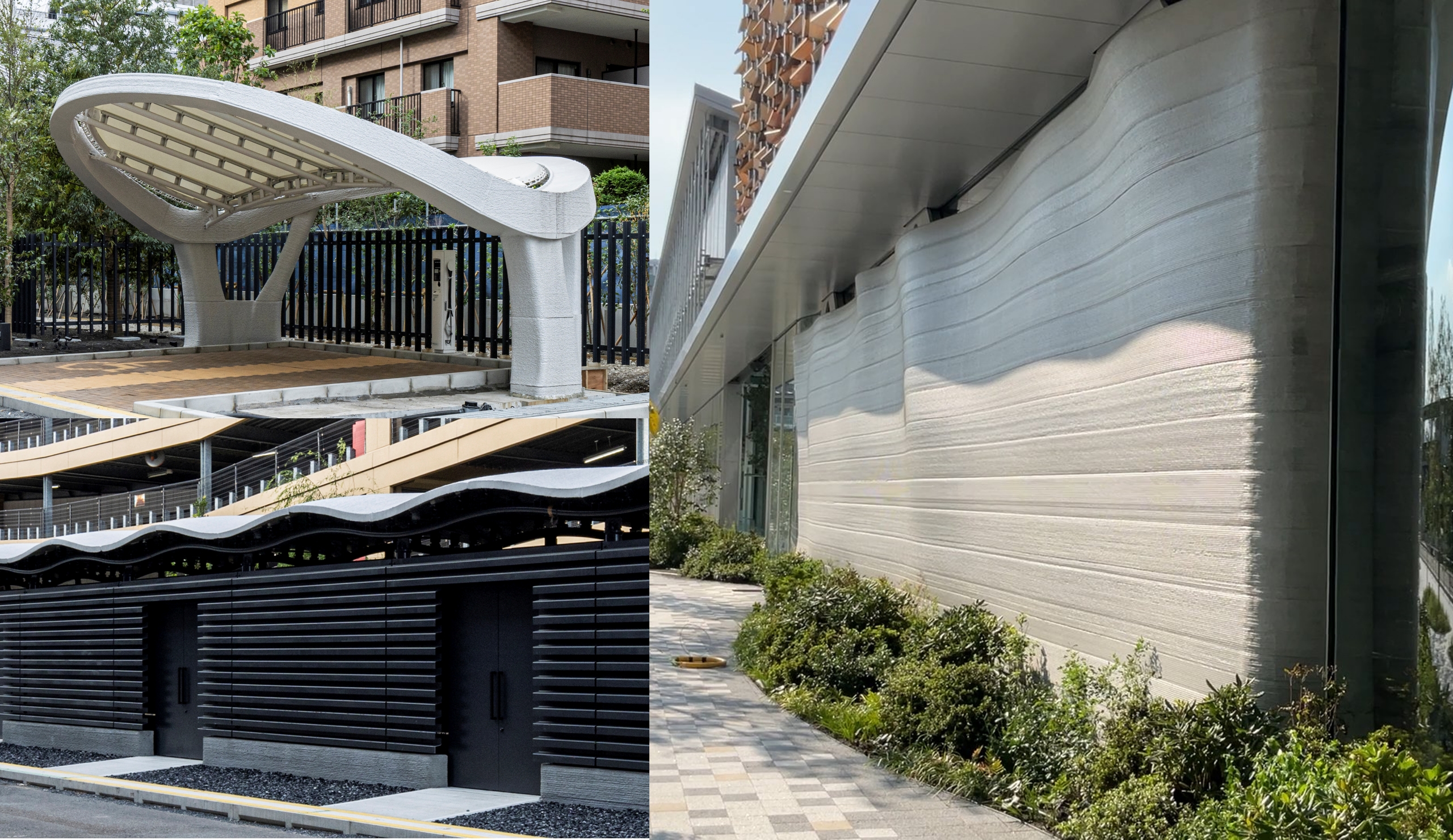
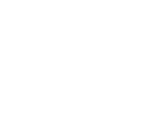
温故創新の森 NOVARE
-3Dプリンタで未来のものづくり-
次世代の創新を生む、新たなプラットフォーム─NOVARE─
江東区潮見に誕生した、オープンイノベーション拠点「NOVARE(ノヴァーレ)」。ラテン語で「創作する、新しくする」を意味するこの施設は、清水建設が国内外の知を結集し、新たなイノベーションを創出する場を目指しています。5つの施設が自立・連携し、 大自然の中で「森」が生態系(Ecosystem)を形成するように、ものづくりの原点に立ち返ります。
- 計画地
- : 東京都江東区潮見
- 敷地面積
- : 32,233.97㎡
- 段階
- :竣工(2023年)
省人化・省マテリアル・低環境負荷の新しいプロセスで、
未来のものづくりに挑戦
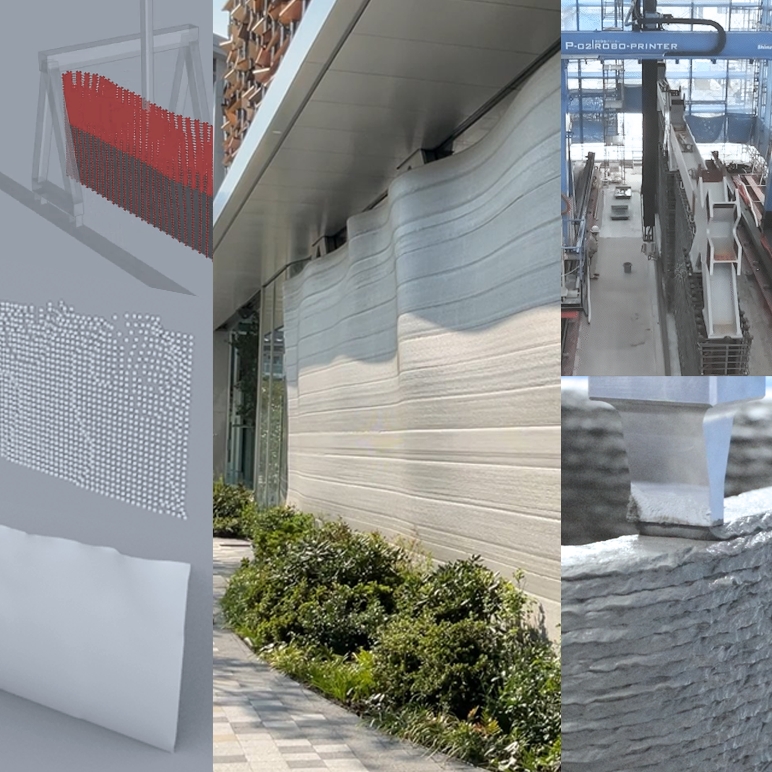
当社は2023年11月に創業220年を迎えました。その長きにわたる歴史の中で培われた知識、技術、人財のDNAを受け継ぎ、新たなイノベーションに繋げることがNOVAREの使命です。
NOVAREを構成する5つの施設はそれぞれ自立かつ連携しあい、国内外の知を結集し新たなイノベーションを創出する場となることを目指しています。つまり、さまざまな新しい技術を導入する、実証実験の場でもあるのです。
施設各所では現代の社会状況や環境に合わせて、省人化・省マテリアル・低環境負荷の新しいプロセスのものづくりに挑戦しました。3Dプリンタをそれぞれ違うかたちで活用した、3つの「未来のものづくり」の事例をご紹介します。
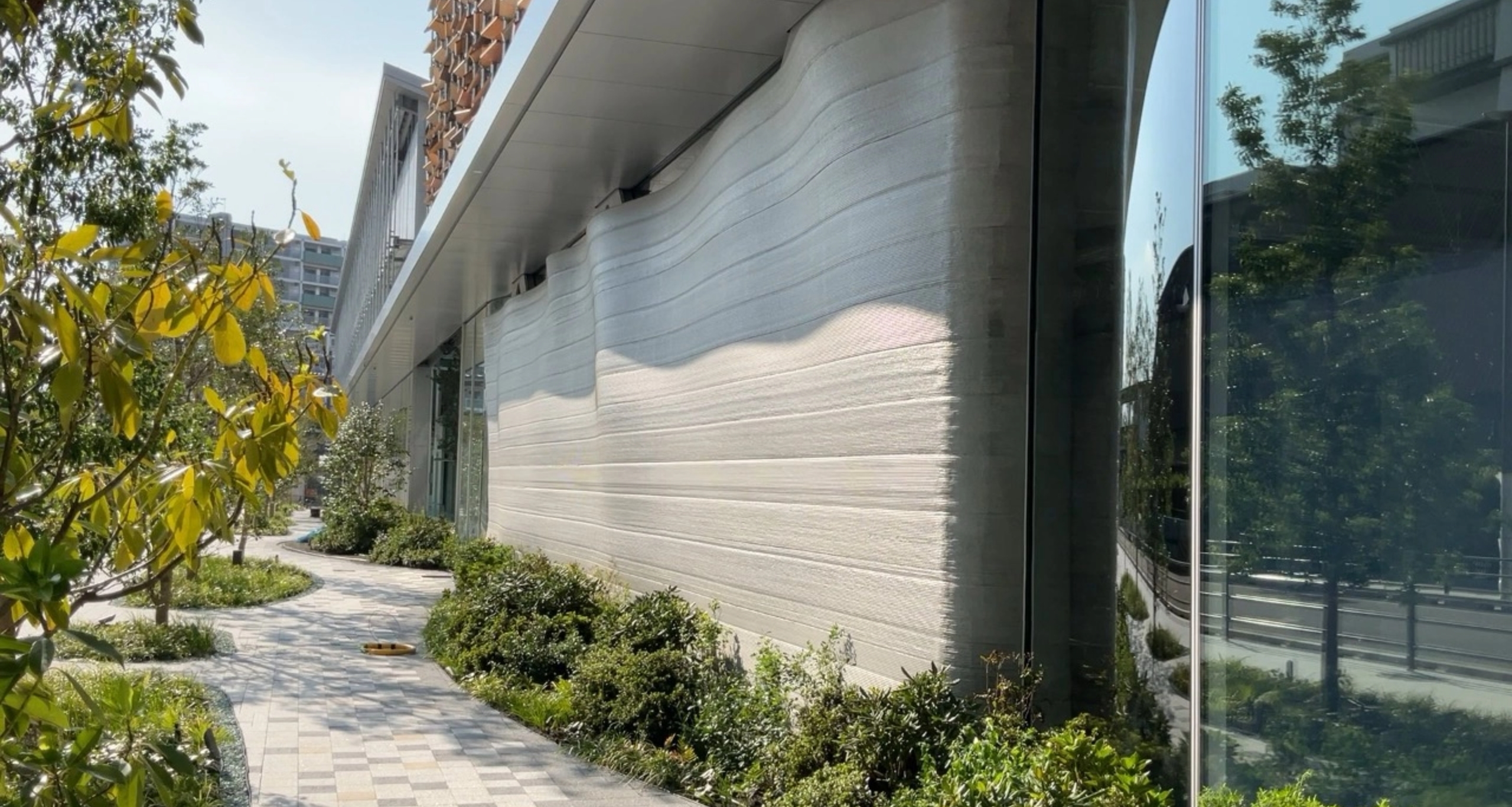
3Dプリンタを環境配慮型活用した 「3D曲面壁型枠」
3Dプリンタの特徴の一つが、自由形状を作りやすく、個別生産に強いという点です。この特性を活用して、環境配慮型の壁「3D曲面壁型枠」を作ることに挑戦しました。
まず、壁の厚みを決めるせん断力を算出するため、FEM解析により長期荷重と地震時の荷重に対する応力分布を生成しました(右図)。
その応力分布の画像データから厚み方向の量を決定し、構造的に不要な部分を取り除いた形状を生成していきます。必要なところだけを厚く、不必要なところを薄くすることでコンクリート量を1割削減することに成功しました(下図)。
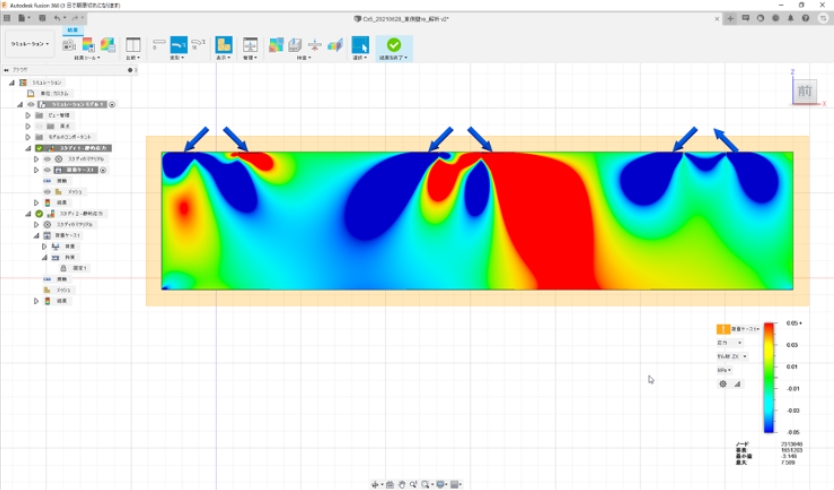
支配的になるせん断力の応力図。赤がプラス方向で青がマイナス方向、矢印部分はトラスの脚部の位置を示している
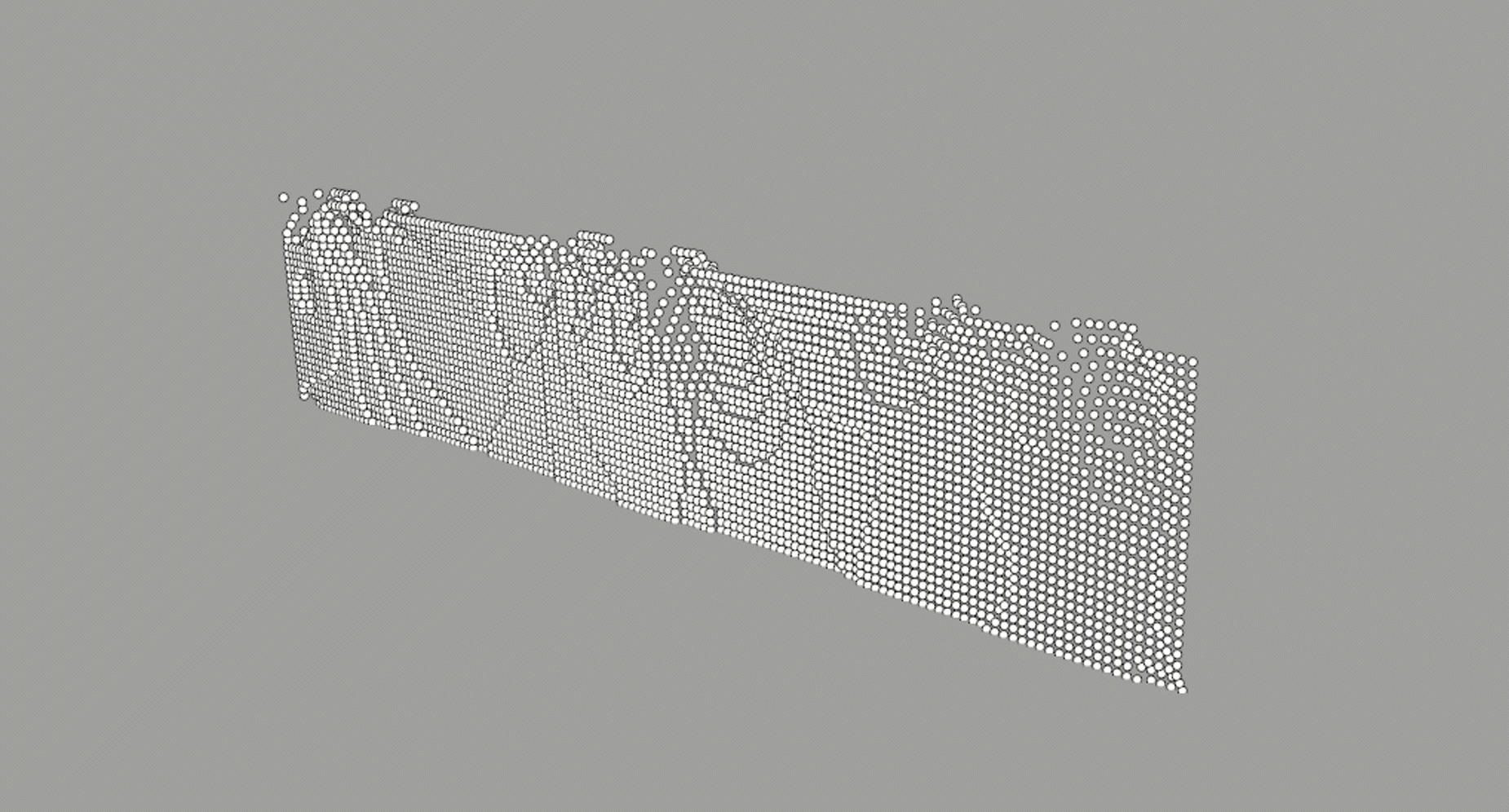
応力分布図を壁の厚みに変換。滑らかにしていくことで、最終的にコンクリート量を1割削減
3Dデータでプリントをシミュレーション
次にプリントのシミュレーションをGrasshopperで行います。これは、3Dデータを使い、プリントがどれくらいの期間でできるか、必要な材料はどれくらいかといった情報をデジタル上で検証するプロセスです。3Dプリントはデータを送れば完結するものではなく、機械を動かすプログラムを書き出す必要があります。今回はそのプログラムである”G-CODE”の書き出しまでもGrasshopper上で行い、設計・施工の連動を容易にすることを実現しました。
今回の壁は長さ20m、高さが4.5mもある巨大なものです。そこで、現地でそのままプリントする「オンサイトプリント」を実践しました。設計データをもとに現地で3Dプリントするデジタルファブリケーションは、当社としても初の試みです。作業は1日4〜5時間プリントし、2週間ほどで完成。気温に応じた材料の配合等、得られた様々な情報は今後の3Dプリンタ施工のための貴重なデータとして活かされます。

Grasshopper上でシミュレーションを行い、施工に必要な情報を一元管理
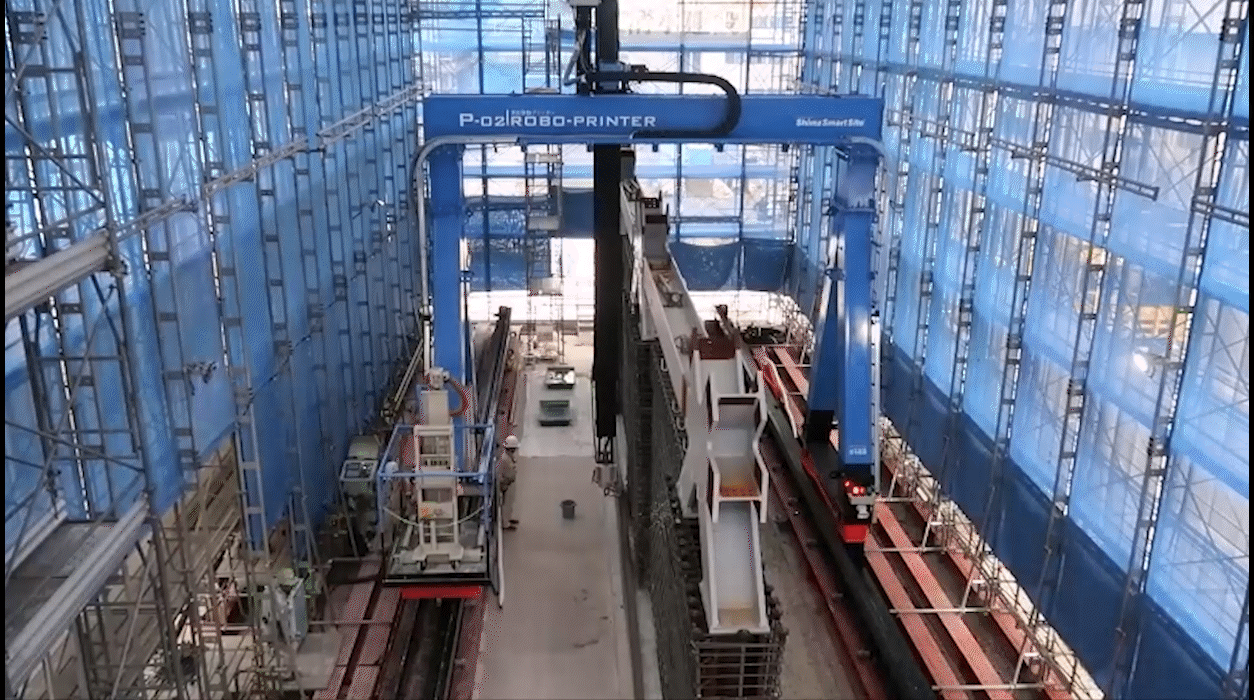
施工場所で実大構造物を直接印刷できる建設3Dプリンタ「Shimz Robo-Printer」。巨大なものも現地でシームレスにプリントできる
環境配慮型の材料で、CO2を60%削減
ここでは3Dプリンタのノズルに刷毛を付けてテクスチャを表現する自動左官も取り入れました。さまざまなスポンジや動物の毛を検討した結果、ヤギの毛を採用しています。結果、独特の波を打つような壁面となりました。
また、「3D曲面壁型枠」の内部には他社が開発した高炉スラグ粉末を多量に含む低炭素型コンクリート「ECMコンクリート」を使用しています。ECMコンクリートは高炉スラグ粉末を多量に含み中性化速度が一般的なコンクリートよりも早いため、外気に触れる場所への適用ができませんでした。しかし、3Dプリンタの素材が非常に緻密で水も空気も通さない材料のため、ECMコンクリートの長所を最大限活用することを可能にしました。CO2削減という社会課題に対応するため、競合他社製品と自社技術を掛け合わせるというオープンイノベーション施設ならではの新たな取り組みです。
形状としてもコンクリート量を削減、材料としても従来に比べCO2を6割削減し、型枠の廃棄もない、環境配慮型の壁を実現しています。
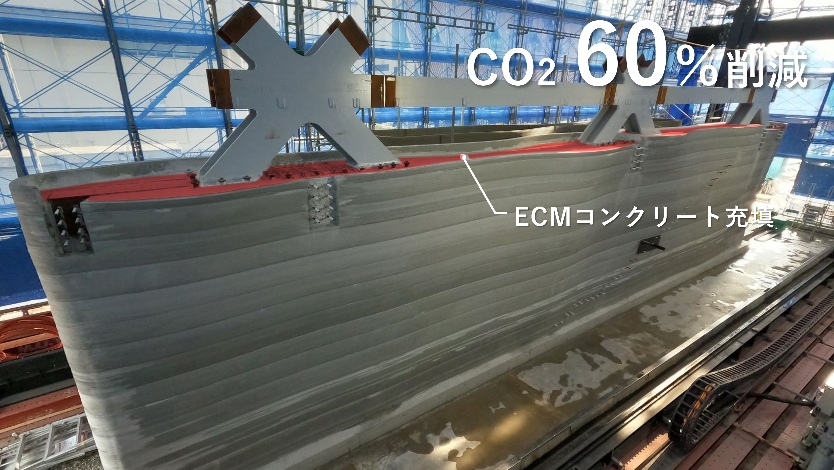
ECMコンクリートはセメントの60~70%を鉄鋼製造の副産物である高炉スラグ粉末に置き換えたコンクリート
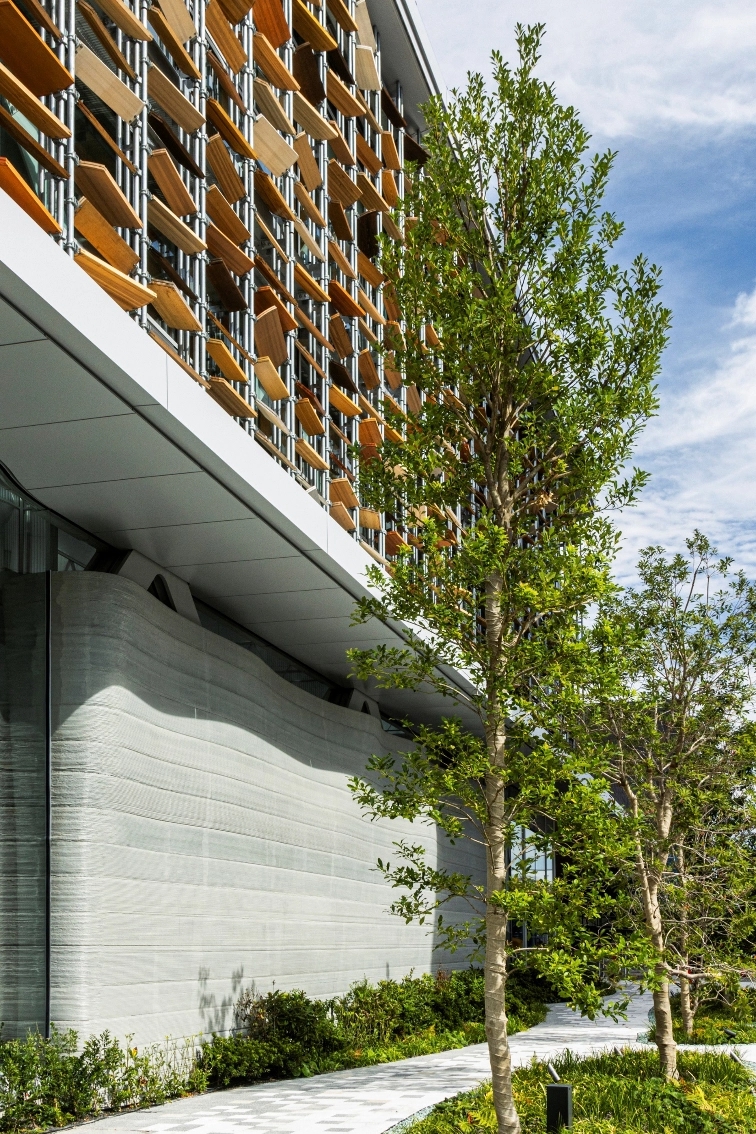
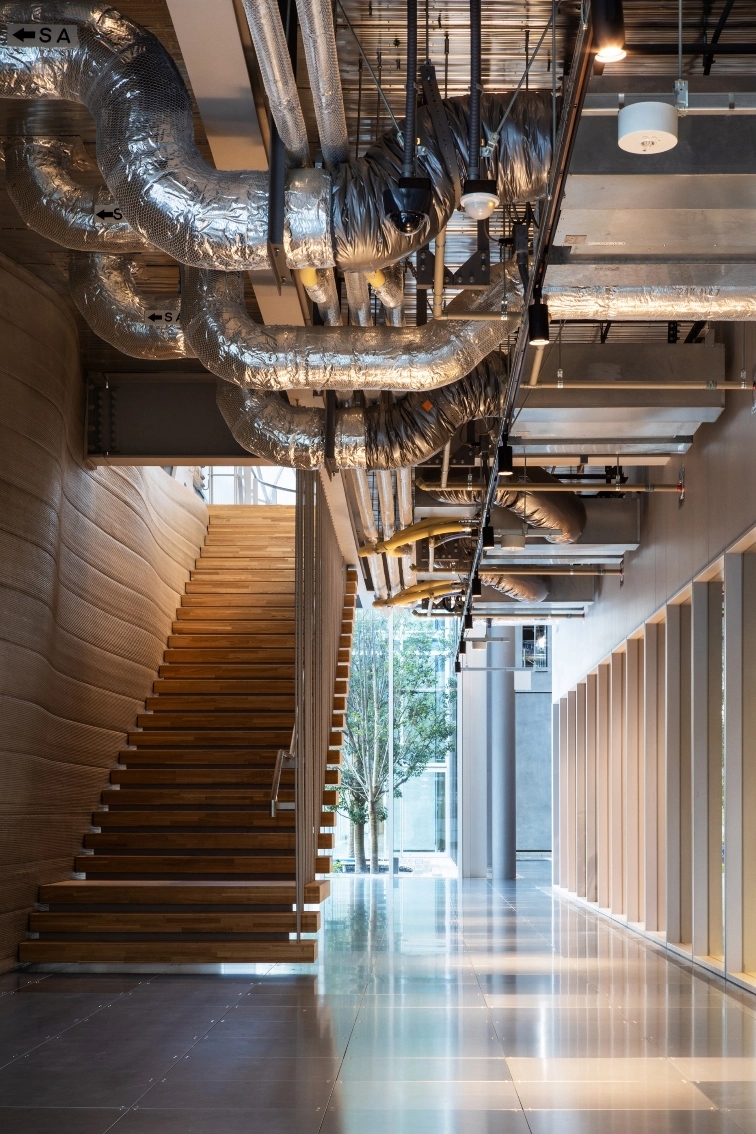
3D曲面壁の外観と内観。壁の曲面に沿って階段の幅をひとつひとつ調整してフィットするように設計している
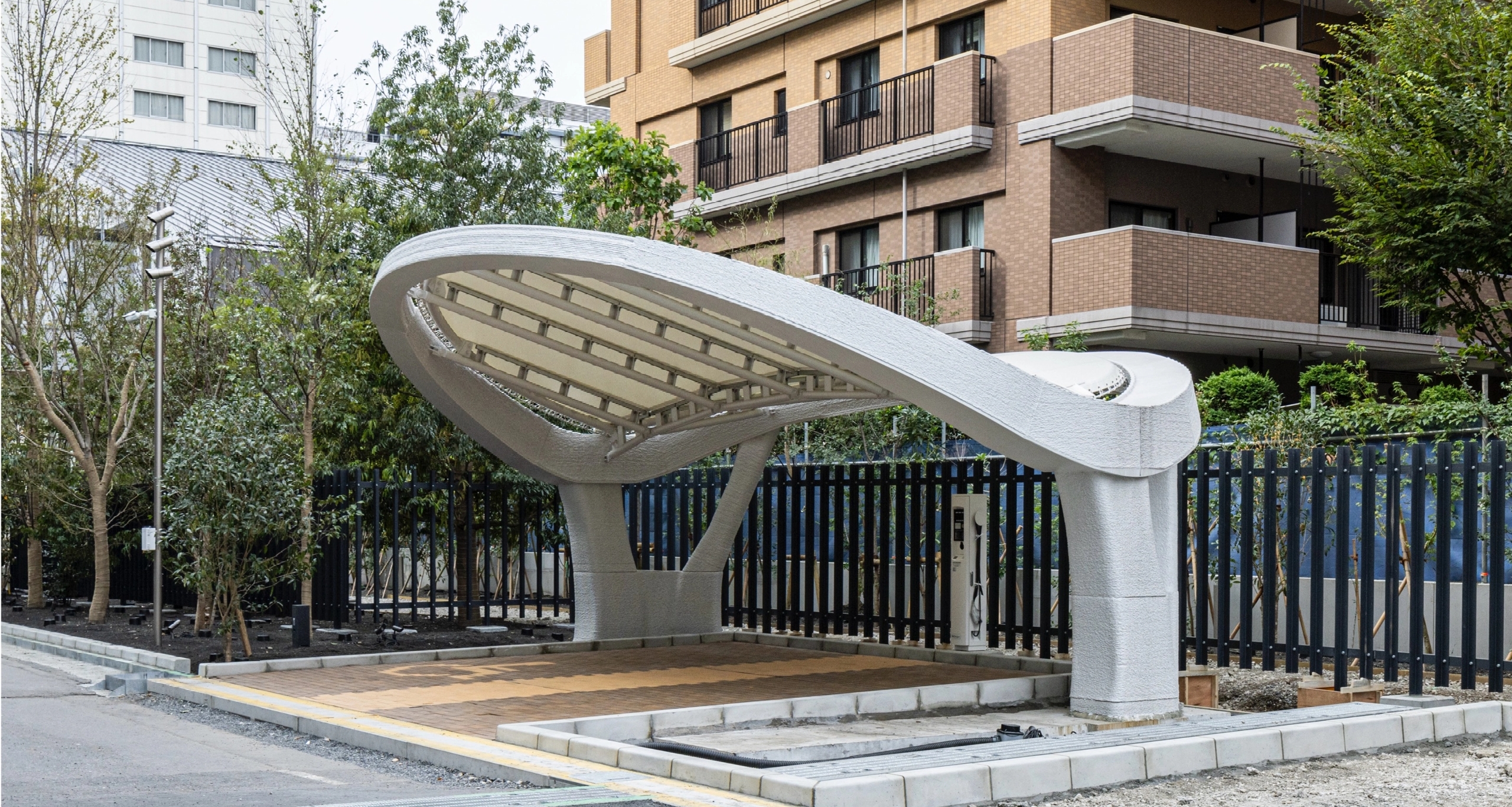
駐車場そのものを3Dプリンタで出力する 「構造体プリント」
構造体そのものを3Dプリンタで作った国内初の例
3Dプリンタの建設適用はまだ黎明期にあります。そこで、その可能性を広げるため、型枠ではなく建物の骨格になる構造体をプリントすることに挑戦しました。
構造体そのものを3Dプリンタで作ることとは、下図の中央と右図のような方法を意味しています。構造体にするメリットとしては、3Dプリントした部分も含めて構造体として活用することで、使用材料も少なくなり、環境負荷低減や意匠性の向上が期待できることが挙げられます。また、設計データから直接構造体をプリントすることで、施工図、製作図の作成、コンクリート打設といった手順を省略することが可能となります。そのため、本プロジェクトと並行してコンクリートとして打設可能な3Dプリンタ用材料「ラクツムS」の開発を行い、大臣認定を取得しました。これは国内では初の試みです。
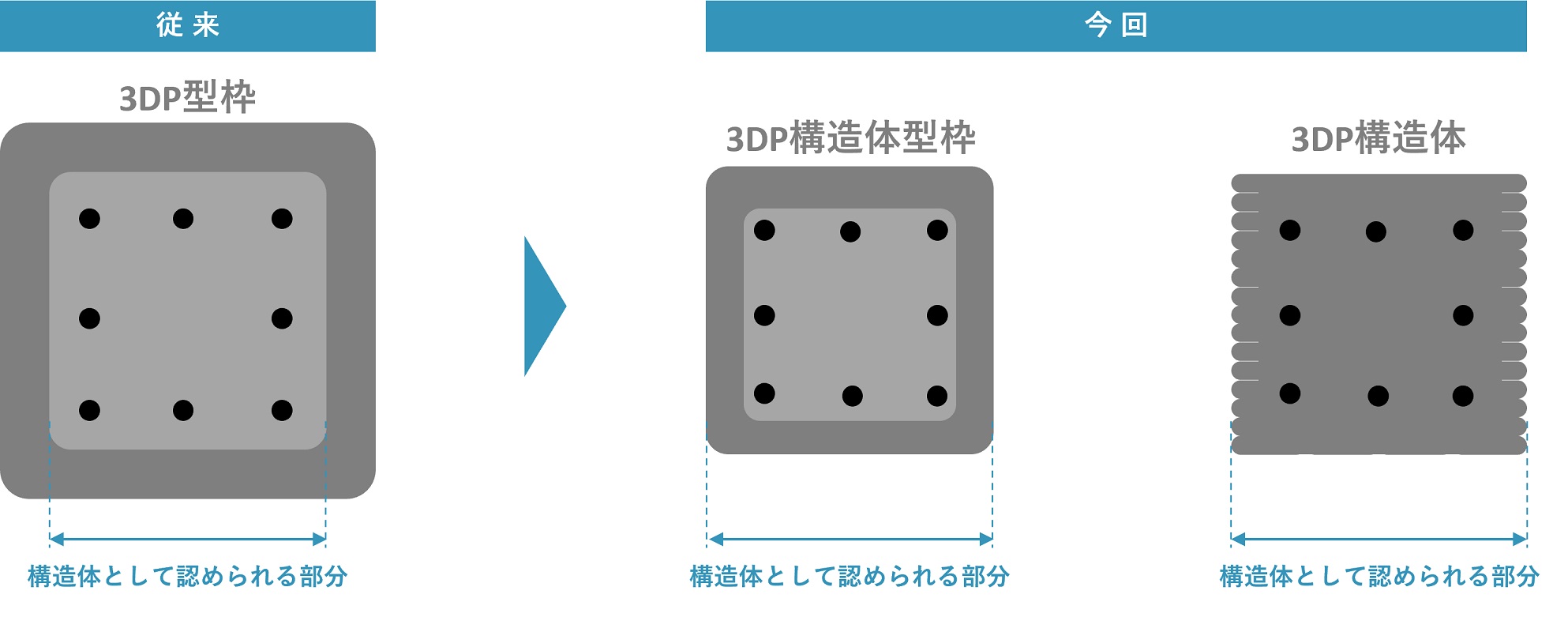
左:濃いグレー部分を3Dプリンタで作る従来の活用例。構造体として認められる部分は、薄いグレー部分のみ
中央:濃いグレー部分も構造体として認められる、3Dプリンタ構造体型枠
右:3Dプリントを行い、中に鉄筋を置くという方法で作る3Dプリンタ構造体
建物の形状に対して最適な架構を三次元的にデザイン
駐車場のデザインは圧縮形材料であるコンクリートの特徴を活かして、2つのアーチを取り入れた造形としました。長期荷重は基本的に2台のRC柱で支え、控え柱により安定性を向上しています。意匠及び構造上細くしたい部分のアーチ先端と控え柱に、構造体算入可能なラクツムSを適用しています。
データをそのままプリントできるのが3Dプリンタの大きな利点のため、複雑な形状も作りやすいのが特徴です。2つのアーチを取り入れたデザインを検討するため、さまざまなデザインスタディを行い、最終案に絞り込んでいきました。
また、構造体とする箇所や施工順序も考慮して、全体を14パーツに分けてデータを作成しました。入力したデータをそのまま出力するデジタルファブリケーションならではのデータ構築です。

幾何学的に複雑な造形を三次元的にスタディして、さまざまなパターンを検討
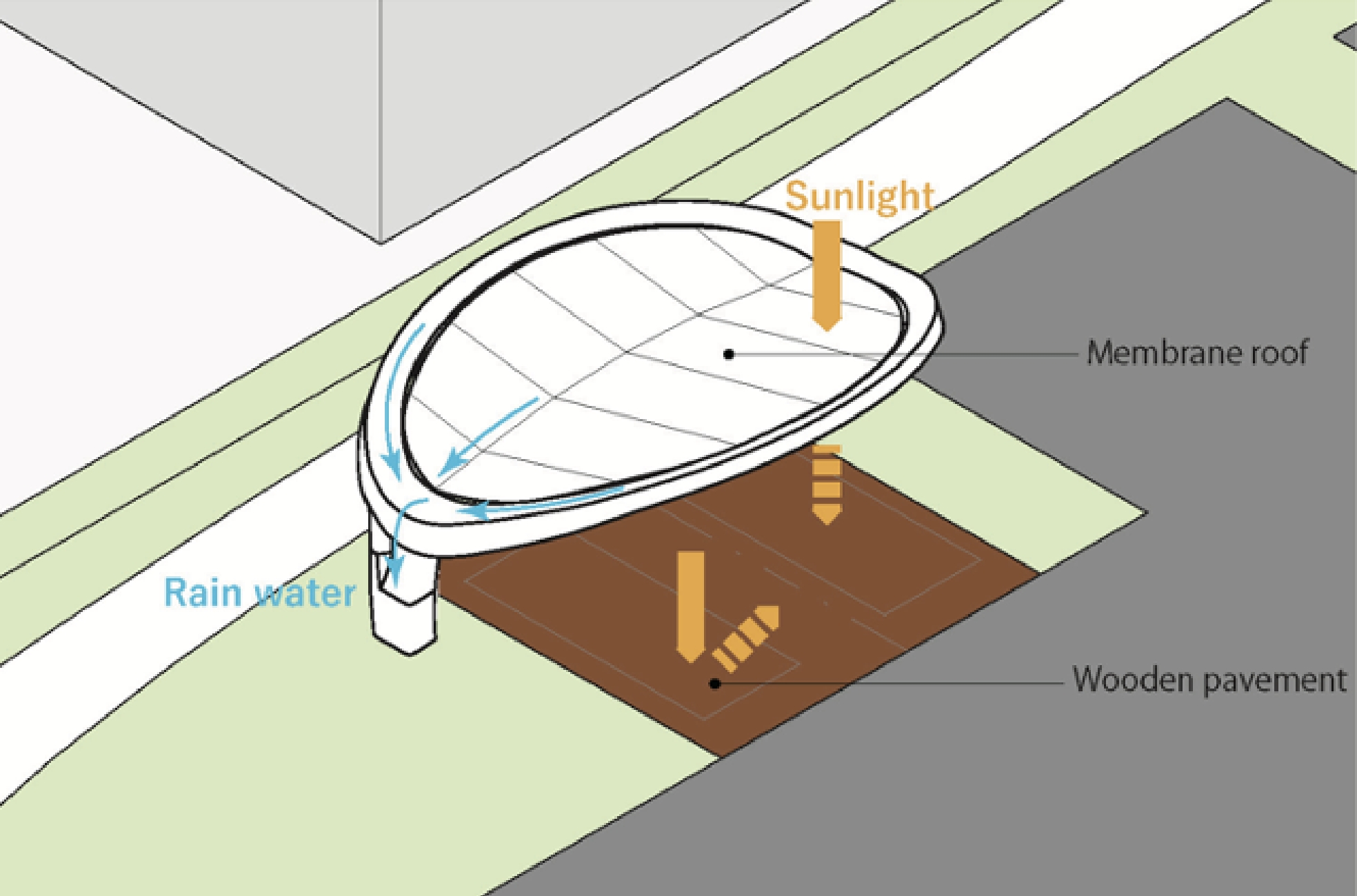
日射をさえぎり、屋根の2箇所に雨水を集めて水が流れる合理的なデザイン。舗装は熱を吸収しない木質レンガ
3Dデータを活用し、テスト・プリント・検証
デザインをプリントするにあたり、徐々に変化する部材の断面が課題になりました。そこで、断面形状はプリントの吐出量とプリントスピードで調整し、断面変化量に対する最適なプリント列数を検討しました。
テストプリントを繰り返し、プリント結果に応じてデータを修正、プリントパスを決定するプロセスを導入。テストプリントをすることにより、データも蓄積されていったのです。
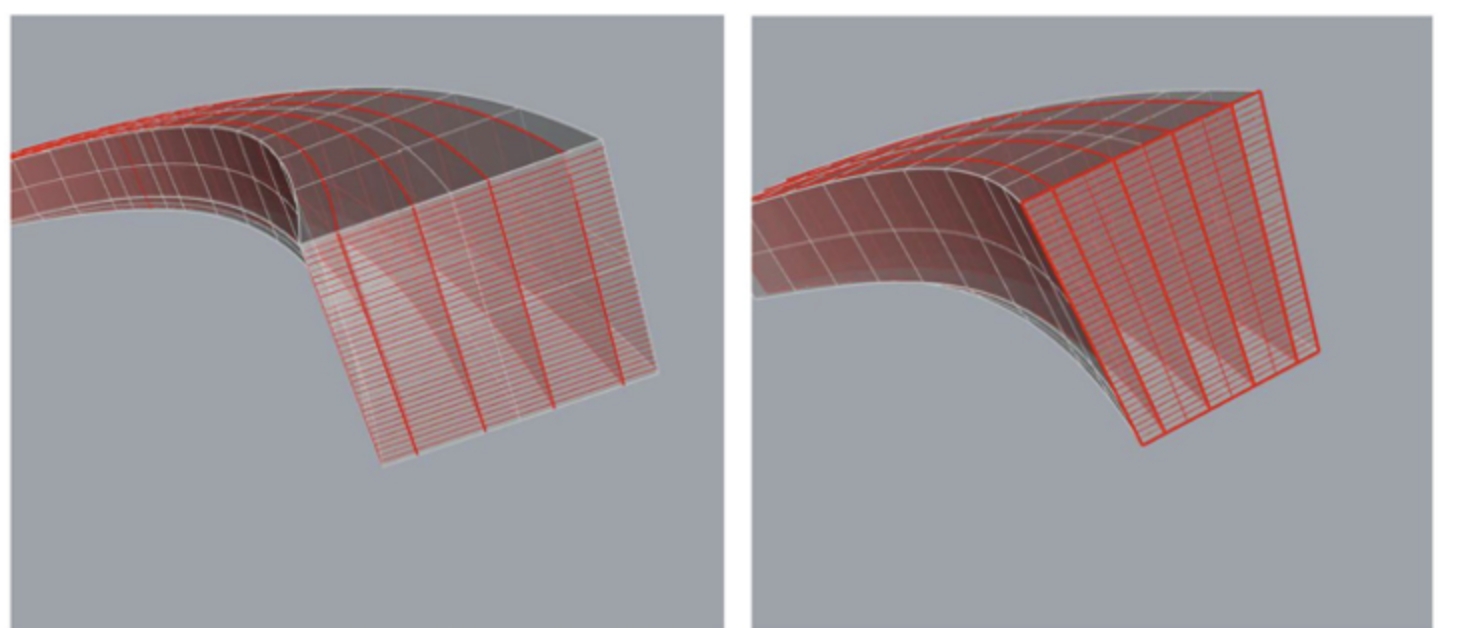
テスト結果を3Dモデルに反映し、プリントパスを決定していった

鉄筋を置いた上にロボットアーム型3Dプリンタでプリントして部材を制作していった
また、3Dプリンタで実際に出力していく際には、3Dデータをプリントする現場の管理が欠かせません。そのためには管理していくポイントが必要のため、3Dデータから抽出していきました。
できあがった部材は3Dスキャンをしてモデルと重ね合わせ、実際に設計した通りのデータになっているかを確認します。プリントされた部材の精度や、データと数値の誤差がないかなど、品質管理上のポイントを確認していきました。
これまで主に型枠材の置き換えに留まっていた3Dプリンタの活用方法ではなく、構造活用を踏まえた駐車場となりました。ロボットで建物をすべて作るという近未来に向け、第一歩となったプロジェクトと言えます。
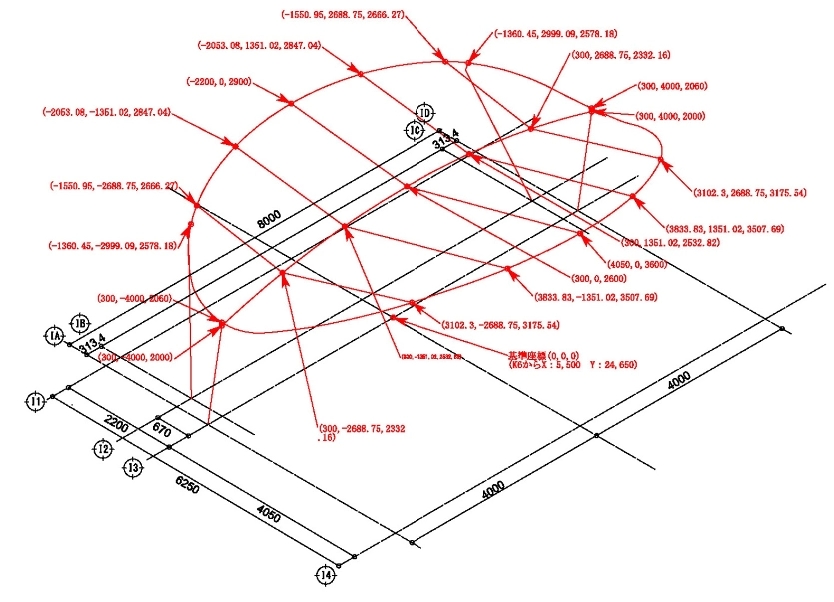
3Dデータから抽出したプリント上の管理ポイント
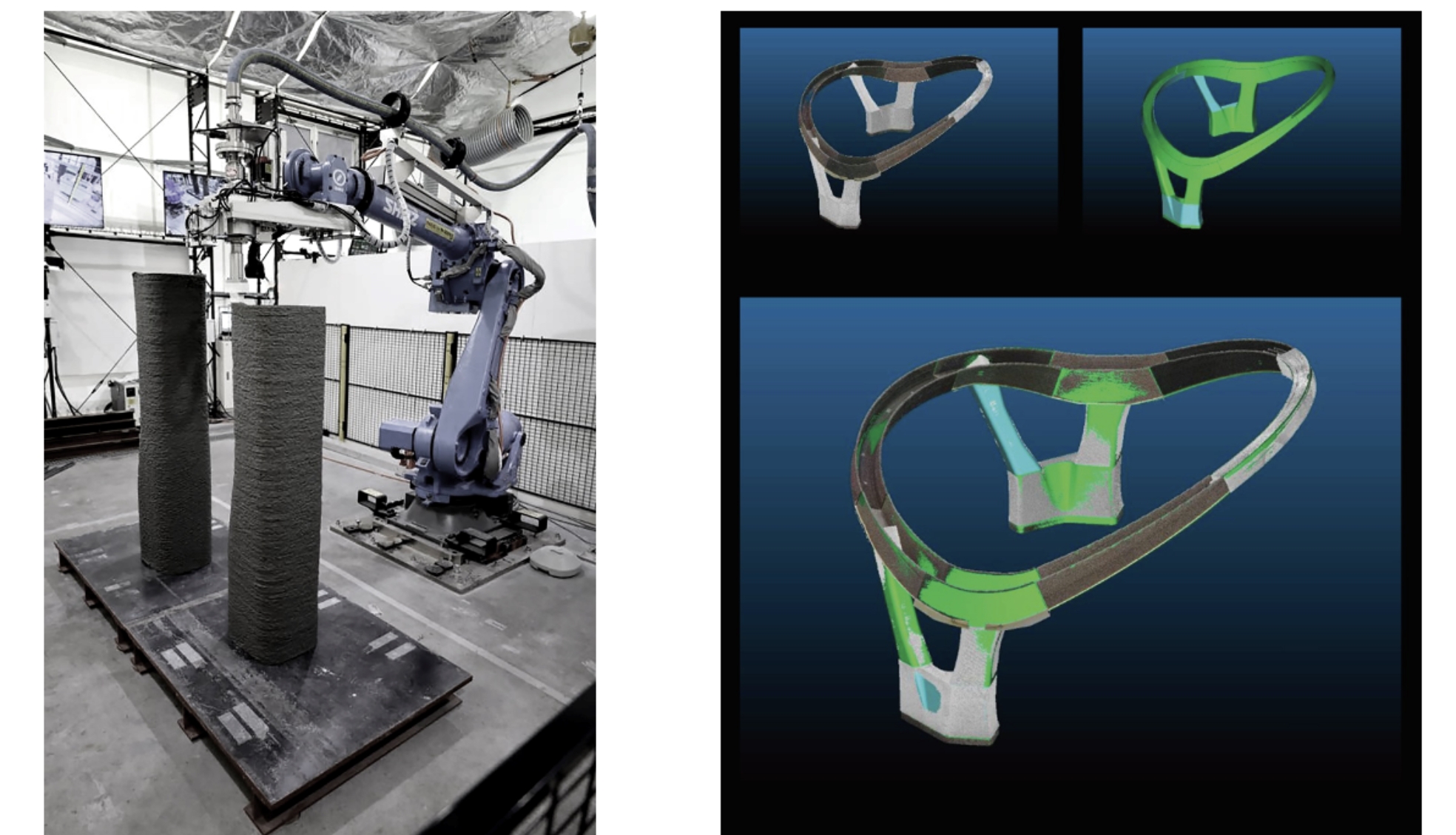
プリントされた部材を3Dスキャンしモデルと重ね合わせて検証
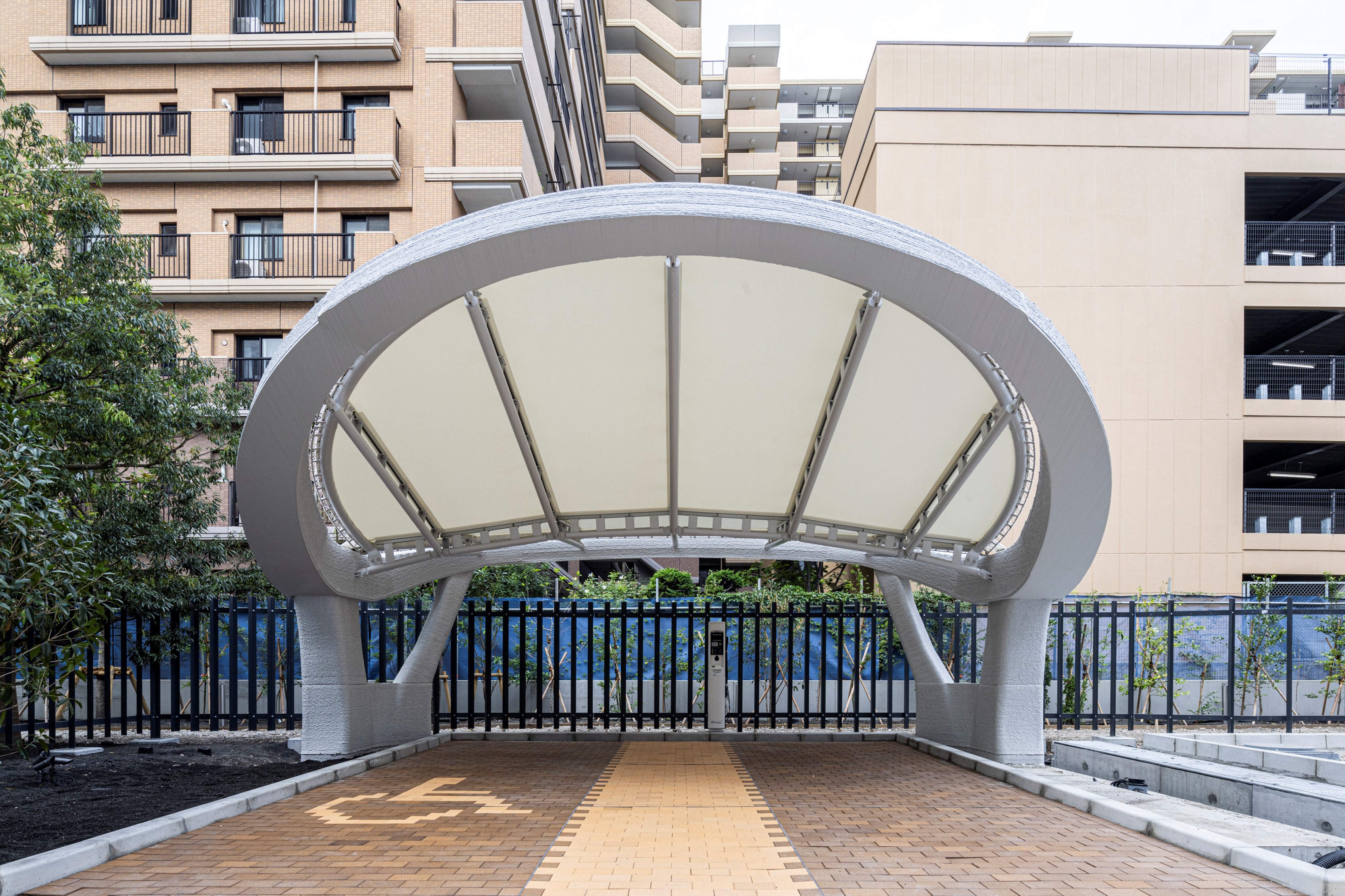
駐車場の正面。右側が電気自動車用で、左側が障がい者用の駐車スペース
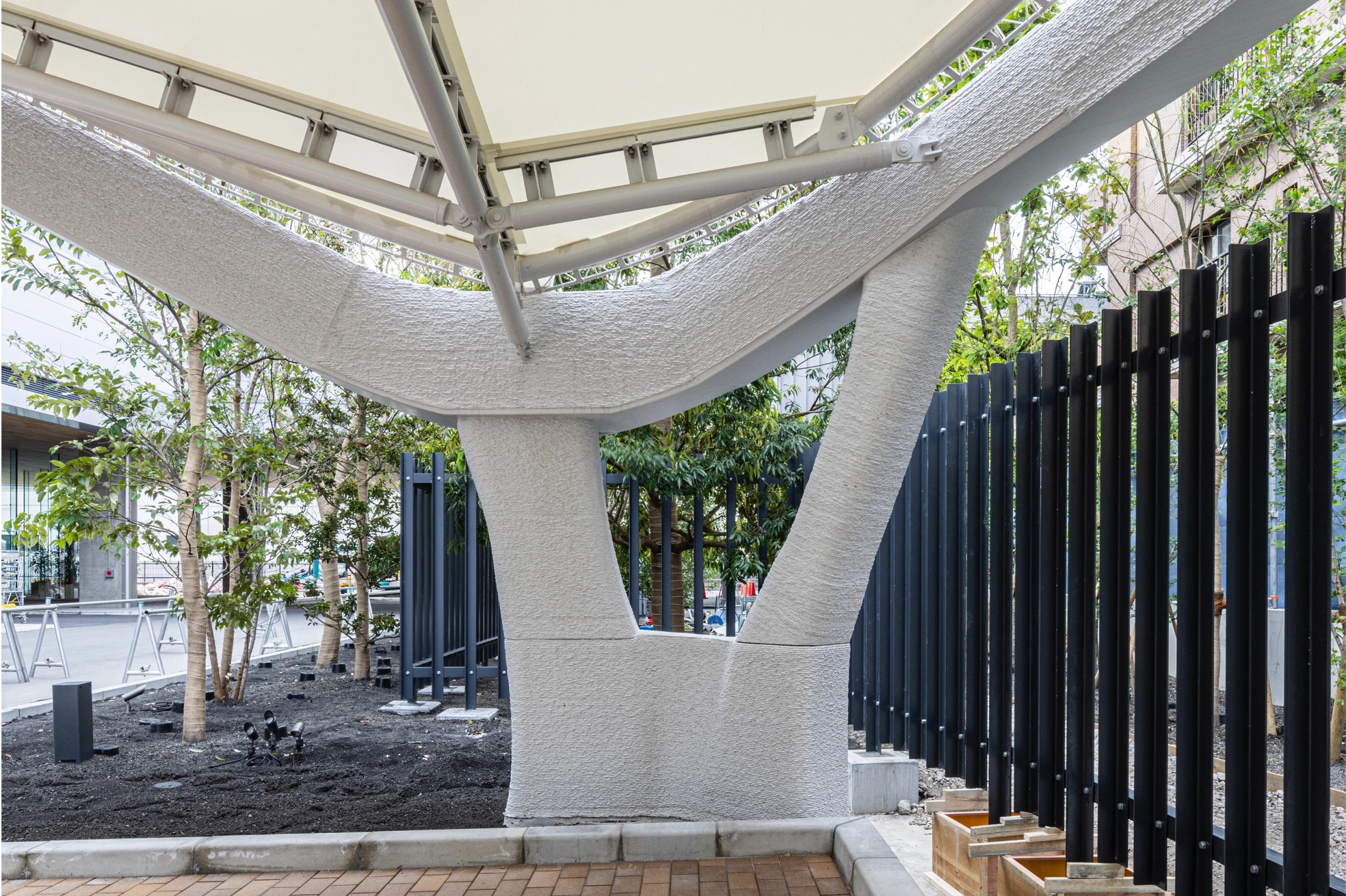
部材の表面は高さ7mmにこだわったきめ細かい意匠になっている
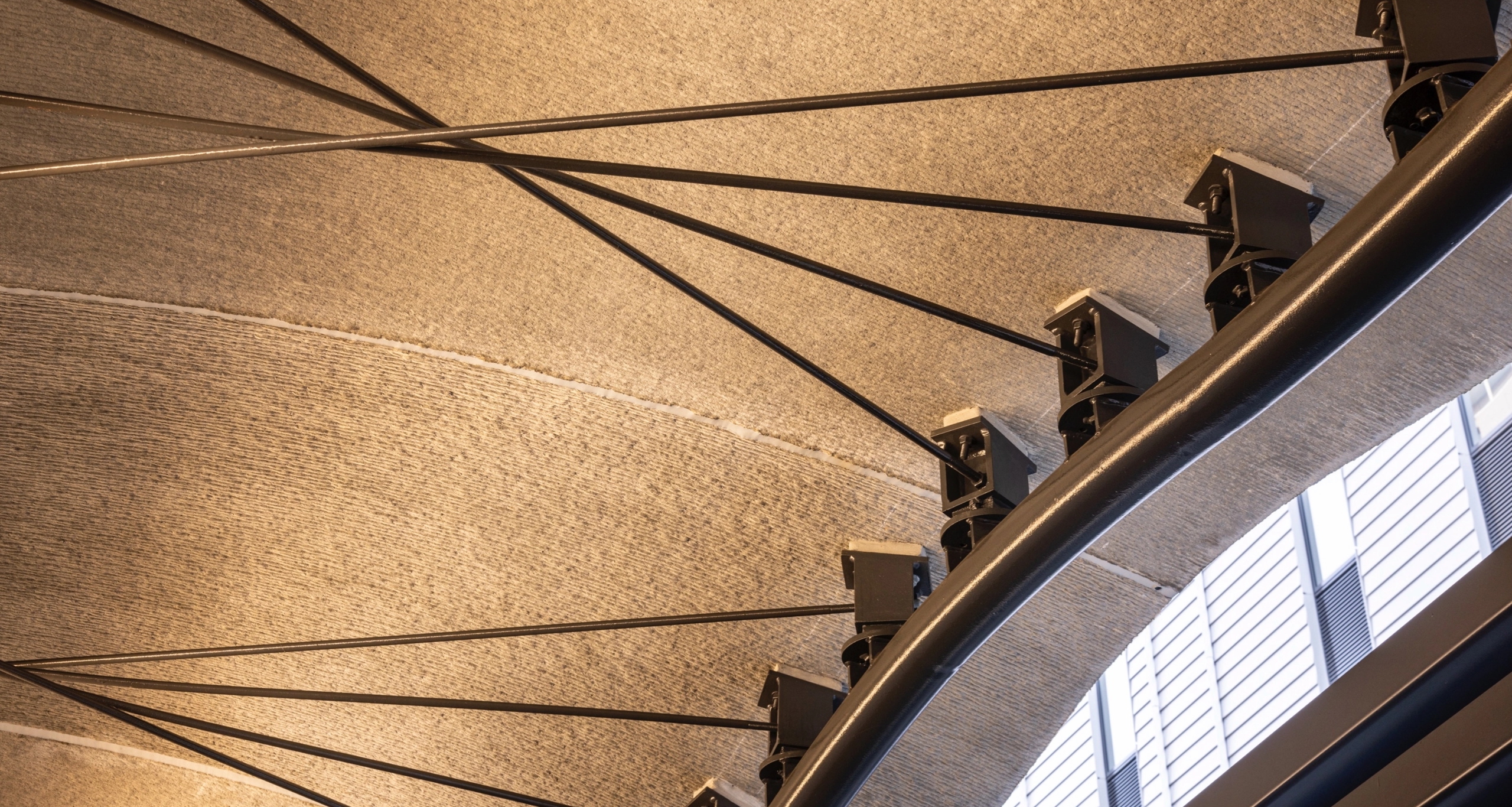
3次元の波打つ屋根を実現した 「シェル構造プリント」
構造だけの建物をデザイン
さらなる3Dプリンタの活用方法として、シェル構造のプリントに挑戦しました。具体的には、外装仕上げ材(屋根ふき材)の無筋プリントです。
半屋外の構造だけの建物に、構造材のデザインを検証するところからプロジェクトはスタート。まず、三次元の曲面と屋根の組み合わせを考えたとき、波打つような屋根がアイデアとして生まれました。そこで、長辺方向の梁を半位相ずらしたサインカーブにし、それによって平面に交差するロッドと三次元曲面を持つ屋根を考えました。
そして、水平方向の伸びやかさを保つため、屋根のライズを抑えました。長期荷重に対して発生する応力を、交差するロッドに張力を導入することでキャンセルさせ、力学的に自己つり合いさせた架構としました。
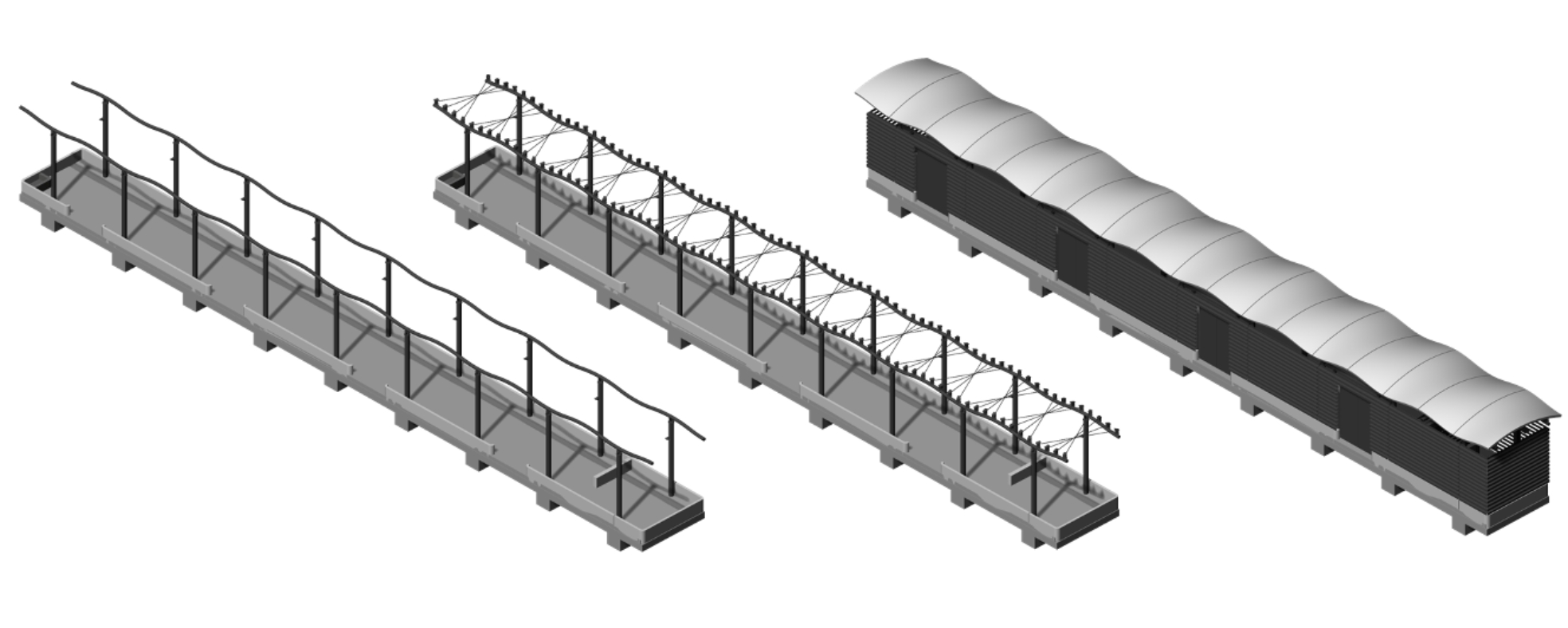
三次元の屋根自体は無筋で、屋根下部のロッドがスラスト力を保持している
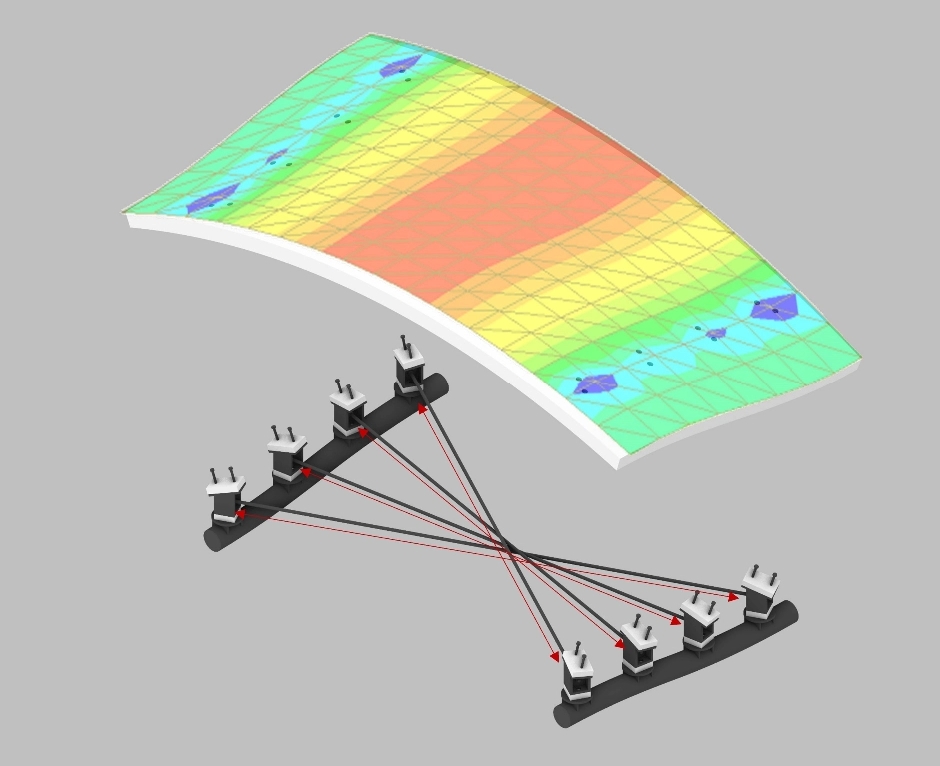
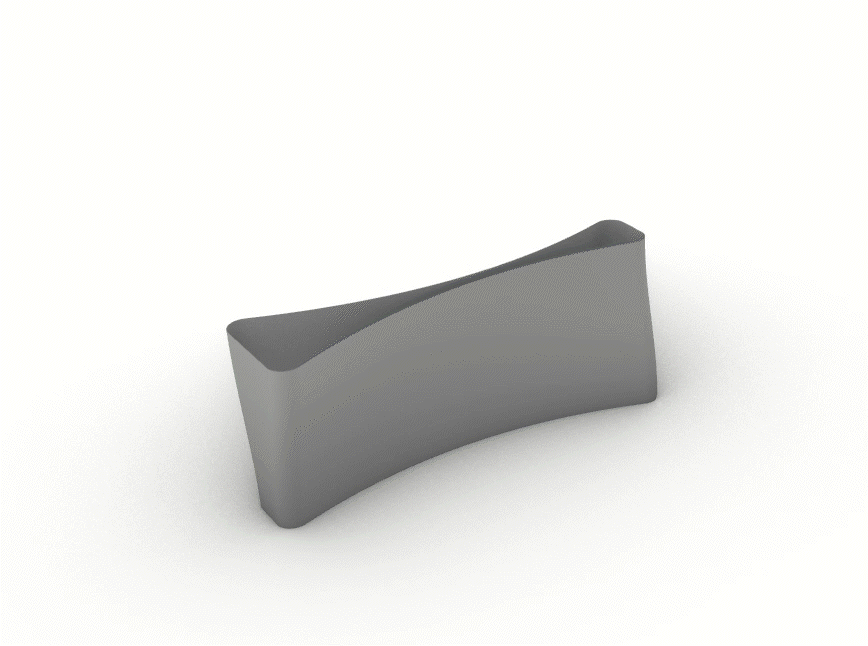
自立したパネルはプリントが難しいため一筆書き形状に調整したモデルを作成。赤い部分は後でカットして屋根を作っていく
ディテールをデジタルで作る
次に屋根に取り付けるボルトや金物の角度や位置など、ディテールを作成していく必要がありました。しかし、三次元曲面のため、場所によって角度や位置は異なってきます。どのように現場に伝えるかが課題となりました。そこで、今回はGrasshopper上で金物の角度などを自動算出し、ディテールをすべてデジタル上で作成していったのです。
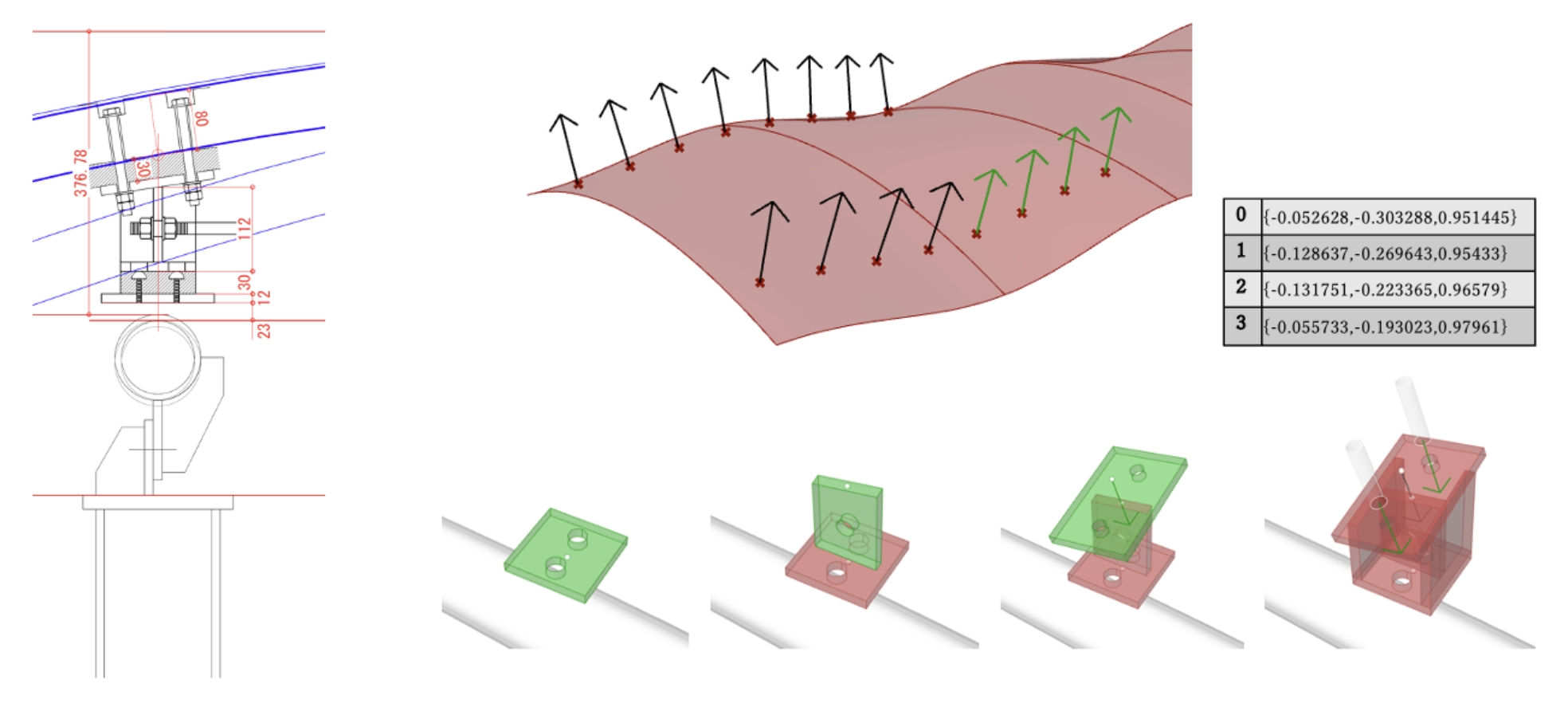
金物は8種類あり、角度などをGrasshopperでルール化していった
3Dプリンタの新たな活用方法を構築
施工にかかわる全員にとって、今回が初めてとなる試みが多く、そのため実際の3Dプリント作業にはさまざまな課題が生じました。同じ形でも日が違ったらプリントが再現されない、気温や湿度に左右されやすいなど、3Dプリントによる施工には、特有の難しさがあります。特に今回は冬場にプリントを行ったため、ヒーターで温めながらプリントするなど、設計者と施工者が協力しながら試行錯誤を進め、課題をひとつひとつ克服していきました。
このようにNOVAREでは3Dプリントを様々に活用しています。一方でサプライチェーンや法規制面での課題は残されています。NOVAREで3Dプリンタに取り組んだメンバーでは、社会普及に向け引続きそのような課題を解決していこうとしています。

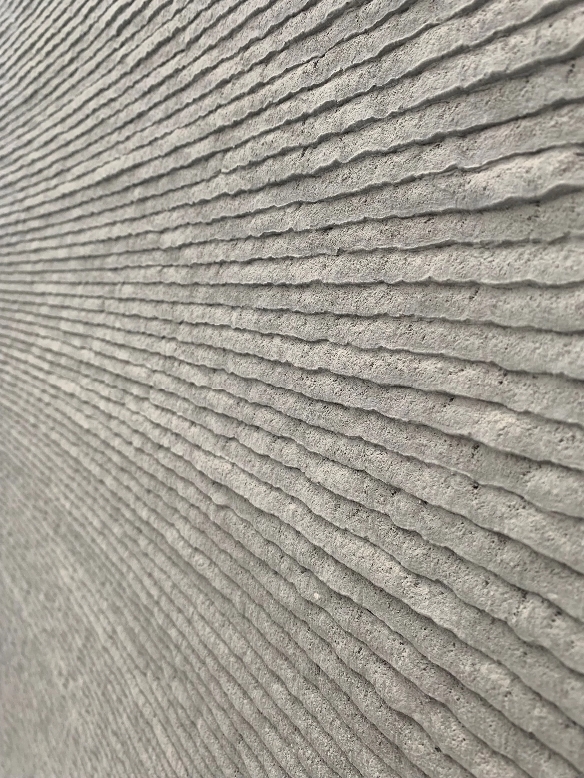
左:ヒーターで温めながら行った実際のプリントの様子。右:表面の加工。刷毛は使わずに美しく仕上がった
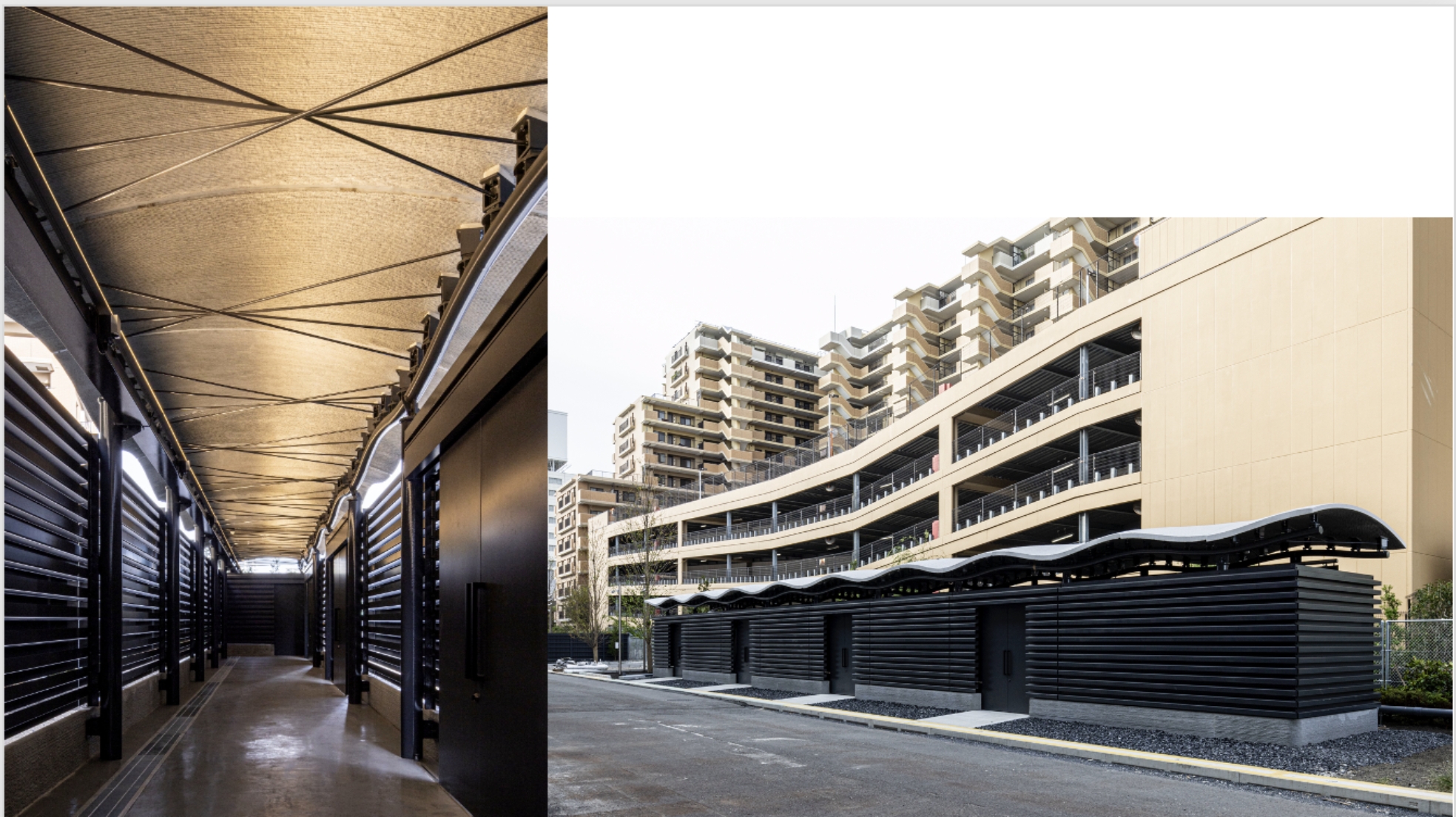
照明に照らされた建物内部。普段はNOVARE内の再利用保管庫として使用されている
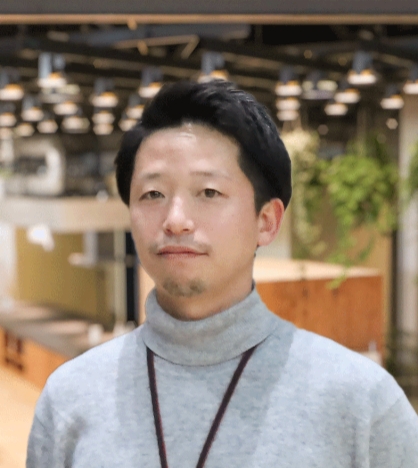
意匠設計
金馬 貴之
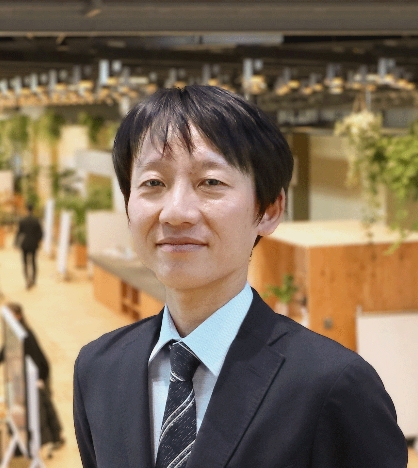
構造設計
田中 初太郎
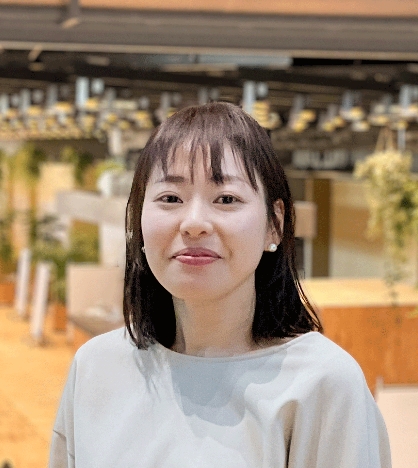
構造設計
山下 美帆
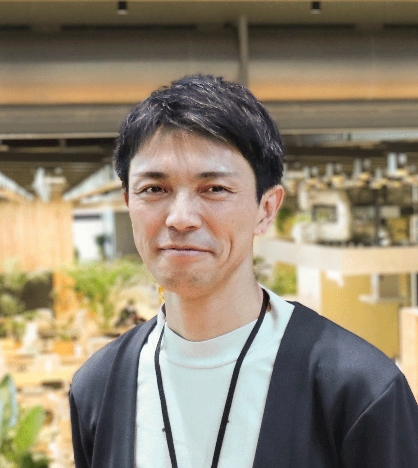
構造設計
杉山友也
3Dプリンタの新たな活用法を提言
3Dプリンタの適用を従来の型枠利用から一歩踏み出し、仕上げ材・構造体としての活用や低環境負荷型の活用、オンサイトプリントでの施工にチャレンジしました。デジタルデザインを活かした検討を行い、さらにコンピューター数値制御による3Dプリントと連動するという次世代の設計・施工連携にも一歩踏み出すことができました。まだ実案件適用の歴史は浅いですが、省人化・低環境負荷が求められる今後の社会において、有効な設計・施工手段であり、DX時代と相性の良い技術だと感じています。今後は技術の発展のみならず社会普及を目指し、3Dプリンタ技術の正しい理解やニーズの作り込みを、本案件を通して行っていきたいです。